Layering headbox increased production and reduced costs at PT. Aspex Kumbong PM 3
PT. Aspex Kumbong mill (part of KORINDO Group), located in Cileungsi, West Java, Indonesia successfully completed a grade conversion rebuild for their PM 3 from newsprint to light fluting and liner grades in 2023. The Valmet supplied rebuild consisted of a new OptiFlo Layering Gap headbox and improvements in the press section, which allowed the mill to increase production and upgrade quality to improve profitability.
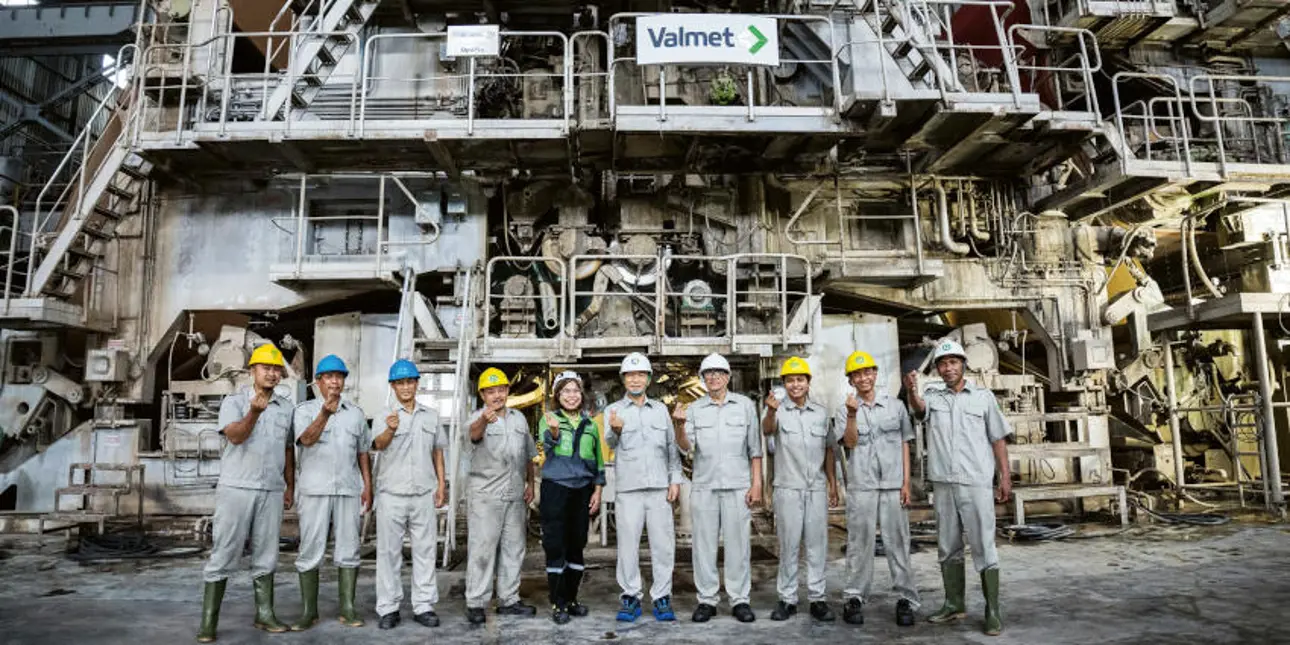
Before the rebuild, the mill was one of the largest newsprint manufacturers in Southeast Asia. They were however facing challenges related to cost competitiveness and low customer demand and were already before the rebuild producing also other grades. This led the mill to plan for a grade conversion to light fluting and liner grades. This is a trend in the current market where the consumption of newsprint and printing/writing papers is decreasing, and the consumption of containerboards or carton boards are rapidly increasing.
The target of this grade conversion rebuild was to develop new sellable grades with better quality to improve competitiveness and to increase production to improve profitability. After the rebuild, the PM 3 produces recycled liner grades in basis weight range 70 – 200 g/m2, such as base paper for beverage, snack and vegetable boxes, envelope paper, rice wrappers and construction paper.
All guaranteed values have been reached and quality has been good from the beginning. CD profiles are even, orientation profiles are good, and uniformity in customer rolls has been very good.
References and troubleshooting skills played a key role in supplier selection
According to PT. Aspex Kumbong mill the main factors to help paper makers to stay competitive are ability to delivery good quality products at the right price, to have a stable and cost competitive production, and to continuously communicate with technology suppliers to know about the latest technologies that can help keep the production competitive.
Comparing suppliers and selecting the best partner to team-up with is an important part of a rebuild project to help reach these targets and make the project go more smoothly, and minimize risks at every step, from planning to delivery to start-up. PT. Aspex Kumbong was convinced that Valmet could help them achieve the set targets with their PM 3 grade conversion rebuild. Main reasons behind this were the multiple credible technology references Valmet was able to present, quality of the delivered equipment and the trouble-shooting skills Valmet demonstrated.
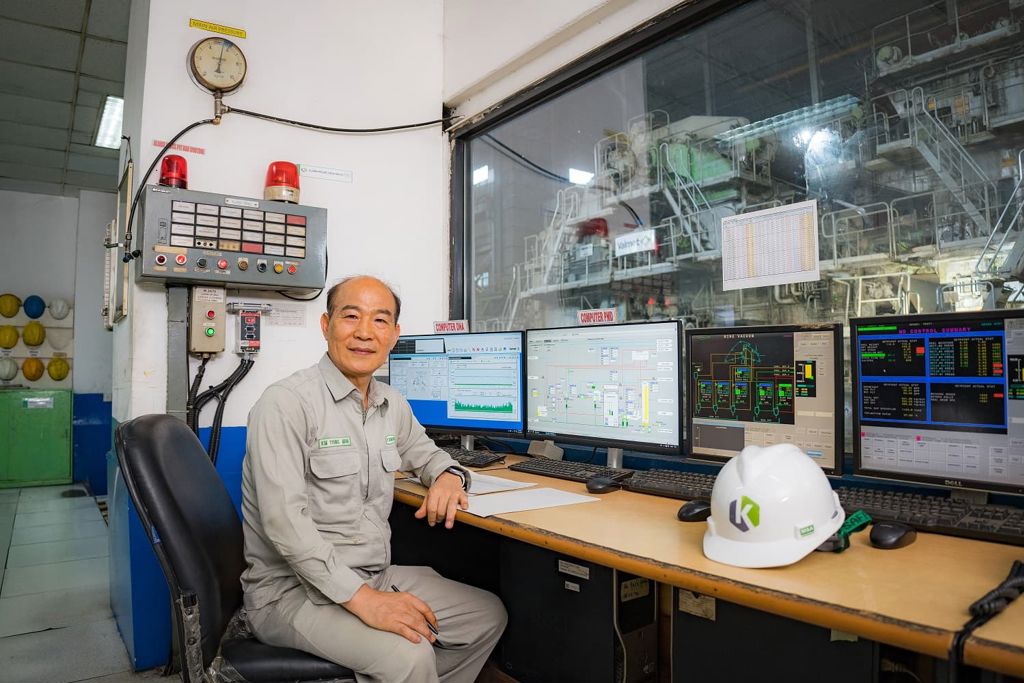
Novel layering headbox technology ensures targeted quality
Key factor in the PM 3 grade conversion rebuild was replacing the old headbox with a new OptiFlo Layering Gap headbox. This novel headbox technology makes it possible to produce lightweight containerboard grades with two layers with only one headbox and one forming unit. While comparing to the old and traditional technology, the new headbox has required the mill to learn to operate the layering headbox technology, but despite of this the mill has been very satisfied with the new technology.
The end-product quality has been on the targeted level right after since the start-up. According to the mill all guaranteed values have been reached and quality has been good from the beginning. CD profiles are even, orientation profiles are good, and uniformity in customer rolls has been very good. These are enabled with the ejector type dilution system and patented CD dilution profiling with edge feed control. Effective and zone-controlled mixing of dilution water and pulp flow provides narrow and accurate dilution response. The redesigned hydraulics using accelerating secondary tubes provide better turbulence and flock breaking power and deliver a more uniform and stable headbox jet to the wire.
After the rebuild the mill has been able to dye only the print ply, which has resulted in significant cost savings in dye and retention chemicals.
In two-layer headbox applications, it is very important to guarantee layer coverage. On PM 3 the layering headbox has enabled the mill to better control the quality and profiles for the different layers. After the rebuild the mill has been able to dye only the print ply, which has resulted in significant cost savings in dye and retention chemicals.
From maintenance perspective, the mill has been very pleased with the new layering headbox. Maintenance has been said to be “easier than ever”, and the headbox tilt and gap adjustments get praise for allowing easy inspection and cleaning.
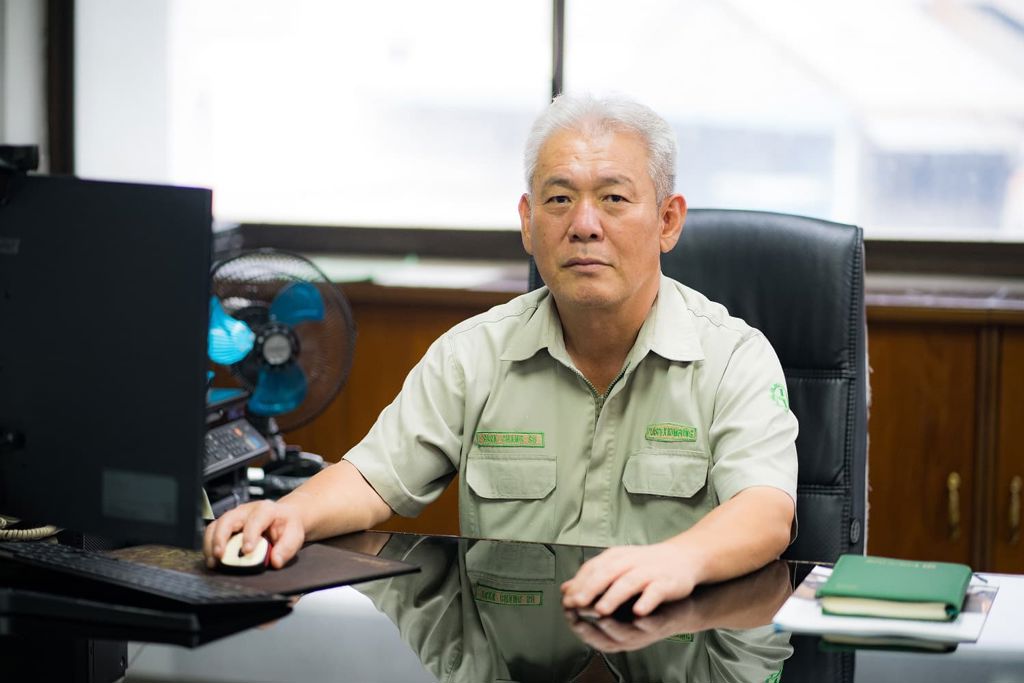
Press section improvements improve runnability and reduce draw
In addition to the new layering headbox, also the area between press and dryer section was rebuilt with Valmet Press Run Web Stabilizer. The aim was to reduce sheet breaks, improve runnability, avoid wrinkling and reduce draw between the press and dryer section. The old layout also included a grooved paper lead roll which contaminated easily due to stickies and needed maintenance with short intervals. The new layout enabled removing this roll, also reducing the maintenance needs.
After the rebuild the press to dryer draw could be reduced up to 40 % with still maintaining flawless paper runnability. The cleanliness issue in the area was improved significantly.
Maintenance has been said to be “easier than ever”, and the headbox tilt and gap adjustments get praise for allowing easy inspection and cleaning.
A successful grade conversion
Grade conversion adds an extra layer of complexity to a rebuild. Not only learning to operate the new equipment, but the mill also must learn how to produce the new grades and understand the new production parameters to produce the targeted quality. The PM 3 project faced it challenges prior commissioning due to COVID times and the difficulties it posed to site work, but the challenges were overcome, and the PM 3 grade conversion rebuild was a success for PT. Aspex Kumbong mill. The targets of increased production, improved profitability and better quality were successfully met. Their customers have accepted the new products and their quality and expansion to new markets and customers continues.
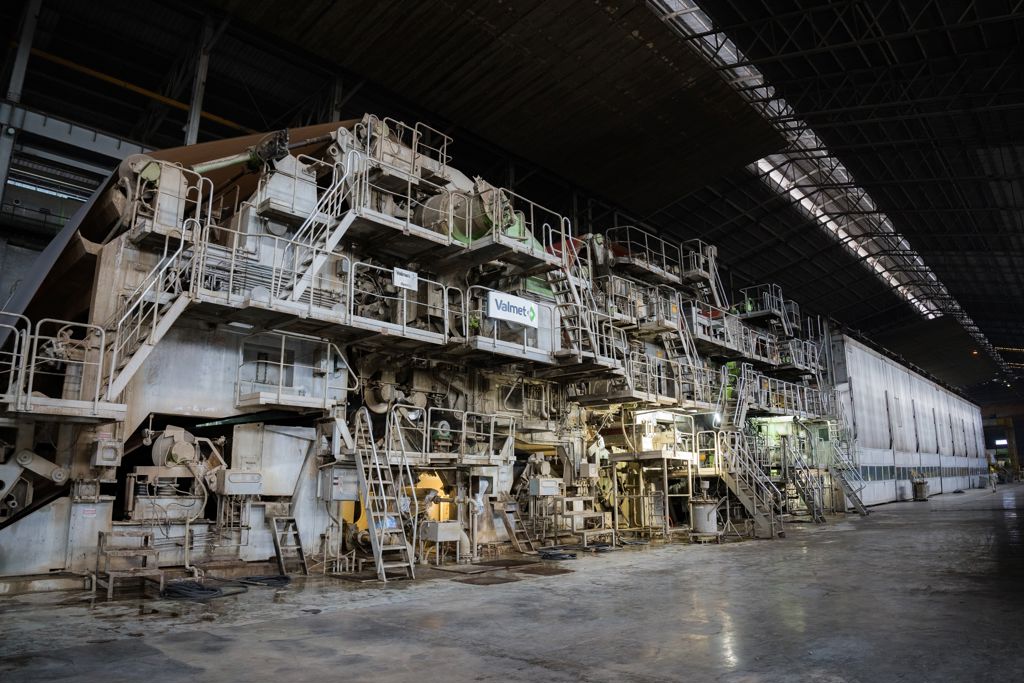
Text: Elsa Sinjaga, Weeraya Netwong and Hyun Hee Kang
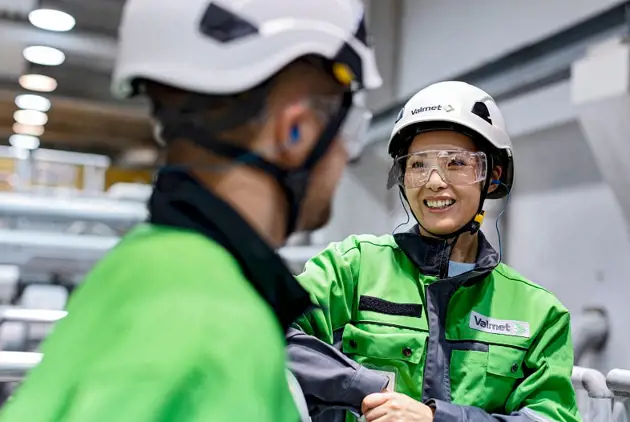
Want to talk to our board & paper experts?
If you wish to get further information like technical specifications or details, need a quotation, or wish to discuss different solutions, fill in the contact form and our experts will contact you shortly.
Contact our expertsOptiFlo Layering Gap headbox – High-performance layering gap headbox for demanding gap forming applications
Layering headbox makes it possible to produce lightweight containerboard with two or three layers with only one headbox and one forming unit. This layering headbox solution enables feeding different stock into each layer, which in turn means that the structure of board can be further optimized. This high-performance headbox is an ideal solution for layered applications, to meet today’s high board making demands on containerboard production.
Excellent layer coverage
In two-layer and three-layer headbox applications, it is very important to guarantee layer coverage. All hydraulic components of the OptiFlo Layering Gap headbox have been designed to minimize slice jet and board sheet disturbances. This novel solution provides excellent layer coverage, considerably lower residual variation in basis weight as well as an excellent formation with no streaks or tiger stripes. The headbox hydraulics and white water automatic dilution design produces smooth forming board activity, without any mixing of individual layers.
Cost efficient layering headbox concept
Having two or three separate headboxes is a much bigger investment compared to a layering headbox. But the cost savings do not come only from the initial headbox investment. There are possibilities for great operational cost savings as well. With two or three headboxes you have wires running with all of them consuming water and chemicals. These require cleaning and changing wires, which take a lot of time. All of these create a higher operational cost compared to a layering headbox. So, it is not only about the initial headbox investment, but also consider the cost savings in energy, chemicals, and consumables which a layering headbox can help you achieve.