Preheater
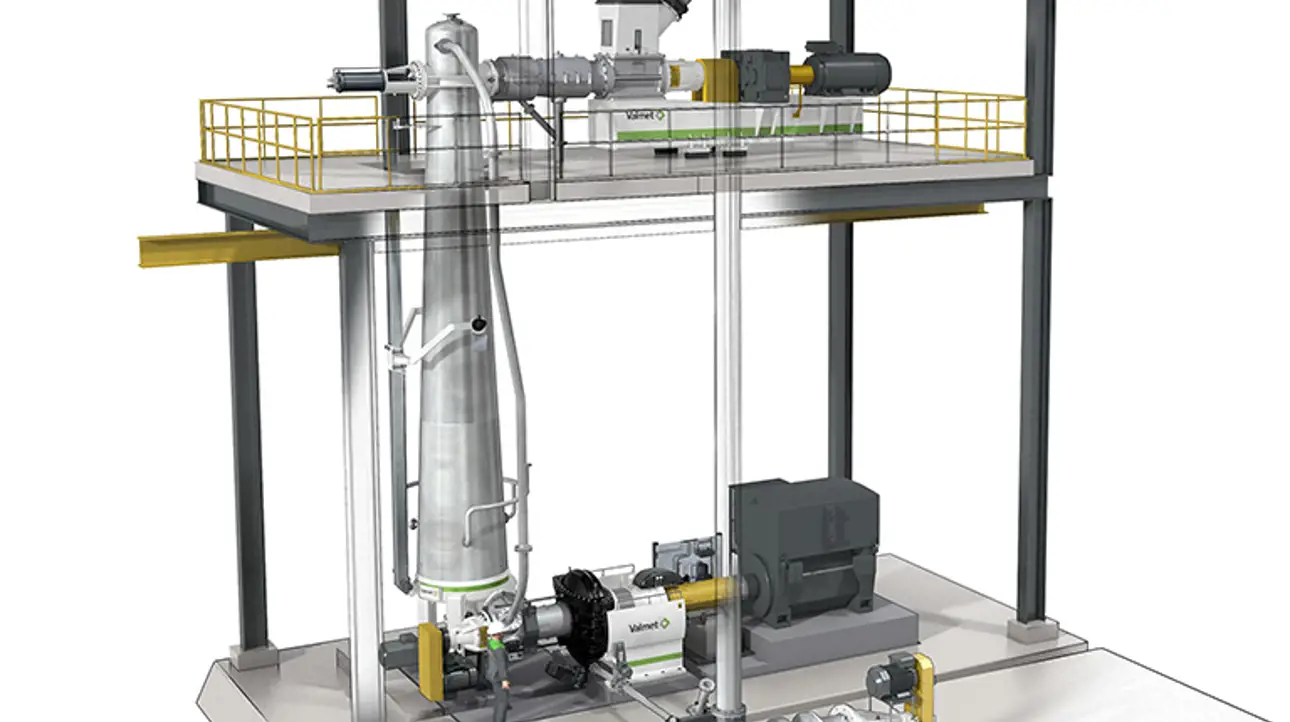
The preheater heats the raw material in an pressurized atmosphere of steam. This softens the raw material and enables easier separation into fibers and fiber bundles in the following refining process (Defibration). The temperature in the preheater is maintained at a preset, variable level. By varying the level in the preheater in relation to the feed rate, a controlled preheating time can be maintained.
The preheater is of a conical shape with bigger diameter in bottom to avoid bridging. Steam is entered at the preheater top and above the bottom section to provide thorough heating of the raw material. In the bottom part of the preheater mantle there is a flanged man-hole. The preheater bottom section has a so-called agitator, driven from a vertical shaft through the preheater bottom, which scrapes the raw material into the discharge screw.
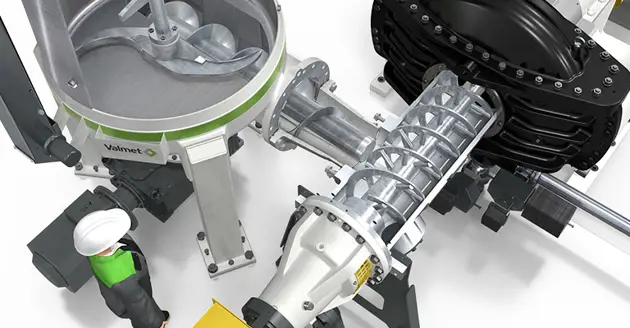
Preheater discharge screw with compression zone
Even discharge from the preheater discharge screw is crucial for smooth refiner operation at low energy. For that purpose Valmet preheater is equipped with an discharge screw (outfeed screw) with a compression zone. This compression zone is an important detail that distinguishes Valmet's design from other solutions on the market. This compression zone creates a pressure tight plug between the preheater and the Defibrator (refiner) and enables smooth and even feed to the refiner without any disturbances from steam flow. The even discharge from preheater together with the EVO centrifugal refiner housing in the Defibrator results that Valmet refiners consume less energy for the same fiber quality than the competitors. The compression zone in the preheater also enables to operate the refiner with a wider range of differential pressure in the Defibrator.
Heavy duty machinery for tough conditions
Valmet equipment often stand out due to its durability and reliability. Valmet Preheater is normally made from thick, cast, stainless steel. Mechanical components like bearings, gears, couplings have high drive factor to ensure a long life time. Compared to our competitors Valmet Preheater has up to three times longer liftime
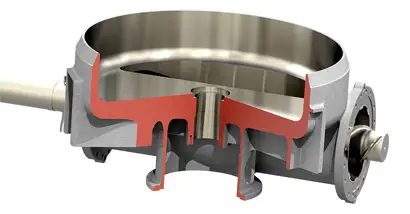
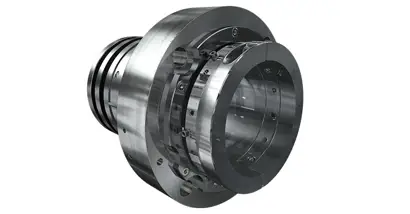
Enviromental friendly by saving water
To minimize environmental impact Valmet has developed a closed loop mechanical sealing system and a new double cartridge mechanical seal type BA. This minimizes the water that enters the process and thus will reduce the steam consumption in preheater and the energy needed in the drier.
Preheater rebuild for improved operation
Many fiberboard producers have reached maximum preheater capacity. Many of them also produce with marginally good woodraw material. This often leads to feeding problems at various positions on the production line. In order to ensure the best possible preheater performance while providing a uniform load on the Defibrator/Refiner, Valmet has developed Valmet Preheater Upgrade, with a wide range of products for upgrading preheater performance.

Upgraded preheater can result in following benefits
- Higher capacity
- Uniform and high consistency
- Constant flow
- Reduced bridging of chips
- More uniform filling of the discharge screw
- More uniform load on the Defibrator/Refiner
- Better gap control
- Better loadability
- More uniform fiber quality
- Increased segment life due to better control.
Material available for download |
||
---|---|---|
Valmet Preheater Upgrade |
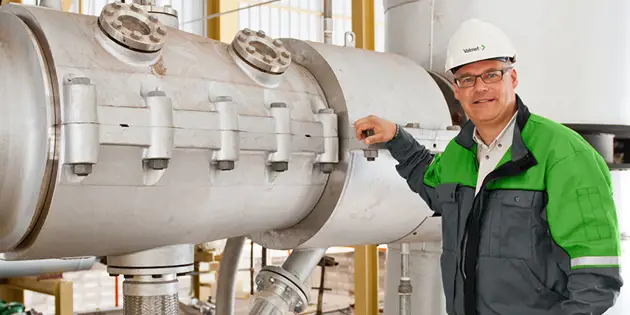
Our expertise is at your service
Our focus is to bring your performance forward utilizing our extensive experience and in-depth knowledge of pulp process technology. Get in touch with our experts through your local Valmet office, or the link below.
Contact us