Ranheim Paper & Board invested in an efficient heat recovery system leading to 14% savings in energy consumption
Cold working environment and quality issues led Ranheim Paper & Board to invest in Valmet’s heat recovery system OptiAir Recovery. As a result, the mill achieved savings in energy and a significant increase in production.
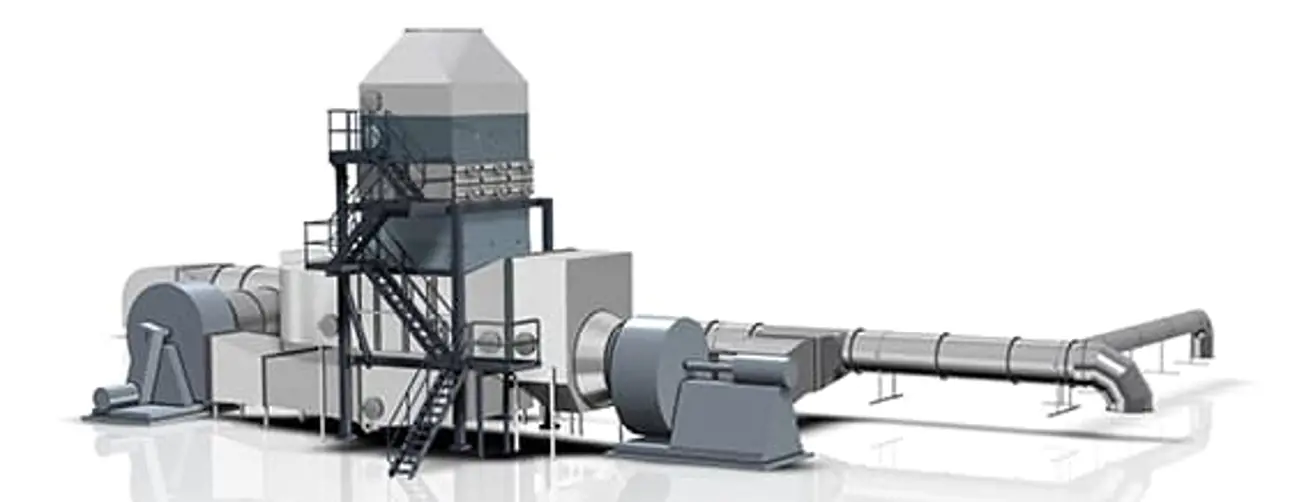
Located in Trondheim, Norway, Ranheim Paper & Board is one of the world’s most northern paper mills. Today, it’s two main product segments are saturating base paper that is used for laminating in building industry and paper and boxes for the local and international fish market.
With nearly four decades of experience in paper and board making, Managing Director Øistein Vedahl has led Ranheim’s operations since 2018.
“To be honest, I was shocked when I first started. The working environment in the converting area was really challenging – cold temperatures and extremely dry air was hard for our employees, but it eventually caused quality issues, too. The top sheets were curling and wouldn’t go through the cutters, leading to excess waste. Converting had become the bottleneck in our growing production of fish boxes”, Øistein says.
Audits revealed the root causes for the challenges
To define the investment scope the current situation was investigated through several audits.
“First, we performed a heat and energy consumption audit on PM5 and concentrated especially on the process water. We found out that the process water was too cold leading to limited production. In the converting area climate audit, we saw that in addition to the extremely cold working conditions the consumption of primary energy was high, and the converting machine was not working optimally”, summarizes Håkan Hannus, Sales Manager, Air Systems, Valmet.
To warm up process water Valmet’s solution was to install heat exchangers in the dryer section exhaust and gas infra-dryer exhaust. The temperature of the converting area was increased by installing a completely new climate control system using recovered heat from the mill’s other paper machine (PM6).
“There was a lot of potential for improved heat recovery both for heating up the converting area and the water system temperature of PM5. The energy costs dropped dramatically as we could replace the costly direct electrical heating by recovered heat in the converting hall”, Håkan explains.
Outstanding results
The project was originally planned to take place in 2020, but due to the global pandemic it was delayed and finalized in the beginning of 2022.
Our original goal was to achieve 11% savings in energy, but we reached a very satisfying 14%. However, the big thing really is that we saw an outstanding 15% increase in production just because of the higher temperature in the mill’s white-water system. Despite the delay and a slight cost increase we are very satisfied – the payback of this investment was only one cold winter”, Øistein says.
“The temperature of the converting area is now 21 degrees with stable humidity, all year round, improving both the working environment and the product quality. In addition, the new heat recovery system also has a positive effect on our environmental footprint – we have been able turn waste into something worthy”, he adds.