Field services for pulp drying equipment
A range of comprehensive support and maintenance services to ensure optimal pulp dryer performance
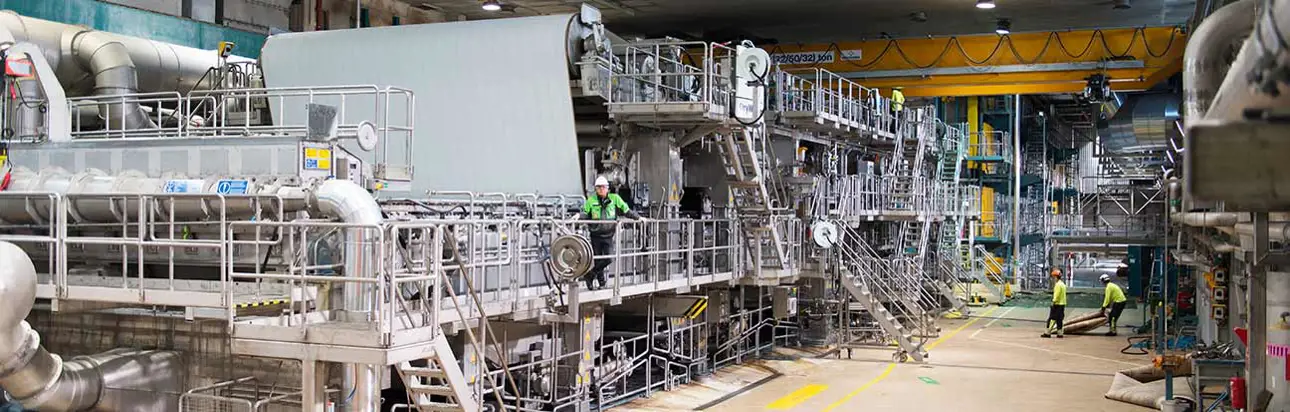
Different problems need different solutions. By supplying expert maintenance services and comprehensive support tailored for each customer, we ensures efficient pulp drying operation with minimal downtime, improved performance, and increased output. We can support the needs through different services such as field service site support, remote support via our Valmet Performance Centers and onsite troubleshooting and audits. Our long experience and knowledge as a pulp dryer machine supplier provides a special know-how to ensure customer trouble free operation not only to our machines but also the complete process from wet end, drying section, cutter layboy and system function including headbox, wire section, press section, dryer and cutter.
Improved runnability
Optimized vacuum
Improved air balance
Speed control
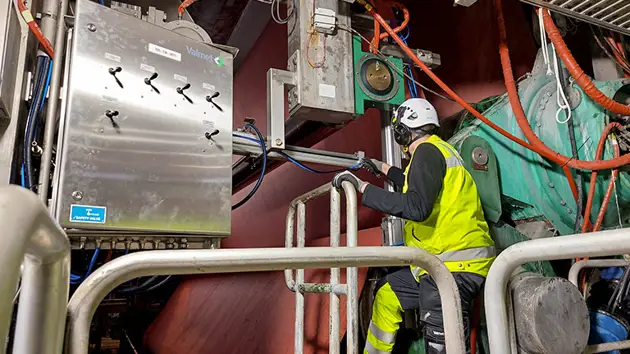
Reduce machine downtime with tail threading services
An efficient tail threading process reduces machine downtime and boosts the overall efficiency of a pulp drying line. Valmet tail threading service improves the tail threading process and ensures equipment availability and reliability
- Improves tail threading process
- Savings in maintenance costs
- Ensures equipment availability and reliability
- Reduces tail threading times
Find out more about our tail threading services.
Long-lasting and effective dirt repellent at the wet end with headbox coating
Valmet’s headbox MX06 coating method reduces dirt-related problems on the wet end of pulp, paper and board machines. It leaves a very thin and unnoticeable protective coat that is nevertheless a very long-lasting and effective dirt repellent.
What can you achieve with Valmet's Headbox MX06 coating?
- Keeps headbox flow surfaces cleaner
- Reduces required washing time
- Reduces the need to use strong chemicals during washing
Find out more about Headbox MX06 coating.
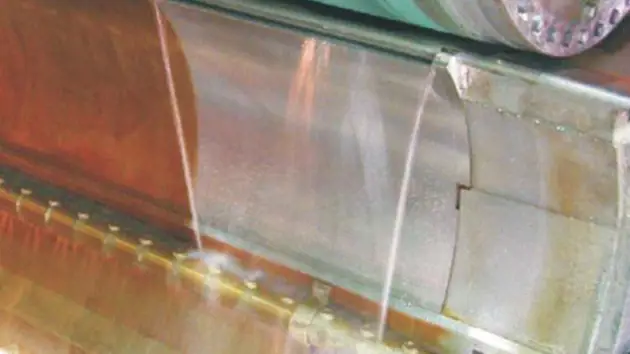
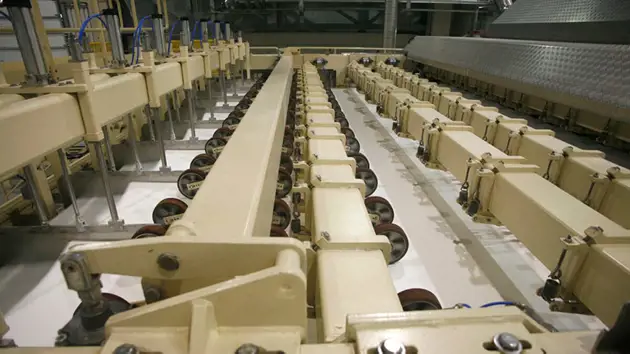
Evaluate current technical cutter condition
The condition test will tell the current technical condition. The machine runnability and the process functions are also evaluated.
- Process function study and process optimization
- Mechanical check-ups and measurements
- Hydraulic and pneumatic system inspections and water circulation study
- Automation field device inspections
- Repairs and adjustments within machine shut down timeframe
- Written reports
Read more about Valmet's cutter condition test.
Questions about equipment maintenance or support for equipment or process performance development?
Whether it’s a single process survey, equipment maintenance, shutdown management or full maintenance, don’t hesitate to contact your closest Valmet Service Center for guidance.
Contact us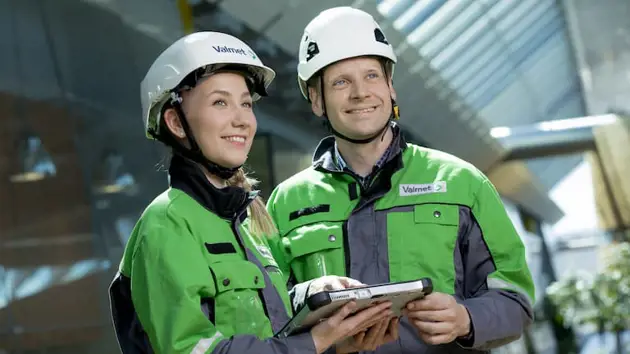
Cleaning services for consistent energy efficiency and good runnability
Regular cleaningof pulp dryers is the key to consistent energy efficiency and good runnability in the pulp dryer. Benefits of cleaning services are diverse:
- Capacity increase
- Better runnability
- Reduced dust formation and amount of web breaks
- Energy saving
- Shorter down time
Learn more about the advantages of cleaning service for pulp dryer.
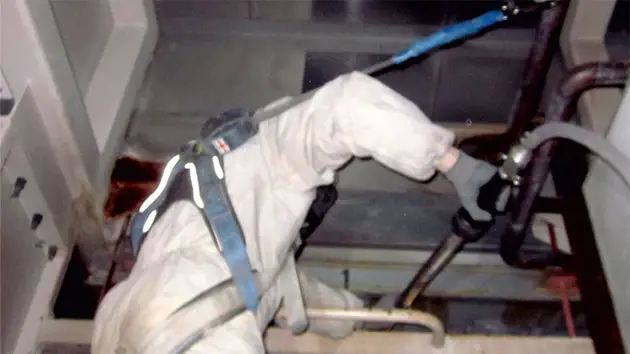
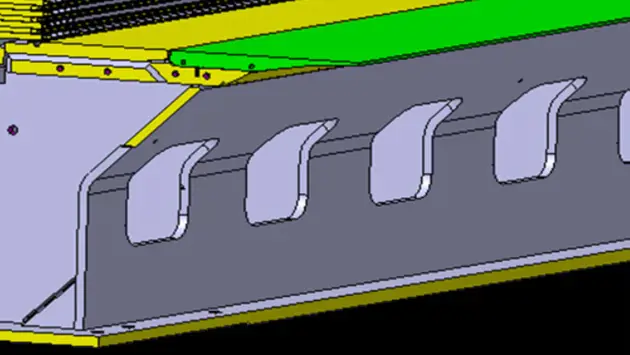
Better dry weight profiles with apron plate replacement
A solution for better dry weight profiles. The apron is one of the most delicate parts of pulp and paper machines, and it has a remarkable effect on the cross-direction profile. The alignment and flatness of this part is critical for the process.
- Reduces need for slice control
- Reduces CD basis weight variation
- Improves machine runnability
- Improves dry weight profile
- Improves jet flow stability
Learn more about apron plate replacement.
Articles and references
keyboard_arrow_leftBack
{{currentHeading}}
{{productForm.Name}} {{"("+productForm.Size+")"}}