Collaboration and teamwork maximizing the fiber saving results at Progroup PM2 line´s OCC process
Progroup recently completed a successful improvement project on its coarse screening process for PM2 OCC line in Eisenhüttenstadt, Germany. The project aimed to reduce fiber losses and optimize the performance of the OCC line. Franziska Ströse from Progroup and Outi Kukkamäki from Valmet shared their experiences and insights on the background, challenges, and outcomes of the project.
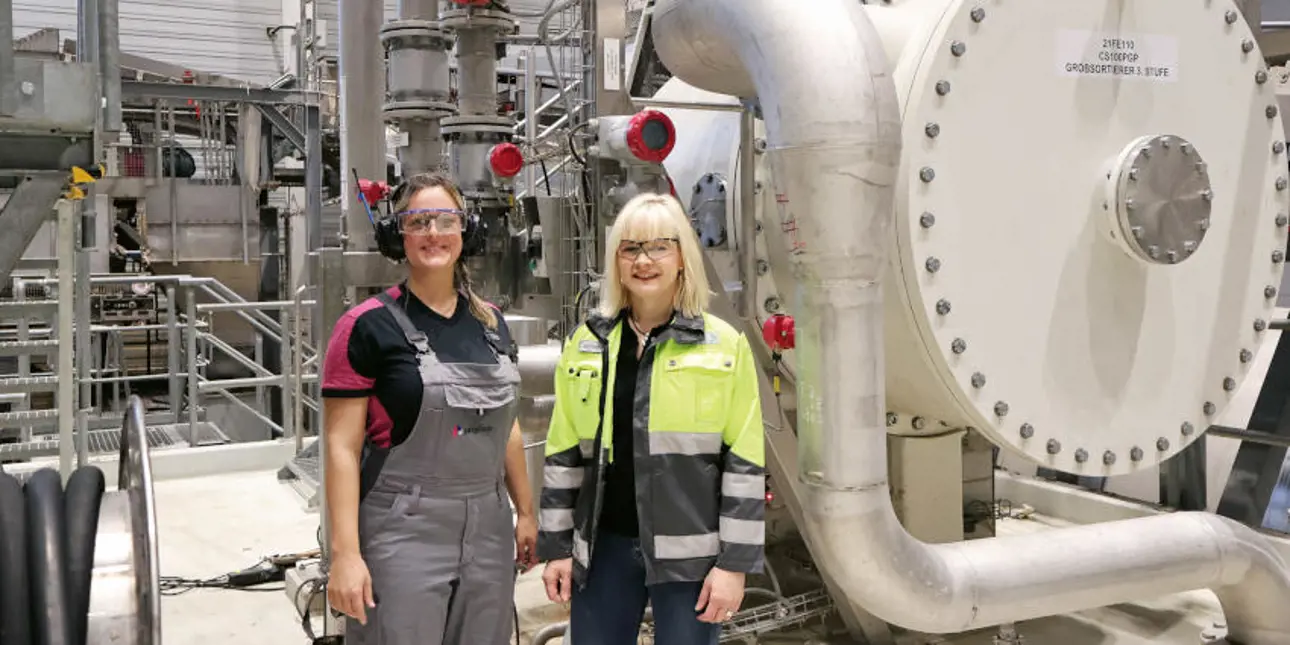
Franziska Ströse from Progroup and Outi Kukkamäki from Valmet
The background
Progroup, a family-run company in Central Europe, holds the incredible eight world records for the fastest paper machine in the world. Progroup´s PM2 in Eisenhüttenstadt, Germany, features Valmet´s paper making and automation technology from the recycled finer line (OCC) and stock preparation plant to the OptiConcept containerboard machine. Besides the world record speed, PM2 also has the world´s largest OCC drum pulper with high production capacity.
Progroup produces high-quality corrugated board base papers exclusively on the basis of recycled material. Company´s investment in continuous development, committed employees and cooperation with suppliers was also building the remarkable results of recently renewed coarse screening process in the PM2 OCC line.
“The idea of the project was to maximize the use of raw material to improve the fiber efficiency,” says Franziska Ströse, Plant Engineer, Technology & Development in Progroup. “The OCC process has three important steps for saving fibers: drum pulping, screening, and cleaning. We decided to focus on the coarse screening, where we observed a lot of fiber losses on the conveyors. Aim was to find a way to recover and reuse those fibers, which would improve the quality and quantity of the paper output.”
When improving the whole operation of coarse screening process there were few important factors which were planned carefully during the project engineering phase: screening efficiency in quality wise in first stages, deflaking of the fiber bundles in last stages, removal of high density particles and reject consistency and plastics removal at the final stage.
The power of cooperation
Designing an improvement to existing line creates its own challenges with layout and integration. One of the biggest challenges was to rebuild the old machines and install the new machines in a running system, without disrupting the paper production. The project team had to plan carefully and coordinate with the operators and the maintenance staff to execute the project smoothly and safely.
”In order to improve the efficiency of the coarse screening process, the entire process from screening and cleaning to deflaking and reject consistency was examined. We began by rebuilding the Valmet High Consistency Cleaner, which was out of its operational window. To address this issue, we designed a tailor-made solution that utilized the reject end valves and reject zone. The new cleaner cone was designed to be suitable for the current flow range, which improved the cleaning efficiency.”, says Outi Kukkamäki, Senior Sales Manager at Valmet´s Stock Preparation and Recycled fiber business unit.
“Next, we focused on the first deflaking equipment in coarse screening, the 3rd stage screen. To understand how much more deflaking efficiency was possible in theory and where the most reasonable target was in terms of energy intake, we used the flow simulation technology, Computational Fluid Dynamic systems. Based on these studies, we set the deflaking energy to a level where we could clearly improve the deflaking without increasing power consumption unnecessarily. The last stage equipment was insufficient in terms of reject consistency, so we selected a new type of screen to improve reject removal in higher consistency. Finally, we checked and planned all the equipment for the new target and made some changes in controls, and pipings to get the best possible outcome of the project,” Kukkamäki explains.
“One of my personal goals on this project was to gather the know-how inside our own organization from PM1, PM2 and PM3. We had an excellent team both internally and with Valmet and were able to improve some parts of the process based on this know-how. There were so many people involved from electrical and mechanical department, piping, automation and operations. We continuously improved and adjusted the plans based on ideas and discussions from our experts. And had fun as a one team,” says Ströse.
“In the design phase we prepared for various situations that could arise during the project, such as power failures, machine breakdowns, or process disturbances. We anticipated the possible scenarios and had prepared plans to deal with them if anything would happen. Cooperation between our team and Progroup experts was seamless, and our customer created an open dialogue which improved the project communications greatly,” Kukkamäki continues.
Reaching the fiber recovery targets with new coarse screen
The improvement project achieved Papergroup´s main goal of saving fibers in the coarse screening process. The fiber losses on the conveyors were reduced significantly, translating into improvements in the yield and the profitability of the board production. After start up and optimization, the amount of good fiber in the reject was reduced almost 70 %.
“I think one of the reasons for the successful upgrade was that we were able to work closely with Valmet and use our experiences from other lines. I was proud to see how much everyone wanted to help and support to make this project a success. We found suitable technology and were able to reach our targets for the upgrade. And we continue the development work with Valmet and aim to optimize the process continuously,” Ströse concludes.
After start up and optimization, the amount of good fiber in the reject was reduced almost 70 %.
Related articles