LignoBoost® - the process
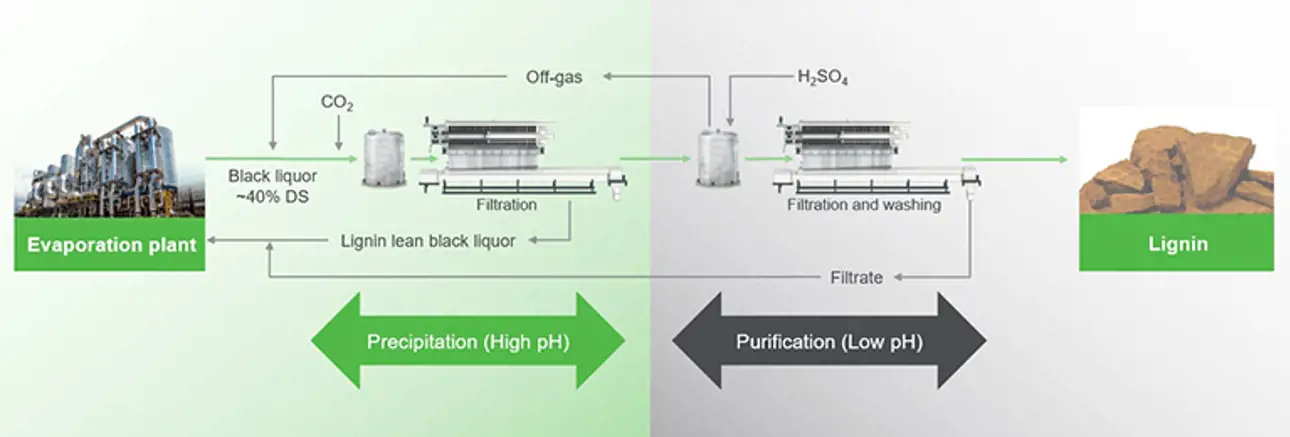
LignoBoost® is a patented process for producing lignin from pulp mill black liquor. Thanks to the continued development, the produced lignin can be given properties that match the intended use.
High-quality lignin from a unique two-step process
LignoBoost is a lignin production process divided into two steps: a separation step, followed by a washing step. The two steps makes it possible to optimize the conditions in each step and produce a very high quality lignin. It also provides several options for adjusting the characteristics of the lignin. LignoBoost was initially developed by universities and research institutes, but has been commercialized and further developed by Valmet.
Step 1: Separation
The first step is to separate the lignin from the mill’s black liquor. Black liquor is taken from evaporation, and the pH is lowered with CO2 and gas collected from the second step of the LignoBoost process. When the pH drops, lignin precipitates and is separated from the liquor with a press filter. The output of the first step is LignoBoost crude lignin.
Step 2: Washing
In the second step, the lignin is purified. The crude lignin is washed in a low pH solution and then dewatered in a second filter press. The purity of the lignin is highly dependent on the conditions in the washing step. LignoBoost is engineered to produce a very pure lignin.
Filter presses are key
The filter presses have a major influence on the quality of the extracted lignin. The current design of the filters and their operation is a result of Valmet’s substantial experience with lignin production. The filters are engineered and fully integrated with the process’s two steps. This results in high safety and reliability.
Return flow to the mill
Lignin lean black liquor and wash water are returned to the evaporation plant. The flow of wash water is low and can normally be handled with only minor changes to the mill’s operation.
Pulp mill sulfur balance
LignoBoost uses sulfuric acid to purify the lignin. Most of the sulfur in the acid is returned to the mill with the wash water and gas from the lignin extraction process.
Valmet’s sulfuric acid plant offers a good way to control the pulp mill’s sulfur balance. Valmet has built one sulfuric acid plant and has recently been awarded the contract for a second. To learn more about Valmet’s sulfuric acid plant technology, see here.
High operational safety
Valmet’s LignoBoost technology ensures reliable and safe handling of all process flows, like black liquor, return liquor, wash water and gas from the process. When the pH of black liquor is reduced, H2S is released, and this makes the gas handling systems an important part of a lignin production plant. Valmet’s in-depth knowledge of the process reactions has resulted in several advanced gas handling solutions that are integrated with LignoBoost and surrounding mill. LignoBoost is built for high safety.
Safe gas handling
The gas produced in the second step of the LignoBoost process is collected and used to reduce the pH of the incoming black liquor. This solution reduces the consumption of carbon dioxide and with it, the operating cost.
Excess gas from the process falls into the DNCG category of gases in a chemical pulp mill. This gas is collected and sent to the mill for destruction. Valmet has many solutions for safe gas handling in pulp mills.
Complete production lines
Valmet supplies complete systems for lignin production, all the way from lignin separation to packing, including all processes needeed to manage the sulfur balance in the mill.
Lignin as fuel in the lime kiln
Lignin is also an excellent fuel for the lime kiln. Valmet can supply modifications to the lime kiln burner and surrounding systems.
How much lignin can be removed from the black liquor?
Many pulp mills can separate up to around 25 percent of the lignin from the black liquor without modifying the existing mill equipment. The Stora Enso Sunila mill was designed to produce 50,000 metric tonnes of lignin per year, or 22 percent of the lignin in the black liquor. Lignin lean black liquor and wash water can be evaporated like a normal black liquor, and if the pulp production is increased and the mill’s energy consumption is reduced, up to 70 percent of the lignin can be removed.
More on LignoBoost
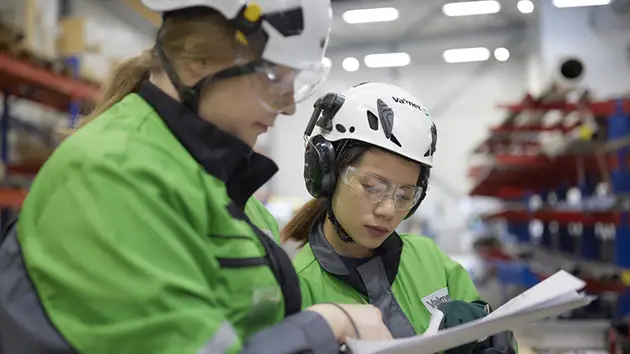
Contact us
To discover how we can help you bring your lignin business forward, get in touch with us through the “contact us” pages or your local Valmet office. Our focus is to bring our customers' performance forward.
Contact us