Flexibility and stable quality for specialty paper production with new headbox
Specialty paper manufacturer Papelera de Brandia, S.A. was facing declining market shares. They invested in a new OptiFlo Fourdrinier headbox that has enabled them to improve and stabilize product quality as well as improve productivity. This has resulted in better competitiveness and in increased market shares.
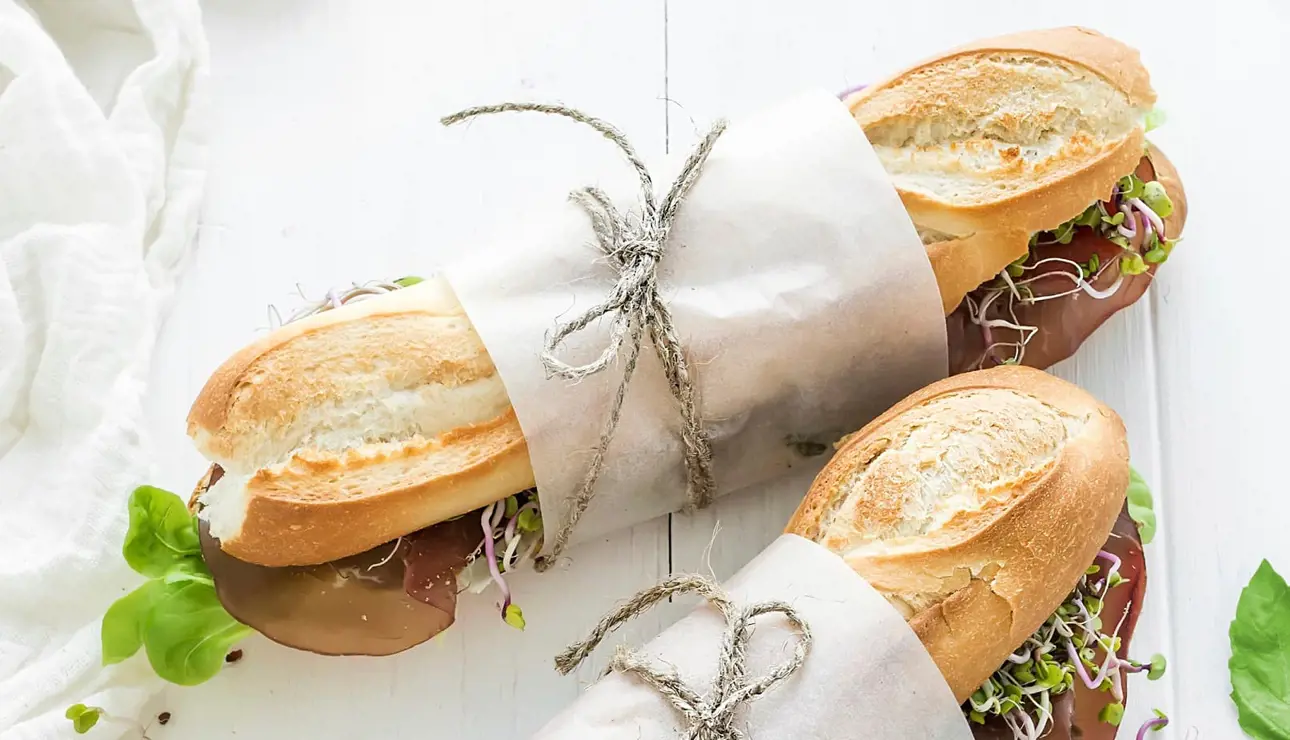
Investment to improve competitiveness and increase market shares
Brandia is known for their high-quality white MG kraft paper, renowned for its high gloss, brightness, and excellent machinability. Majority of their production goes to the food sector for flexible packaging, bags, form and fill packaging for high-speed automated packaging process, and many other applications in basis weight range from 24 to 165 g/m2.
There were two main reasons why Brandia started looking for improvements for their PM 1, explains Gaspar Barreras Rodriguez, General Manager, Brandia. First, the machine was not that old in years but old in terms of technology and did not allow further improvements to be achieved in quality nor in productivity. Second, Barreras continues by stating that increasing machine speed and improving and stabilizing quality at the same time are difficult to achieve simultaneously. This was however something Brandia needed to get to in order to improve their productivity to boost competitiveness and increase their market shares.
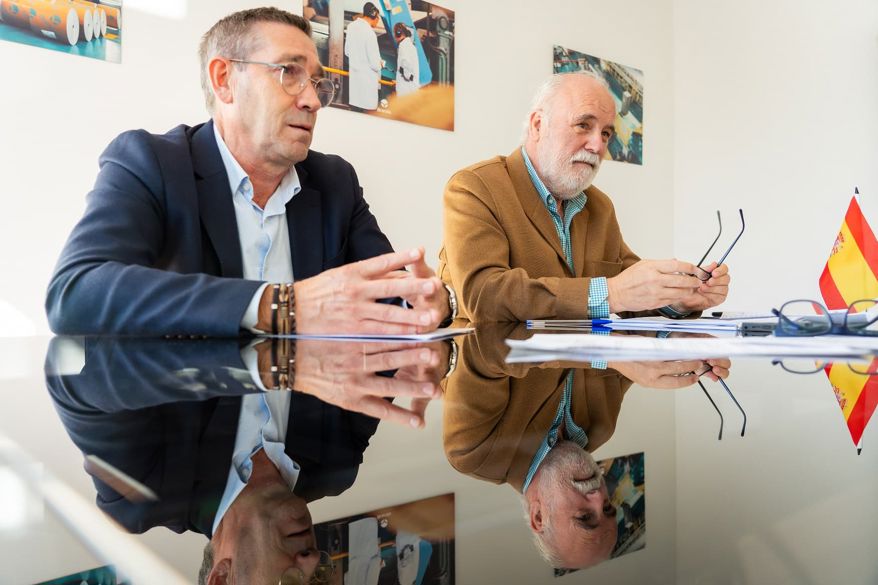
The production with PM 1 is characterized with small batch orders that each have very specific needs in terms of grammage and quality. Some customer orders might be as small as in some kilos, which makes the daily production changes very challenging.”
Capacity increase, faster grade changes, efficient raw material usage and lower energy consumption
Francisco Javier Vazquez Lopez, Technical Director, Brandia explains that: “the production with PM 1 is characterized with small batch orders that each have very specific needs in terms of grammage and quality. Some customer orders might be as small as in some kilos, which makes the daily production changes very challenging.” Vazquez continues saying that Brandia is committed to serving their customers even with these highly specific orders. The new OptiFlo Fourdrinier headbox gives Brandia the needed flexibility for their production, making it possible to serve even these most demanding customer needs efficiently and profitably.
With this type of small batch production, fast grade changes are the key to efficient and profitable production, Vazquez explains. The new headbox has enabled this, which helps Brandia to minimize both raw material and chemical consumption and costs, that contribute highly to the increased production capacity. In addition, the machine line energy consumption has decreased by 15 percent. Barreras continues saying that Brandia has improved on average up to 25 percent on majority of the key indicators that they follow.
When comparing to the old headbox Vazquez says that: “the operation of the new OptiFlo Fourdrinier headbox is significantly better. The production capacity increase has been what expected, and even higher, and we expect the new headbox to enable even further capacity increases for our future needs”. As a proof of this, their production has increased by 3,000 tonnes which allows Brandia to expand their market share and serve new customers.
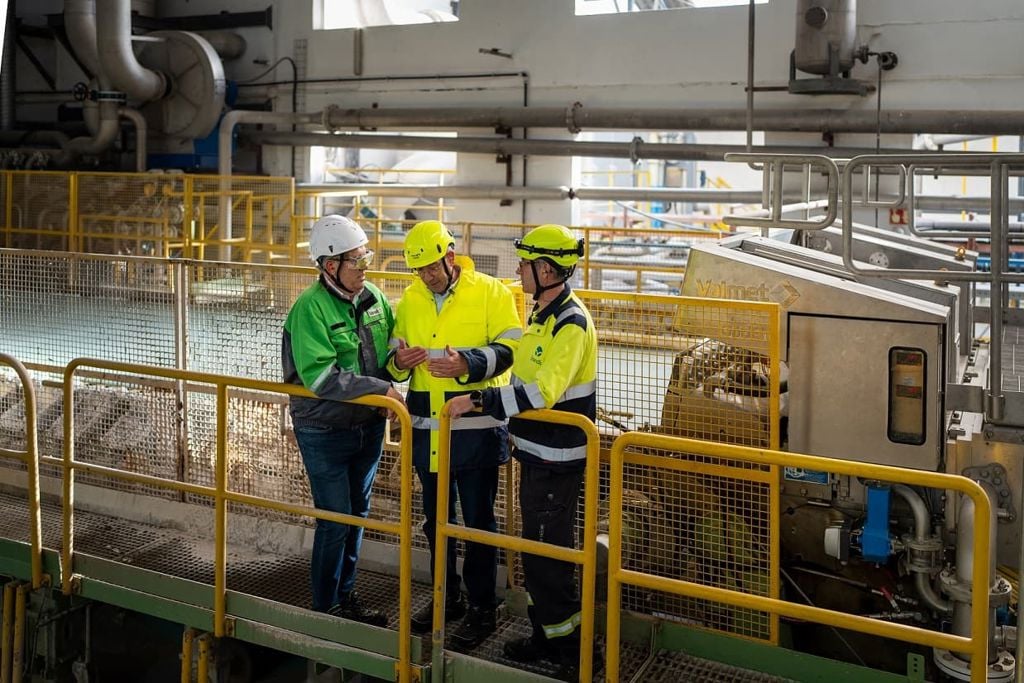
We are being asked very specific requirements and properties by our customers. We can now play with the properties where we had limitations before or could not even produce. This gives us flexibility for the production and much more possibilities to meet the customer requirements.”
Exceptional quality to meet the most demanding customer requirements
One of the key targets for the headbox investment was to improve the quality of our products and achieve a stable level of quality, says Vazquez. “With our old headbox we had very limited tools to work on the quality properties, but now with the new headbox we have tremendously much more tools to optimize and improve both our production and quality,” Vazquez states.
He explains that majority of the most important quality properties their customers ask from Brandia, are now possible to produce and possible to produce with the level of quality their customers are asking for. Vazquez continues listing that: “with the new headbox Brandia have managed to improve formation, porosity, smoothness, and brightness. And, furthermore, we now have the tools for optimizing these properties for each customer requirement and order.”
“We are being asked very specific requirements and properties by our customers. We can now play with the properties where we had limitations before or could not even produce. This gives us flexibility for the production and much more possibilities to meet the customer requirements”, Vazquez states.
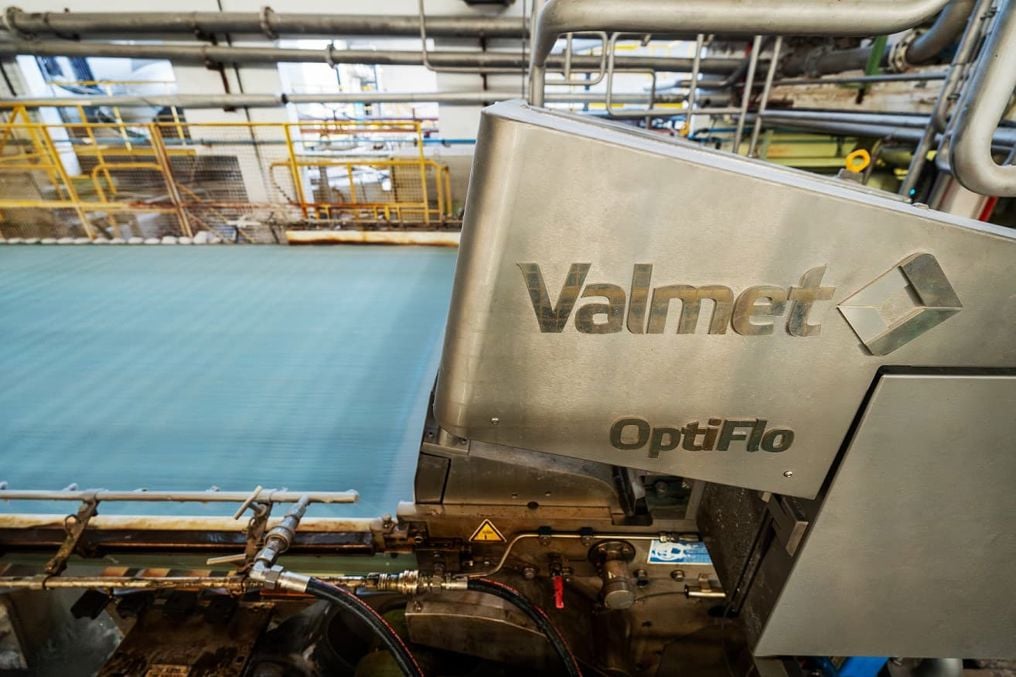
A true testament of the excellent and stable quality is the very low amount of customer complaints. Barreras Rodriguez proudly states that the claims originating to headbox have practically disappeared after the installation of the new headbox. He continues saying that in the past two months the claims related to paper quality and technical properties were worth of EUR 140, which is remarkably low.
Easy maintenance
When asked about the maintenance of the new OptiFlo Foudrinier headbox, Juan Manuel Iglesias Perez, Head of maintenance, Brandia says that: “there have been no issues or problems with the headbox, and no unexpected or out-of-the-ordinary maintenance work has been needed. Normal maintenance and cleaning have been easy.”
When it comes to changing the lamellas, Iglesias mentions that Brandia were recommended by Valmet to use carbon fiber lamellas instead of polycarbonate lamellas. The advantage with the carbon fiber lamellas is that they have a very long lifetime from 3 to 5 years, and this has been the experience of Brandia as well. Since the start-up in August 2022, that is 2.5 years ago, the lamellas have been working flawlessly.

The benefits Brandia currently gets from the new headbox, and our upgraded PM 1, are superior to what we expected.”
Trust and technological performance key factors in supplier selection
For Brandia it was vitally important that the technology partner they select can adapt to their specific needs as a much smaller company as they are. In practice this meant three things: transparent communication, trust between the partners and ability from the technology to efficiently adjust to their small batch production, Barreras explains.
“We manufacture a very wide basis weight range products for various food packaging applications. The production batches are very small and there are up to seven grade changes a day. The technology needed to enable this type of small batch production efficiently to ensure high productivity. And looking back this is exactly what Valmet did with us”, Barreras states.
Vazquez proceeds saying that they had an idea of the development and improvement they needed. The right solution was found when both parties contributed ideas and knowledge to reach a solution that would allow Brandia to meet their targets for the investment. Vazquez continues explaining that: “Brandia has a long, fruitful history with Valmet and the relationship has always been very good. And this partnership and trust, especially with the local Valmet personnel, was one of the factors that encouraged us to go forward in this project with Valmet.”
Brandia can now serve their customers better than before. Pairing improved customer satisfaction with production capacity increase, both Vazquez and Barreras agree that the project targets have been fully fulfilled and even exceeded. “The benefits Brandia currently gets from the new headbox, and their upgraded PM 1, are superior to what we expected”, Barreras concludes.

Text: Elsa Sinjaga
Related content