Flow control for ethylene and propylene processing
Improving reliability and productivity of your process
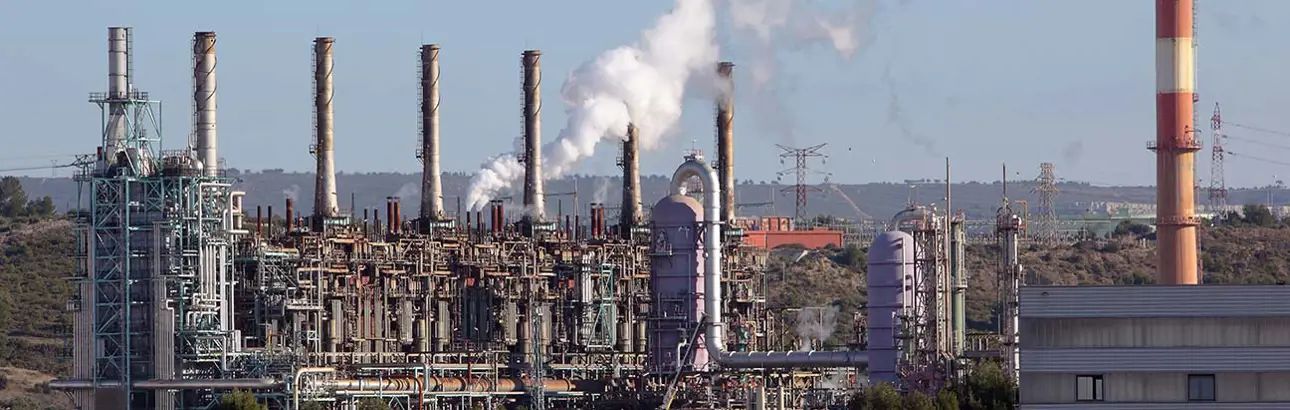
Over the past decade, demand for ethylene has steadily risen and so has the need for valve solutions that offer maximum reliability, safety and performance. Propane dehydrogenation uses propane to produce high-quality propylene. Steam cracking plants, which produce ethylene, are divided into three sections which together represent a very demanding environment. We’ve developed our valve solutions to ensure the utmost safety and reliability in your operations.
Reliability
Sustainable profitability
Uptime
Reliable valves and services for ethylene and propylene processing
After safety, uptime is the primary concern that ultimately determines whether or not an olefin plant will be sustainably profitable in an increasingly competitive global market. There are many critical valves within an ethylene plant. From cracking to quenching, valves are subject to a wide range of thermal conditions, corrosive medium and coke residue. In these demanding applications, inferior valves will quickly wear, leak and need service. Great valves will reduce fugitive emissions and extend the intervals between scheduled maintenance shutdowns.
Ethylene-specific valves are tailor-made to tackle applications challenges
Valmet offers a wide range of valves specifically designed to overcome the challenges of ethylene production including fuel gas control valves, shutoff valves and burner on-off valves. All are engineered and built with a focus on safety and uptime.
Ordinary seat and seals will not perform reliably in ethylene processing. That’s why Valmet uses advanced seat materials and complimentary seat geometries proven to provide better upstream and downstream sealing, eliminate leaks, prevent buildup and increase cycle life while also lengthening intervals between scheduled maintenance.
Friction and galling are the enemy of valve cycle life. Our proprietary coatings are carefully chosen for their thermal expansion compatibility with the substrate. The result is that many of Valmet's customers are now increasing the time between scheduled valve maintenance from 3 – 4 years to 7 – 9 years.
Trouble-free valves: Valmet's specialty for over 65 years
Valmet has put over 65 years of experience in the olefin industry into our full line of control, safety, and automated on/off valves. Our full-offering of the industry’s safest valves meet all the demands of ethylene processing to provide 7 to 9 years of uptime – compared to competitive valves that operate at roughly half that. We push the industry envelope in extending uptime and increasing ROI.
Valves for all processes
In the hot zone, the cracking and subsequent cooling occurs. We offer solutions for each step in this process including on-off and control valves for fuel gas, steam, quench oil, and other process media.
Compression zone valves
The compression zone is where compression, scrubbing and drying of the effluent occurs. Here, we provide valve solutions for secure compressor anti-surge, amine let down, and dryer switching operations.
Cold zone valves
The separation of components from the medium occurs in the cold zone. Here, we provide column control valves, refrigeration system high pressure drop valves, butadiene valves and many more.
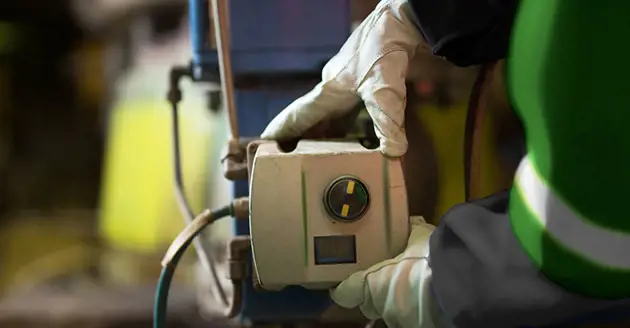
Catalyst regeneration valves
In the continuous catalyst regenerator, the catalyst is repeatedly withdrawn from the reactor, regenerated, and returned to the reactor bed. Efficient operation requires top quality lock hopper block, catalyst addition and removal, and chloride injection and addition valves. Our valves are extensively used in such critical applications.
Dryer sequence valves
Dryers remove hydrogen sulphide and trace amounts of water formed through the catalyst regeneration process. Valves here must withstand fluctuations in temperature while maintaining tightness over years of operation. Valmet's metal seated valves are extensively used in these applications.
Downloads
Flow control solutions and services for ethylene and propylene
Read more about chemical industry