Flow control for polyolefins and polymers
Improving reliability and productivity of your process
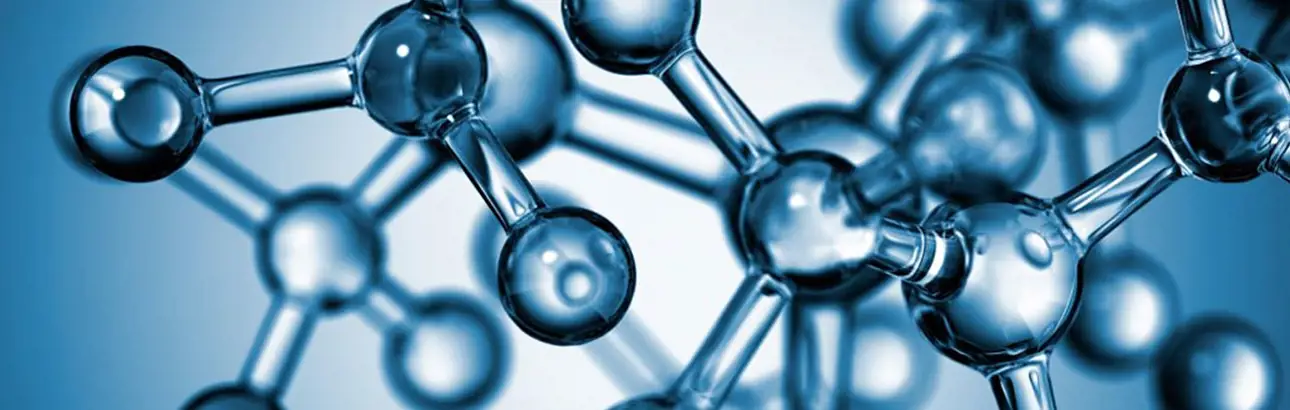
Polyolefin technologies include gas-phase, slurry, high-pressure, mixed-phase, and solution processes. Our valves have been developed to operate in extreme conditions, dealing with an abrasive flow media at very demanding cycling requirements.
Product discharge systems
Unreacted gas is separated from the product and returned to the reactor via product discharge systems. Because they are anti-abrasive, and also prevent polymer from penetrating behind the seat and seizing the valve, metal seated ball valves are the best solution.
Polymer handling valves
Our polymer handling valves are designed to cope with the erosive flow media typical in polyolefin processes, preventing it from entering the seat area, and helping remove any particle build-up.
High cycling valves
In polyolefin processes, valves must be able to withstand up to 1.5 million cycles annually. We offer solutions providing excellent flow characteristics and high capacity, while also maintaining internal tightness.
Reliable valves and services for polyolefins and polymers processing
Valves used in certain types of polymerization processes, such are fluidized bed gas reactors, are typically cycled from 200,000 to 400,000 times annually, often at fairly quick rate of 2-3 seconds. With high cycle rate and speeds comes considerable stress and demand on both the valve and actuator.
Overcoming high cycle rate and polymer residue
Despite the high cycle rate and process stresses, it is essential for valves to operate accurately and reliably over long periods. The marketplace demands clean, high quality products. If valves do not function optimally, adverse effects on quality and plant performance will occur resulting in more problems downstream. Simply put, valves that don’t perform well over the long haul will reduce quality and cause shutdowns.
Medium containing resin, unreacted catalyst and possibly even chunks of polymer present yet another source of valve failure. The buildup of these elements, especially behind the ball cavity, will cause the valve to seize. In extreme cases, accumulation of teal catalyst has resulted in valve leakage and dangerous fires when the chemical was exposed to air.
Proven to go the distance
Valmet has specially designed valves and actuators for use in these demanding applications. Proven to overcome the challenges of high-cycle rate, we recommend metal-seated ball valves with polymer-proof seat and high-cycle actuator designs for these demanding applications.
The polymer-proof metal seat will prevent polymers from penetrating behind the seat to mitigate valve seizure. Because the seat has continuous contact with the ball, it wipes away any build-up with every cycle. Lab and field-testing have proven the valve to provide greater process efficiency, reduce downtime and costs associated with maintenance.
Our intelligent on-off valve controller is designed for high cycling and process-critical on-off applications. The high capacity pneumatics featured in Valmet actuators produce fast stroking times without the need for volume boosters or quick exhaust valves, thereby reducing hardware costs the number potential failure points within the system.
Time-tested performance
Our field-proven products provide accuracy and reliability beyond expectations, keeping your process up and running efficiently for longer than you thought possible. Extend the time between scheduled shutdowns – we can help you do that. Need accuracy after 400,000 cycles – we can do that. Improve safety conditions in your process – we can do that too.
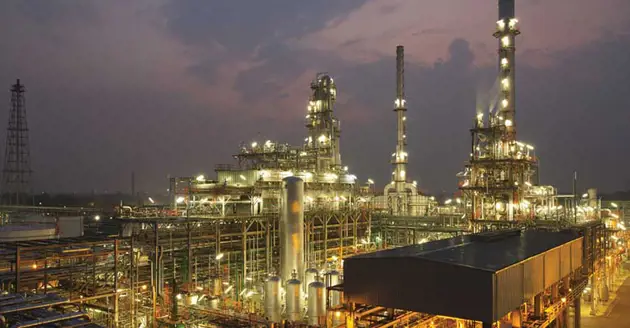
Increase polymerization process efficiency with reliable valves
Petrochemicals have seen tremendous growth in the last decades and many studies suggest that there will be an increasing focus on petrochemicals in the future as well.
See the expert blogDownloads
Flow control solutions and services for polyolefins and polymers
Read more about our solutions for chemical industry