Sustainable board making at Anhui Shanying
Shanying Paper’s two new paper machines produce lightweight yet strong recycled containerboard. Both machines have steam consumption as low as 1,5 tonnes per tonne of board produced. Their aim is to be competitive in the market by using less energy and raw materials.
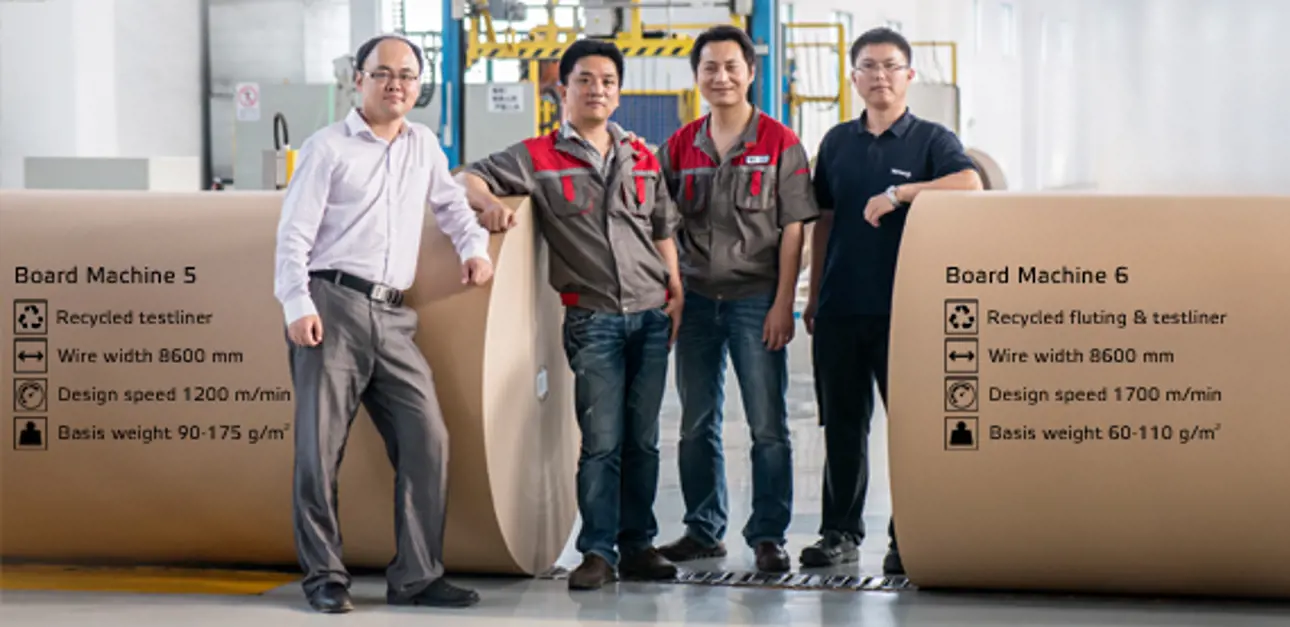
1st gap former for Chinese containerboard makers
Shanying Paper made the largest investment in the company’s history by investing in two new, Valmet-supplied containerboard lines at its plant in Ma’anshan, in Anhui Province in China. The high-quality recycled containerboard lines have been up and running for more than a year now, producing 1,000,000 tonnes of board a year.
The driver behind the investment in two new high-quality production lines (PM 5 and PM 6) was the need to adjust Shanying Paper’s production structure to fulfill market needs and to be more competitive. The concept of PM 5 is based on effective hybrid forming technology, while PM 6 is based on gap forming technology. Making lightweight containerboard using gap forming technology is new for Chinese containerboard makers. The most efficient European containerboard lines making high-quality lightweight end products utilize gap forming concepts with excellent results. Now, Shanying Paper has taken this step with Valmet’s technology.
“We evaluated Valmet solutions especially from the technology and energy consumption perspectives and compared them with other suppliers’ solutions. We found that Valmet can offer the most optimized package for producing lightweight yet strong containerboard”, says Zhan Zhengfeng, General Manager of Anhui Shanying Paper Industry.
Sustainable board making saves both energy and raw materials
In the containerboard business, the trend is towards lighter yet stronger end products produced using less raw material and energy. “The environmental efficiency of PM 6 in terms of energy consumption and raw material efficiency is totally beyond our expectations – much better than the industry standards,” comments Wang Yong, Mill Manager of Shanying Paper. He continues: “We have achieved electricity consumption of 450 kWh/tonne and steam consumption of 1.5 tonnes per tonne of paper, which makes us very competitive in the market”.
PM 5 has been running successfully since start-up as well. The most beneficial features of the production line are the high end product quality, the stability of the process and its overall safety. “The environmental advantage of this line is its very low water and steam consumption. The fresh water consumption per tonne of paper is six tonnes, and steam consumption is 1.5 tonnes,” explains Zhang Xianrong, Mill Manager of Shanying Paper PM 5. The material efficiency is very high. “The initial target of PM 5 was to produce one tonne of paper by using about 1.15 tonnes of waste paper, but we have reached the level of 1.12 tonnes,” says Zhang Xianrong.
|
”Over one year of operations proves that these machines run very smoothly and are easy to maintain.“
|
|
|
Song Zhiming, Maintenance Manager of Anhui Shanying Paper Industry
|
|||
”We evaluated and compared solutions especially from the technology and energy consumption perspectives. We found that Valmet offers optimized package for producing lightweight yet strong containerboard. “ Zhan Zhengfeng, General Manager of Anhui Shanying Paper Industry |
|
![]() |
|
|
“Automation is the brain of the machine, and only advanced systems let the machine produce the best results."
|
|
Liu Wenming, Chief Engineer of Anhui Shanying Paper Industry
|
Smart combination of machinery and automation
Shanying Paper PM 5 and PM 6 are equipped with full Valmet DNA automation systems, including process control and quality control, as well as condition and runnability monitoring systems. This kind of extensive overall delivery package from the same supplier enables the design of highly energy-efficient production lines. It also provides decision-makers with the data they need to make the right decisions. One supplier providing both machinery and automation systems can make the paper machine run more smoothly and bring its superiority into full play.” The union of the latest board-making technology and full automation system saves both money and effort. According to Liu Wenming, Shanying Paper Chief Engineer: “Automation is the brain of a paper machine, and only advanced systems let the machine produce the best results”.
Experiences after one year operation
The PM 5 and PM 6 start-ups were successful, with good results. PM 6 set a 24-hour average machine speed record of 1,398 m/min only 12 days after start-up. After three days of operation, the machine was already producing saleable products. “During the installation of both machines, Valmet’s very professional installation team provided us with guidance and technical support. Over one year of operations proves that these machines run very smoothly and are easy to maintain. Our staff are able to visit Valmet Wuxi Service Center for training, which has improved our technological capabilities and ability to maintain two machines”, says Song Zhiming, Maintenance Manager of Shanying Paper.
Shanying Paper's high-quality recycled containerboard lines PM5 and PM6 produce 1,000,000 tonnes of board a year.