Flow control for gold
From gold autoclave pressure oxidation to gold production in CIL, CIP or CIC circuits
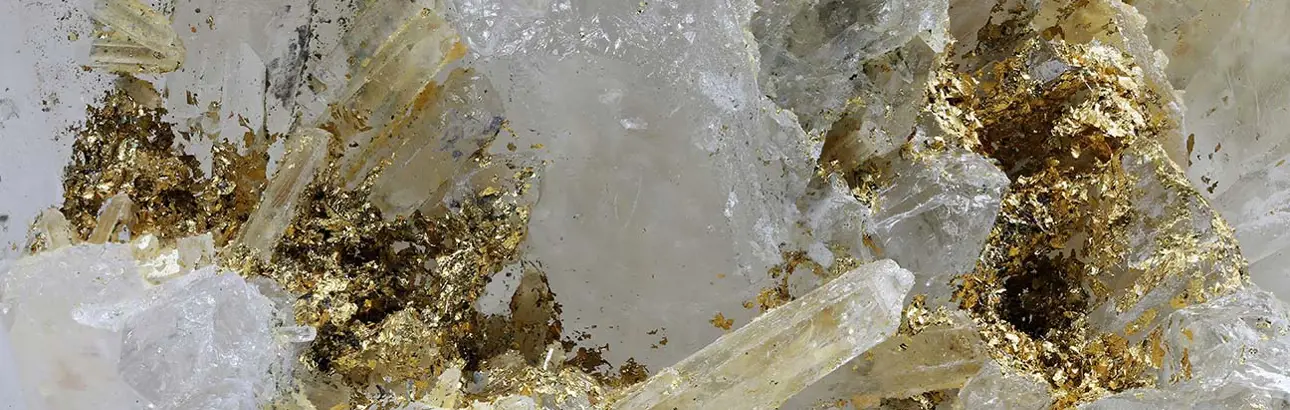
The nature and chemistry of an ore deposit determine the processing method used in gold production. There are many processing techniques for gold ore. The most common is cyanidation in carbon-in-leach (CIL), carbon-in-pulp (CIP) or carbon-in-column (CIC) circuits. Valmet has a wide range of valves and pumps ideal for CIL, CIP, and CIC processing. Another method is autoclave pressure oxidation (POX), which is an effective pre-treatment option when extracting gold from refractory ore bodies, such as pyrite and arsenopyrite. We also offer a wide range of valves, pumps and services for POX process.
Improved safety and reliability
Higher recovery rates and lower total cost of ownership
400+ service professionals in over 40 countries around the world
Optimal valve and pump selection can provide substantial savings in gold production in CIL, CIP or CIC circuits
Gold leaching plants use valves and pumps for numerous flow control and isolation services. Valve and pump performance affects the whole leaching process, so it is vital to select the right type of valve or pump for the right application.
Requirements for tightness, abrasion and erosion resistance, and pressure range, are among the key variables when choosing the optimal valves or pumps. Reliability should also be considered, since malfunctions may lead to safety risks and added process downtime.
Valves for thickening
Thickeners increase the content of solids and thus the gold concentration of the slurry. Unwanted gangue is separated in the thickener and processed in the tailings stream. Process water, on the other hand, is recycled back for upstream processing.
Valve installations in thickeners are required for overflow as well as underflow service. On the overflow side, butterfly valves provide effective flow control. Knife gate valves are also used. For the thickener underflow, pinch and knife gate valves are the most common solutions.
Valves for pressure oxidation
If the gold ore is refractory by nature, it may require pre-treatment processing before leaching.
One pre-treatment option is pressure oxidation (POX). Due to the conditions that valves are subjected to in the POX process, the highest possible resistance against corrosion, erosion, and deterioration caused by solids is required.
To maintain the sealing abilities of slurry feed valves, the right material, seat and coating choices play an important role. Valmet offers the most competitive valve solutions for the POX process.
Valves for leaching tanks
Regardless of the leaching method (CIL, CIP or CIC), valves must provide reliable control for the liquid, gaseous and air flows.
The presence of cyanide creates challenges for process control and makes the correct valve material selection essential. When performance requirements are a high priority, process ball valves are a good option for the leaching tanks.
With the right material, coating and seat selection, ball valves provide a long service life and precise flow control capabilities.
Gold leaching process in CIL, CIP or CIC circuits
The gold leaching process starts with comminution. Run-of-mine ore is first crushed and ground to a fine particle size. Water is then added to the process to create a mud-like slurry that is pumped into a thickener where gold-bearing particles sink to the bottom and are passed to downstream processing.
Typically, the next processing phase is a CIL, CIP or CIC circuit. All these methods use cyanide and activated carbon to extract the gold from the slurry. The applied technology varies from one plant to another, but CIL is the most commonly used method.
In the CIL circuit, cyanide and oxygen are added to the slurry, resulting in gold being dissolved from the ore. Activated carbon is then fed into the process from the opposite direction, against the slurry stream, and as it moves through the CIL tanks, dissolved gold adsorbs onto the activated carbon. This loaded carbon then continues into an elution column, where the adsorption process is reversed.
Gold is stripped off the carbon into a pregnant electrolyte and fed into electrowinning cells for plating onto stainless steel wool cathodes. A water spray then removes the gold sludge from the loaded cathodes for filtering and drying. After dewatering, the gold sludge is mixed with fluxes and heated in a furnace to produce doré bars that are transported to a gold refinery for processing into 99.9% pure gold.
Valves and pumps control various flows in gold autoclave pressure oxidation process
Autoclave POX operations include several different types of valves to control both liquid and gaseous flows. Slurry feed and discharge valves, pump isolation valves, depressurization valves, steam supply and steam drum isolation valves, as well as oxygen feed valves, among others, make sure that the POX process works optimally and efficiently.
In the autoclave, valves are subjected to a high-temperature and an oxygen-rich environment, so the right selection of valves can potentially make a significant positive impact on the operation’s reliability.
Valves and pumps for slurry feed
The conditions that valves and pumps face in the POX process require the highest possible resistance against corrosion and erosion as well as against the deterioration caused by solids. The right material, seat and coating choices play an important role in maintaining the sealing abilities of slurry feed valves and pumps.
Valves for oxygen feed
Valves for depressurization
Autoclave POX for the extraction of refractory gold
In the POX process, the ore is crushed and mixed with water to create aqueous slurry that is then heated and fed into an autoclave.
Oxygen is added to the vessel to react with the slurry. The POX process uses high temperatures (approximately 200 °C/400 °F) and high pressures (10-35 bar/150-500 psi) to facilitate the leaching process.
After the autoclave processing step, the slurry is returned to atmospheric condition by taking it through two or more flashing letdown stages.
Once at atmospheric condition, the slurry is washed and separated, at which point the metal can be recovered from the liquid portion in the downstream processing circuits.
Downloads
Valves, pumps, valve automation and services for gold production
Flow control for different applications in mining and minerals processing