Valmet continues to invest in R&D and its pilot facilities
Feb 11, 2020
Valmet’s Paper Technology Center in Järvenpää, Finland, provides the best available paper finishing piloting trials. To be even better and to correspond more accurately to the mill environment, the sizing section at the pilot facility has been updated with new spray beams and rolls.
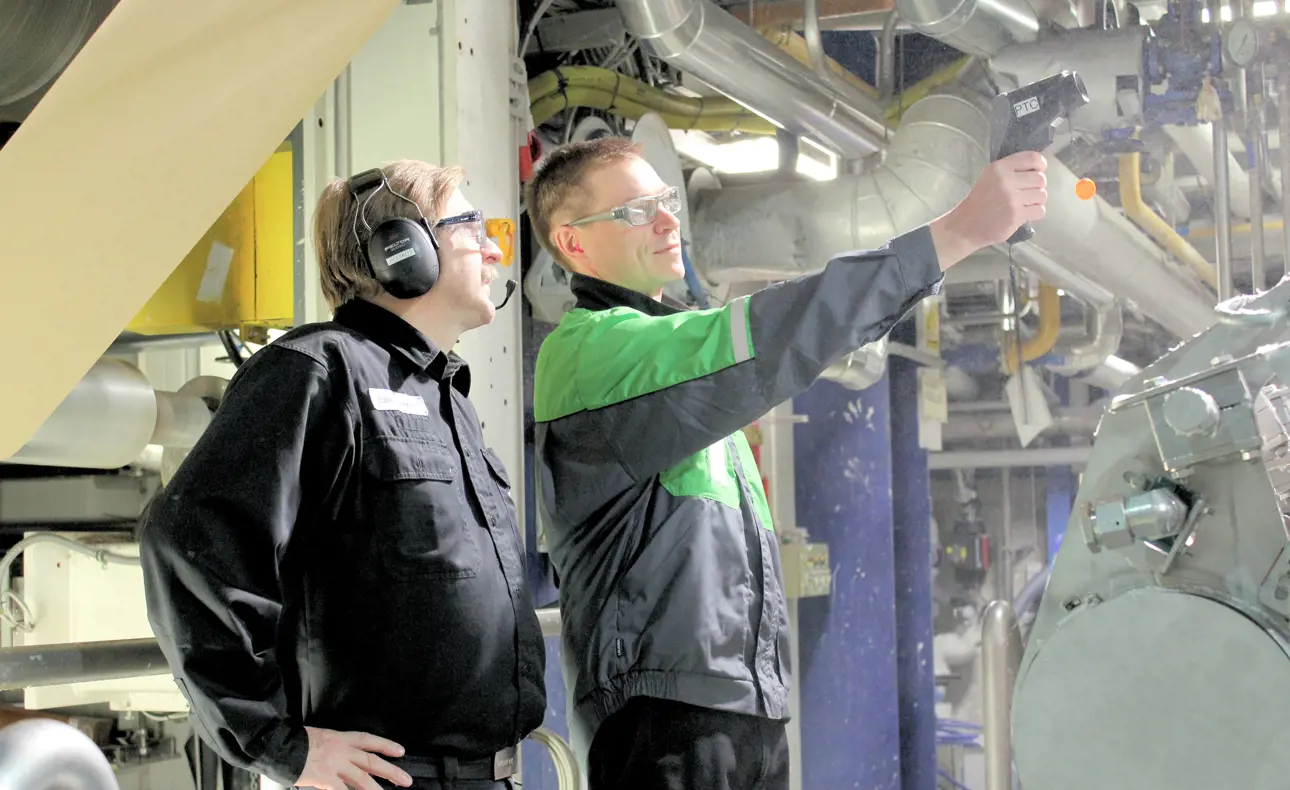
A sizer with spray application has been in Valmet’s product portfolio for quite some time. The whole sizing station was upgraded to meet the improved equipment design, but an even more important target was to be in a position to offer more efficient and accurate piloting services for surface sizing. “The rebuilding work for the pilot sizer went very well and as planned. The pilot sizer rebuild was relatively easy for Valmet because of our vast experience with rebuilds,” says Superintendent Esko Nupponen.
Narrower beams – but like the real thing
The new spray sizing beams, rolls and hard roll covers for the hard nip sizer are the most significant upgrades. They correspond closely to the spray beams in a mill-scale sizer. “In a way, our previous spray beams were a result of continuous development. We started with one type of beam and added bits and pieces as the design evolved. This is quite a normal process in R&D. However, the end result did not look professional, even if this previous R&D version spray beam was working OK,” says Superintendent Mika Linjamäki.
“With these new pilot beams, all the details and functions are exactly the same as with the mill-scale spray beams. The only major difference is the width of the machine. The pilot spray beam width is less than one meter, while the full-scale spray beam can be more than 10 meters wide. When the sizing process is well-tested at the pilot scale, the start-up curves with the new sizers at mill sites are very steep,” Development Manager Henri Vaittinen describes the improvement.
Henri Vaittinen and Esko Nupponen calculating values and figures for each trial run
Faster piloting services
Because the rebuild improves the efficiency of the pilot activities with reduced machine downtime, the sizing concept changes are shortened considerably. The structure of the pilot machine was designed for an easy beam exchange to test different sizing application methods more quickly. For example, standard film sizer can be exchanged with a novel hard nip spray sizer in just one day. Previously, changing the film sizer took three days. Concept changes can now be made in a day. “This is a real advantage when a customer wants to compare different surface sizing methods,” adds Esko Nupponen.
Preheating to imitate the paper mill environment
Experiments have shown that the sizing of hot web gives higher SCT and burst strength than the sizing of cold web. “Previously, there were cases where sizing pilot trials gave poorer strength improvements compared to the results from the mill. The sizing environment at the pilot didn’t match the paper mill environment,” Mika Linjamäki describes the starting point.
Only one week after installing the web preheating system, the results were promising: “The laboratory test results correspond a lot better to the paper mill-scale environment when the web is preheated to similar temperatures to the web exiting the drying section. A 20-degree web behaves quite differently from a web of 60 or 80 degrees,” Henri Vaittinen says.
Upgraded pilot sizer is used for R&D and customer trials
All the available surface sizing technologies
With the Valmet pilot sizer, all the available surface sizing technologies – film, spray and pond applications, with soft and hard rolls – can be tested in the most realistic and mill-like environment. These upgrades underline the fact that Valmet provides the world’s most comprehensive piloting services for the entire board and paper making process – and has the best equipment to develop new technologies for the future. You’re most welcome to come and test them for yourself!
Text and photos: Pauliina Purola
Related articles