Maximizing operational performance of the OCC process with screening and cleaning
Oct 31, 2023
Recycled fiber processing is all about taking the most out of the raw material. Again and again. To ensure best efficiency and yield, we need to understand the optimal solutions for screening and cleaning furnish in the stock preparation process. We interviewed Valmet´s Process Technology Manager, Jim Burns, to learn more about the world-leading fiber recovery technologies in the OCC process.
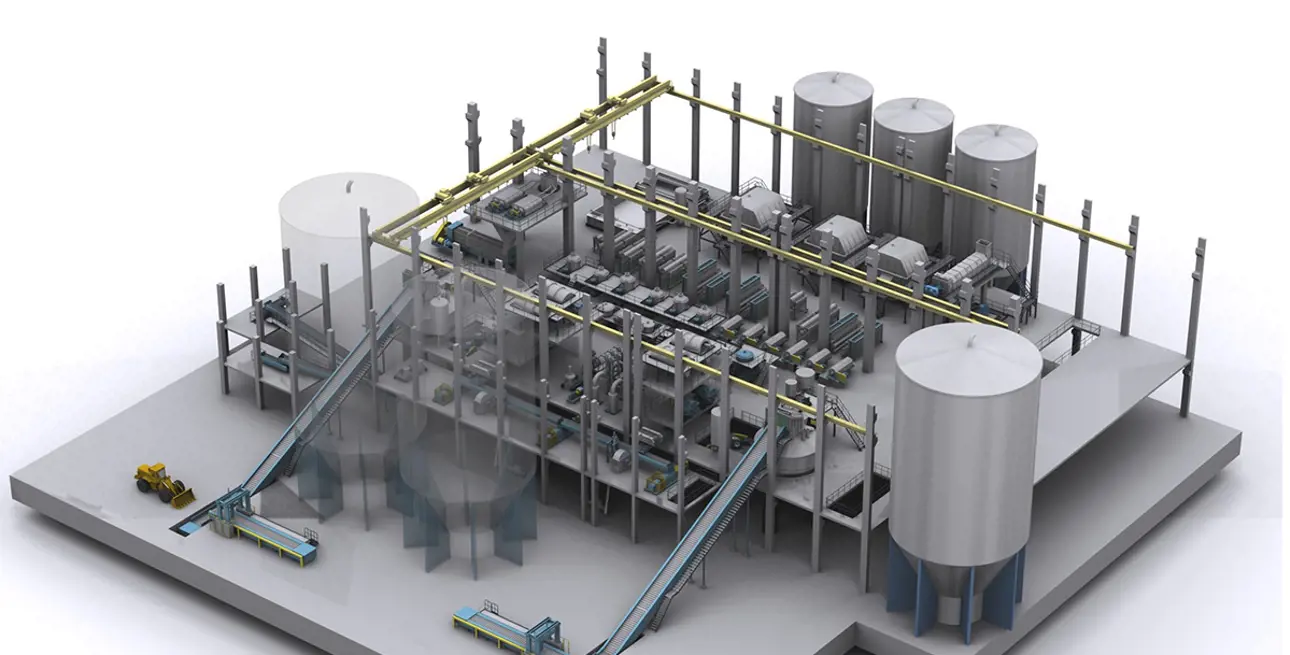
What new developments have there been for the screening process lately?
Coarse screening ensures stock cleanliness for the smooth runnability of the screening stages. As coarse screens must effectively remove medium sized contaminants and flakes from the pulper accepts, we have a Valmet Coarse Screen using slots instead of holes for enhanced debris and sticky removal. Screening process is a multivariable optimization task of mass reject rate, slot size and velocity, basket configuration, rotor parameters and system temperature.
Many of the contaminates are three dimensional where slots are found to be more selective. In addition, Valmet utilizes a CSi Screen following our primary coarse screens to remove plastics and provide a shear force to reduce un-defibered flakes. The plastics are collected in air core and are rejected while the acceptable material is accepted through a low-profile impeller and a 3 – 5 mm fine hole grate.
Why should we use fractionation in the OCC line?
Fractionation selectively classifies the recycled fiber to optimize board-making potential and enables exclusive dispersing and refining of fibers that have high strength potential. This brings energy savings and secures and homogenizes the targeted pulp quality.
Fractionation is a tool to direct our investment and energy focusing on long fiber fraction instead of all of the fiber stream. This way we can optimize the long fiber cleaning and screening as well as the fiber development.
What should we know about cleaning the recycled furnish?
Cleaning the furnish in OCC line is a major unit operation in the recycled fiber process, as it involves removing contaminants and impurities to ensure the final product meets quality standards. Furnish can contain various contaminants, including adhesives, dirt, plastics, and other foreign materials. These contaminants must be removed to produce clean stock from recycled materials. Cleaners utilize the differences in specific gravity of the contaminants, consistency, and centrifugal force.
Valmet’s cleaning solutions for OCC processes include high density cleaners for heavy contaminants as well as low-consistency forward and reverse cleaners for finer heavy and light weight contaminants. The cleaners are positioned in various sections of the OCC process to optimize the contaminant removal operation.
High density cleaners are found after the pulpers before the coarse screens. Typically, high density cleaner rejects contain stones, metal pieces, concrete and big staples that will damage downstream equipment. Valmet has a two-stage high density cleaning system. The primary stage continuously rejects to the Valmet Reject Separator, which is a low G-force sedimentation vessel. This allows larger heavy material to separate and settle before the second stage feed pump thus protecting it and last stage cleaner. The heavy material is discharged from the Valmet Reject Separator via an automated junk trap. The last stage cleaner has discontinuous rejects to minimize fiber loss.
Low consistency forward cleaners are designed to achieve high G-Forces and longer retention time for optimal removal of fine heavyweight particles such as sand. Our Valmet Hydrocyclone Cleanpac 700 MCD cleaner is our high efficiency cleaner specifically designed for OCC. The patented mid-cone dilution technology reduces thickening and recovers useful fiber from the reject material. The Valmet Hydrocyclone Cleanpac 700 MCD can also be configured as a combination cleaner for both heavyweight and lightweight contaminants.
Low consistency reverse cleaners are designed for efficient removal of lightweight contaminants from the fiber stream. The Valmet Hydrocyclone Slidepac cleaners are Valmet’s most efficient cleaners for lightweight contaminant removal. Although one would wonder why cleaners seem not to have independent valves, our unique satellite header arrangement offers a compact arrangement for the cleaners. The cleaners are not a single piece and the wear area at the bottom of the cleaner can be changed without removing the entire cleaner. The Valmet Hydrocyclone Slidepac RT pressure drop is ~28 - 30 psig and will increase the cleaners accepts consistency reducing downstream thickening requirements. In addition, Valmet has other options for lightweight cleaning with individual isolation valves also if desired.
Read more about Valmet´s OCC technology