Flow control for gas to liquids (GTL)
Improving reliability and productivity of your process
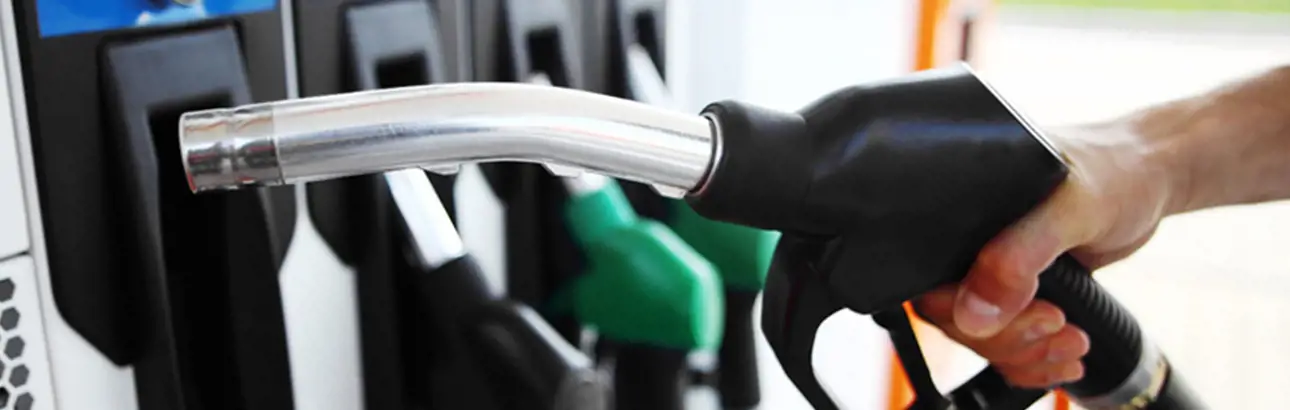
GTL is proving to be a technology advance with great potential for the hydrocarbon industry. Though the process is not entirely new, it is challenging for plant engineering to scale the plant appropriately. Valmet has developed best-in-class valves and flow control services to overcome the challenges of the GTL process from syngas production and air separation through the FT reaction, regardless of the reactor type (fixed, fluidized or slurry bubble).
Process reliability
Reduced VOC emissions
Extended uptime and profitability
Reliable valves for gas to liquids (GTL) process
Handling slurries and waxes
Investing in GTL and processing the plants involves great risks. It’s one that can have great rewards. High temperature, noise, cavitation, and pressure differentials along with the challenges of waxy and slurry media make GTL applications challenging. The difference is overcoming these challenges to boost uptime and keep the process running for extended periods between shutdowns.
This calls for careful selection of valve type, seat and materials. There needs to be reasonable amount of valve types to meet the variety of all requirements, which again sets challenges to find manufacturers that can provide products with long lasting performance.
Valves at the heart of the GTL process
Valmet has developed best-in-class products specifically designed to overcome the challenges of the GTL process from syngas production and air separation through the FT reaction, regardless of the reactor type (fixed, fluidized or slurry bubble).
Our experienced engineers have GTL field and application experience that translates to customer success. We work with customers to select the best mix of products from our comprehensive line of solutions. Special considerations are given to all the relevant details, from valve sizing and selection to seat design and the materials of construction, all of which ensure the valve will not clog and maintain tight seals for long periods. Trim designs are critical to maintaining safe and profitable GTL processing. Our noise reduction technology has been proven to prevent cavitation and reduce noise and vibration considerably.
Process reliability
Valmet's people and superior product offering help GTL plants to extend periods of uninterrupted uptime while boosting efficiency and ensuring safety. Dedication to technology development at ever demanding process requirements will benefit further the GTL industry to meet the toughest requirements and ensure safe plant operations.
Flow control solutions and services for gas-to-liquids
Read more about our solutions for gas processing