Casmatic Sam solutions for packaging equipment
Casmatic Sam pack
Industry 4.0 ready
- Stores locally and shares quality data via a dedicated gateway
Effectively prevents quality issues
- Accurate and reliable packaging moniotring
- Detects most of the visible defects
- Works with any packaging format
Easy to use
- Easy to operate and to visualize defects via the HMI pannel
- Fast to set up and to add new defects to detect
No more uncertainties
Thanks the highly accurate and reliable technology this system is the ideal solution to effectively monitor packaging quality avoiding human herrors and minimizing the risk to deliver uncompliant products.
Featuring the latest technology
Casmatic Sam pack includes a set of HD cameras and light bars which scan each pack side; a deep learning algorithm is then able to detect most of the visible defect for any pack format, and the uncompliant packs can be ejected.
A great help for operators and quality managers
Casmatic Sam pack is easy to operate and fast to set up, giving also the possibility to store both locally and remotely quality data for analytics purposes.
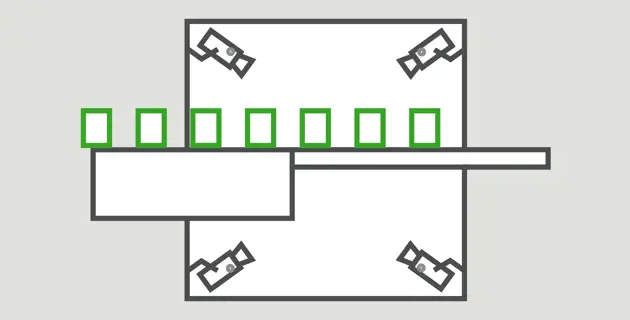
Casmatic Sam cut
Improved OEE
Avoids downtimes caused by perforation issues
Improved operator safety
Perforation monitoring and correction can be done easlily and safely from the HMI, without accessing the wrapper
High reliability and accuracy
The patented technology ensures precise and reliable measurements, without being affected by temperature, dust and vibrations.
No more jams and downtimes
Casmatic Sam cut has been designed to monitor packaging film perforation quality in wrapper machines, by continuously checking the interference between the perforation blades. Casmatic Sam cut allows to detect in advance the incorrect perforation, preventing possible jams and downtimes.
A patented system
The employed technology is highly robust and reliable: 24 V DC is applied to the fixed blade and the rotating one is grounded. Since the helic rotating blade touches the fixed one in a small section only, the PLC receives a high signal each time the interference does not occurr, and it is possible to locate the section on the blade.
A great help for the operators
This system, together with the motorized blade adjustment, allows to monitor and correct the perforation rapidly and safely without accessing the wrapper, thus improving the line OEE and the operator safety.
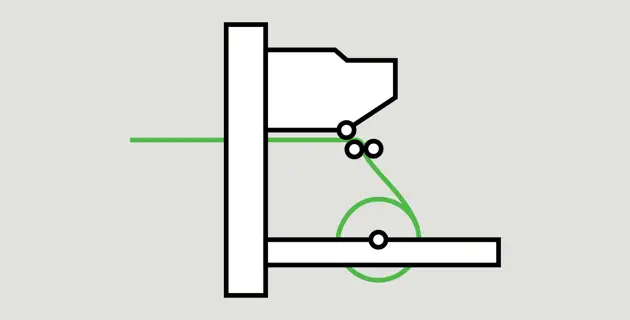