Integrating lines to unleash flexibility
Dec 5, 2024
Phase two of Klabin’s Puma II Project in Brazil has successfully started up, with a bleached chemi-thermomechanical pulp (BCTMP) line and fiberline integrated with the new PM 28 board making line. Together, they increase the flexibility of production and introduce a high-quality end product.
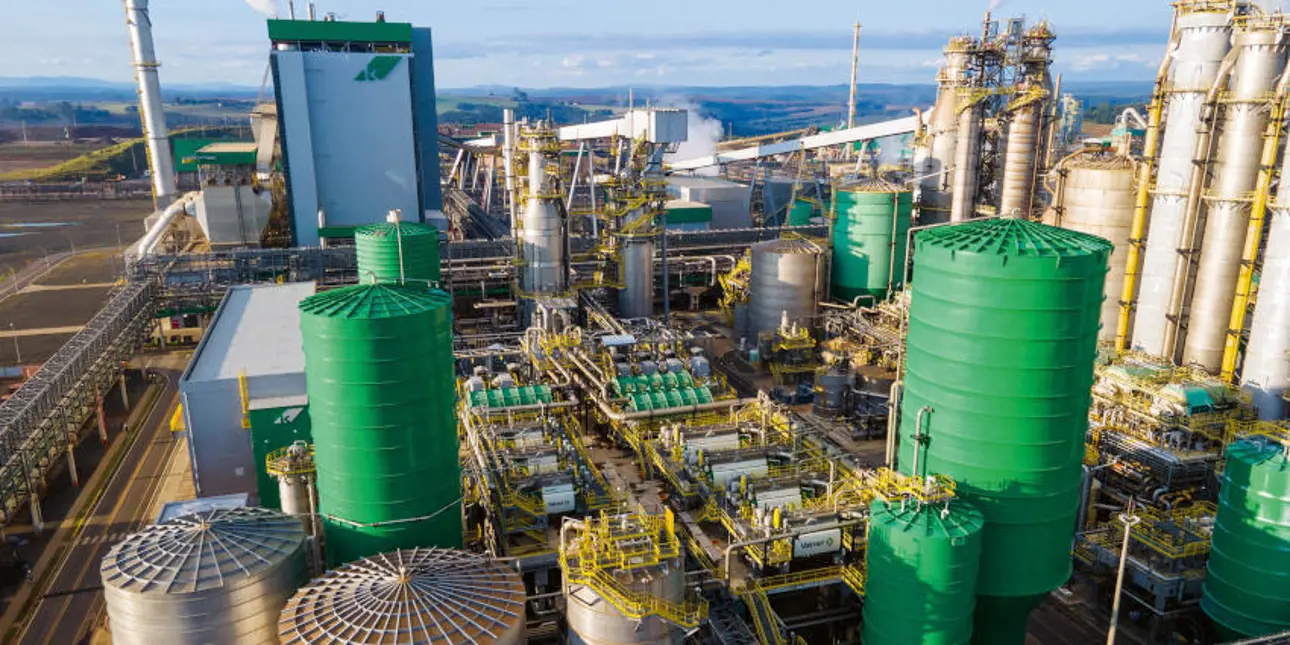
The new PM 28 board making line has an annual capacity of 460,000 tonnes, which makes Klabin more complete and enables them to withstand market volatility as one of the world’s leading producers of coated virgin fiberboard and kraftliner.
An investment in sustainability and flexibility
Klabin has had a fantastic history of investments over the past 15 years. “We’ve practically doubled the size of the company and its results,” says Francisco Razzolini, Executive Director of R&D and Sustainability at Klabin.
“We’ve focused strongly on potential markets where Klabin has opportunities to grow. We saw early on that the packaging paper segment was an attractive market. It had great potential for growth, as the market began to use products sustainably and renewably, with recyclable and even biodegradable products. Reducing the effects of climate change was a key factor when we were planning the Puma project. We strive to reduce our carbon footprint and rationalize the use of our natural resources,” says Razzolini.
Both paper machines have Valmet DNA Distributed Control Systems (DCS), Valmet IQ Quality Management Systems, and Valmet Industrial Internet solutions.
Excellent paperboard with fantastic print surface
The PM 28 project involved modifications in the fiberline to introduce the production of high-yield pulp – BCTMP. This has a very important function in board production, providing the highest possible volume and guaranteeing the best stiffness.
With the new PM 28 machine, the print surface is absolutely fantastic.
“We’re very pleased with the results so far. The highlights of PM 28 include technological innovations, especially in the high-quality corrugated board market, with differentiating end products like 8k coated white top kraftliner that complement our product portfolio. That product has proven to be excellent, and the print surface is absolutely fantastic. This is one of the big advantages of the flexible new PM 28 machine,” he continues.
Successful project implementation
“The success of the project implementation was based on the good relationship between the Klabin and Valmet teams. Together, we’ve worked closely on everything, from system design and installation to assembly and commissioning,” he says.
“We learned a lot from Valmet during the first project phase, with the upgrade of the MC 26 pulp drying machine and the new PM 27 line. When the PM 28 project was about to start, we already had a good idea of what had gone well, and where there was room for improvement. Looking back, it seems to have been an easy project, but every day was filled with great excitement. We wondered when we would get more control over the pandemic, and life would get closer to normal. Challenges emerged throughout the project, but the people who implemented it always had the ability, discernment, and dedication to make things happen,” explains Razzolini.
Francisco Razzolini, Executive Director of R&D and Sustainability at Klabin.
A very strong development focus
One of the increasing challenges in growth and continuous technological development is to use fewer resources to produce more. Today, the focus is on improving the properties of paper and improving operational performance with less energy, steam, fuel, chemicals, and fiber to achieve the results.
“Research, development and innovations have gone very far in this direction, and Klabin’s partners must have a very strong development focus. It’s essential for us to have technical development, and that our partners also carry out this development with Klabin. This is how we can always achieve better results, better quality, and better products with the related environmental improvements and social progress,” says Razzolini.
Shared vision and continuous learning
The work Klabin has carried out with Valmet in recent years has firmly anchored the two companies’ relationship. “We have a fantastic relationship. We share visions of global and sustainability growth, the pursuit of innovative technology and reliability, continuous improvement of all industrial processes, and increasingly incorporating autonomous development and control systems with a lot of application of digital technology,” Razzolini says.
“We’ve made progress and achieved results, but it doesn’t stop there. We’ve now completed a major investment process, and the learning curve continues. New technologies are coming, and we’re ready for new challenges. With our team and Valmet, I’m committed to continuing to meet this challenge and increasingly improving our competitiveness and the sustainability of our products, our companies, and the global market,” he concludes.
Text Kerstin Eriksson
Puma II Project
The Puma II Project’s first phase included a completely new Kraftliner PM 27 line, fully focused on eucalyptus brown pulp and all utilities. It is the first line in the world to manufacture kraftliner with 100 percent eucalyptus – called Eukaliner®. For the second phase of the project, Klabin’s team decided on a flexible new paperboard making line.
This included the BCTMP and fiberline integrated with the new PM 28 board making line, which can produce a large variety of board grades, from kraftliner to coated boards, like folding box boards (FBB) and liquid packaging boards (LPB).
PM 28 scope of delivery for Puma II project phase 2:
- Continuous Cooking G3
- High-yield pulp BCTMP line
- Fiberline upgrade with an increased capacity
- Complete automation package with APC, analyzers, and measurements
- Valmet Industrial Internet solutions
- Stock preparation and approach flow systems
- Coated board making line (PM 28), from headboxes to reel, winder, and roll handling systems
- Coating Color Kitchen
- Appr. 2,400 valves for the new line’s reliability.
Related articles