Supreme quality with unbeatable absorbency and softness
Advantage ThruAir Technology
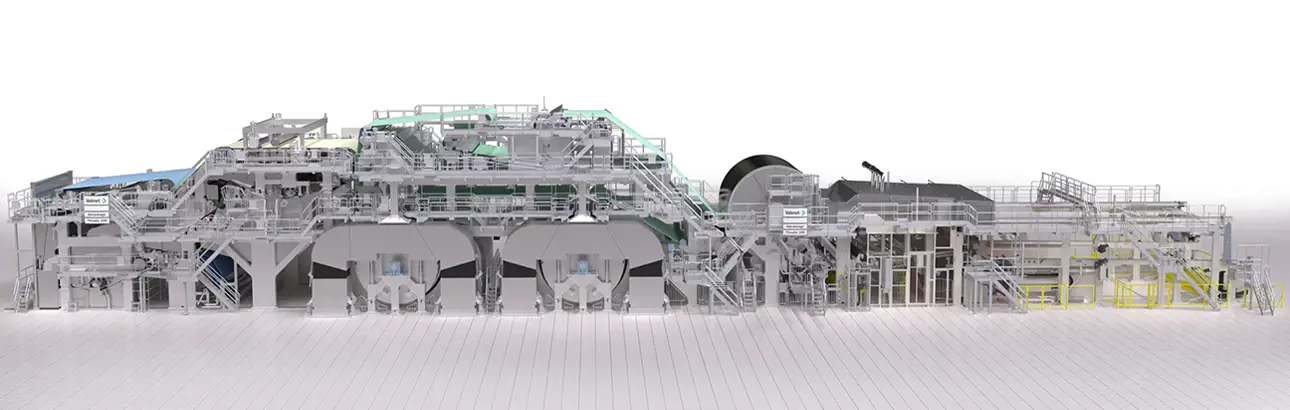
Advantage™ ThruAir® (TAD) Technology for structured tissue delivers the highest rate of absorbency with the lowest basis weight of any comparable tissue product on the market today. It is particularly suited for production of superior quality bath, towel and napkin grades from virgin or recycled pulp.
QUALITY
Highest absorbency to bulk ratio
Highest softness to bulk ratio
EFFICIENCY
High machine efficiency
Highest production speed
Sustainable approach
FLEXIBILITY
Flexible for all kinds of ultra premium products of facial, bathroom tissue, towel.
Wide range of sheet basis weight and furnish strategies
Suited for production of superior quality tissue
TAD products have become the preferred choice for consumers around the world. Softness, strength, bulk and absorption are all highly valued products features. The Advantage Thru-Air (TAD) Technology provides these desired quality properties and can cater for all production volumes. The base principle of the TAD technology resides in vacuum dewatering of the sheet, molding of the sheet into a structured TAD fabric and drying the sheet by forced air.
The key to high bulk
The tri-dimensional fabric design and rush transfer capability associated with TAD manufacturing allow the tissue producers to dial-in sheet properties such as absorbency, bulk and softness. The TAD process avoids the destructive effect of wet pressing as opposed of other tissue manufacturing processes. This is key for a high bulk fully structured sheet.
The engineered sheet
In addition to all the normal conventional machine tools, the Advantage Thru-Air machines also offer the opportunities for rush transfer, molding, and a variety of TAD fabric styles. These all help to engineer a distinctive product with high consumer appeal.
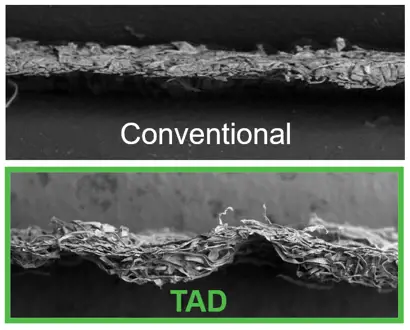
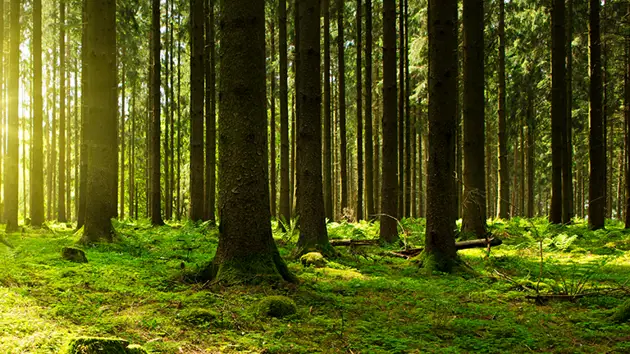
Reduce fiber usage up to 40%
Valmet continuously seeks for improving performance and efficiency of its Advantage Thru-Air technology with respect to fiber usage, fiber recovery, energy recovery and for reducing the emissions. The flexible design of the TAD air systems allows the manufacturer to adapt the technology based on energy cost, source of energy available or to minimize carbon emissions of the process.
The TAD technology can reduce fiber usage in the final product by up to 40% in comparison with a conventional tissue sheet depending on grade produced, fabric design and strategy of operation.
In comparison with conventional machines, Valmet TAD machines are known for the ability to deliver products with superior sheet properties and improved fiber utilization rates. This translates into higher value products with lower fiber costs per case. The numbers below are expected after converting operation.
Fiber reduction (TAD vs DCT paper)
~35%
Towel product
~41%
Bath product
3.5x higher
Caliper
The Advantage ThruAir family
The Advantage ThruAir 100 and 135 are entry level machines that are best suited for the small or medium sized producer or those exploring emerging markets.
For large scale producers in mature markets the Advantage ThruAir 200 can provide the very high output required. The concept is at the same time flexible and machines of varying width and output can be customized to suit producers’ special needs.
All members of the ThruAir family can produce top quality ultra-premium products. Further, energy consumption is as low as 3800 kWh/MT (depending of furnish/grade and operating conditions). This includes thermal (gas steam) and electrical.
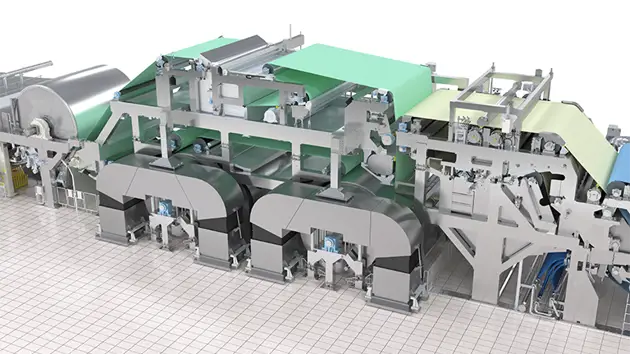
Advantage ThruAir 100 | Advantage ThruAir 135 | Advantage ThruAir 200 | |
Thru-Air dryer | 1 x 16 ft TAD | 1 x 16 ft TAD | 2 x 16 ft TADs |
Yankee | 18 ft | 18 ft | 18 ft |
Basis weight range | 15-45 gsm | 15-45 gsm | 15-45 gsm |
Max reel speed | 1600 m/min | 1600 m/min | 1600 m/min |
Max sheet trim | 2.8 m | 3.6 m | 5.6 m |
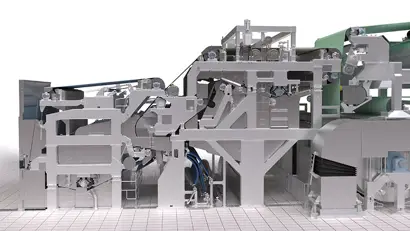
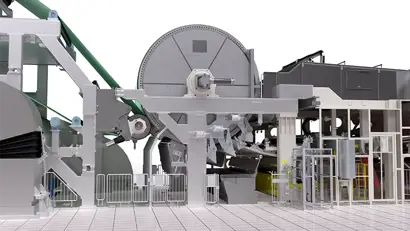
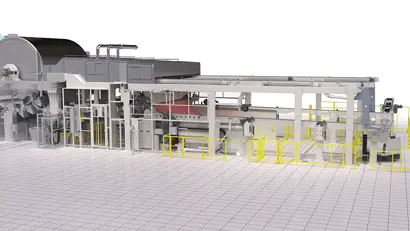

With close to 60 TAD machines, rebuilds and air systems installed worldwide, we are uniquely qualified to bring this innovative technology to you at the lowest possible overall cost.

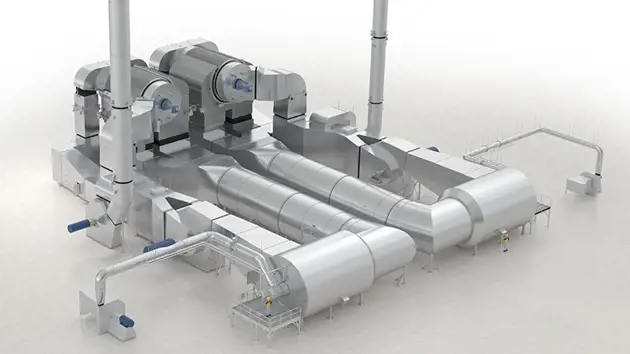
Reduce your emissions
Valmet TAD air system can be configured to maximize energy recovery. It can be adapted to use a combined heat and power unit or used in conjunction with steam coils. We utilize the best in class burner technology, specially developed in partnership with a burner supplier, to reduce your emissions by 95% compared to the traditional technology.
The importance of the Honeycomb roll
With more than 110 tissue TAD Honeycomb rolls delivered in the tissue industry, our unit located in Bidderford, USA has established itself as the leader in this field and developed a deep understanding of the technology. Key factors such as airflow uniformity, sealing and structure strength are very important for good operation of the TAD process.
Reliability and longevity are non-neglectable aspects when it comes to designing a TAD roll. The Valmet Honeycomb design has multiple references that have been in operation for more than 40 years which confirms its strong design.
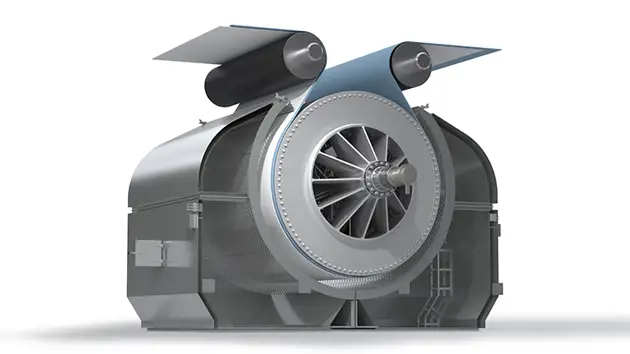
A dialogue with data to improve the performance
Valmet Industrial Internet offering covers an extensive range of solutions and applications for tissue mills in order to optimize the full scope of the production. The data driven applications and services support you throughout all the phases of the tissue machine’s lifecycle.
As a start we normally explore the potential of utilizing data through a data discovery process. Then we can evaluate what applications within production capacity, quality, energy efficiency and reliability, are beneficial for your operation. Further, our expertise is easily available for you through the Valmet Performance Centers (VPC). Our specialists have a deep understanding of machinery, processes and automation and with connections and tools, we can offer the needed remote support and guidance without delay from our 8 centers around the worlds.
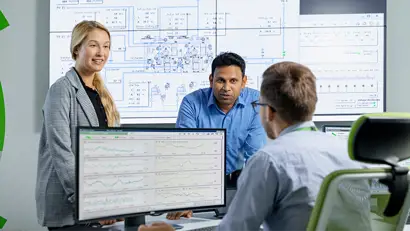
Explore our VII guidebooks
What is the Industrial Internet? What do you need to know about it? And how can you make it work for you? We have prepared guidebooks to open up the most important elements of the Industrial Internet and to explain why and how data can benefit your business.
Get your guideQuestions and answers about the Through Air Drying process technology
Q: What does TAD stand for?
A: TAD is the acronym for Through Air Drying
Q: How does the Through Air Drying (TAD) process differ from conventional tissue manufacturing methods?
A: In the Through Air Drying (TAD) process, hot air is used to dry tissue sheets, resulting in softer and bulkier products compared to conventional methods.
Q: What are the key advantages of using Through Air Drying (TAD) technology in tissue production?
A: The TAD technology is a well-established process providing a wide operating window for ultra-premium tissue and towel production. The web is dewatered by vacuum elements in the wet-end. Since there is no wet-pressing and the paper is air-dried, it results in enhanced softness, bulk, and absorbency in tissue products, leading to improved consumer satisfaction and market competitiveness. The C-Former orientations places the long fiber first against the forming wire (draining first) and provide a support for the short fiber. Additionally, since sheet is significantly dryer going into the Yankee cylinder, the operation at the Yankee is less impacted by fines from the white-water system. These process differences are an advantage for both the operation and the end-product quality.
Q: What types of raw materials are typically used in conventional dry crepe tissue paper production?
A: Softwood or hardwood trees mainly serve as the primary fiber component.
Q: What factors should be considered when selecting or designing a Through Air Drying (TAD) tissue machine for specific production needs?
A: Factors such as production capacity and speed, desired tissue properties, energy efficiency, and cost-effectiveness are considered when selecting or designing a TAD tissue machine.
Q: Are there any challenges or limitations associated with implementing Through Air Drying (TAD) technology in tissue manufacturing, and how can they be addressed?
A: Challenges in TAD technology includes higher energy consumption and equipment costs compared to conventional methods. However, advancements in technology and process optimization can mitigate these challenges. Production output and efficiency of the tissue line, fiber saving, and high retail value of the paper are making the process interesting from a sustainable perspective. Additionally, the process can be integrated with cogeneration, electrical and steam coils heating systems elevating the process to a more sustainable tissue production with potential of a complete fossil-fuel free operation.