New Valmet Pulp Dryer Fold-up Hatches Changing the game
Valmet’s new pulp dryer fold-up hatches have proved a game changer for Stora Enso’s Imatra Mills: The previously risky operation of pulp dryer hatches has become easier, faster and safer.
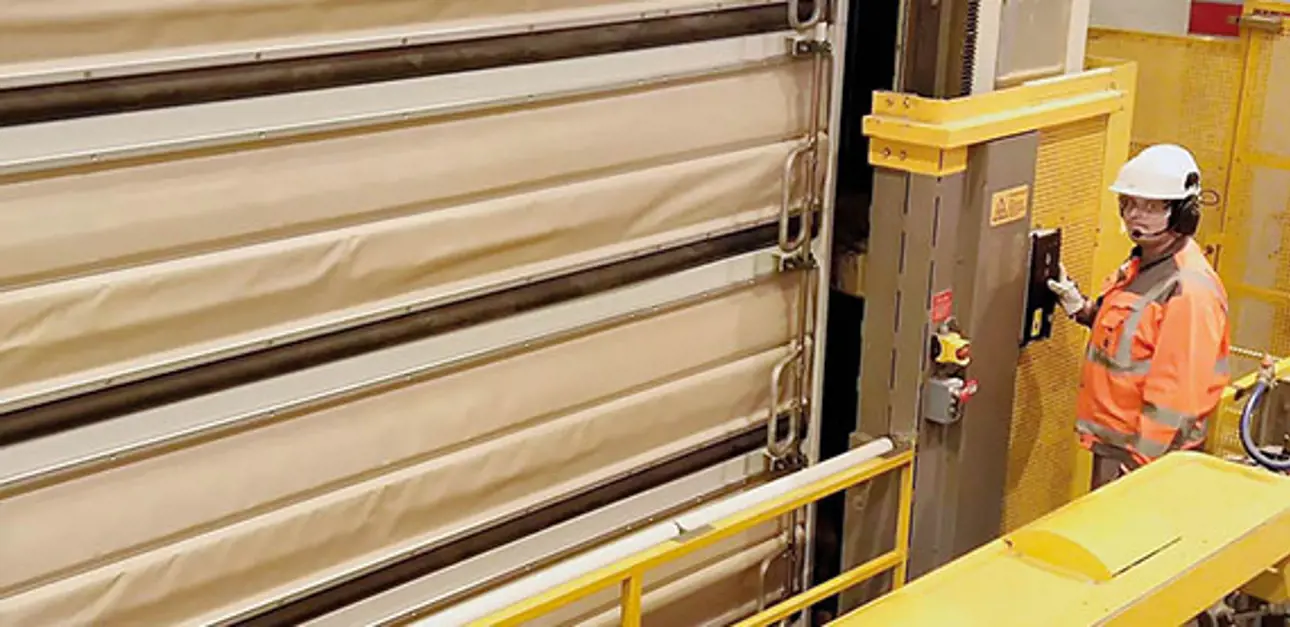
Valmet is continuously innovating new solutions to improve customer safety. In a pulp dryer, there are dozens of end hatches made from steel and/or aluminum.
“The operation of the hatches has been considered problematic at several mills, so we were thinking about whether there was a completely different way to make them,” says Esko Similä, Valmet’s Project Manager.
After intensive development work, new fabric end hatches were created: a lightweight easy access solution, with a new automated operation. All the hatches can be opened with a single button – and a considerably lower risk of injury.
One risk less
At Stora Enso’s Imatra Mills in Finland, the KU1 pulp dryer machine’s hatches were old and rusty, and approaching the end of their useful life. About the same time, an operator made a safety observation concerning the operation of the hatches. This prompted the mill to seek a better solution.
“The hatches make the dryer cleaning and checking easier, faster and safer.”
Stora Enso’s Imatra Mills were willing to pilot the new Valmet hatches and ordered the first Valmet Pulp Dryer Fold-up Hatch to replace two hatches at the dry end of the dryer. Once they were convinced it was a well-functioning solution, they ordered new end hatches for the entire pulp dryer.
Reserve Supervisor Jaakko Kinnunen from Stora Enso’s Imatra Mills is very happy with the performance of the new hatches: “We’ve got rid of heavy hand-opening hatches that caused unnecessary tearing and hence a risk of injury. The previous hatches also entailed a dropping risk and possible injury if the hinge failed.” He continues: “The visibility through the dryer has also improved considerably.”
Easier and safer operation
“Our operators are giving good feedback about how the hatches make dryer cleaning and checking easier, faster and safer,” says Kinnunen.
Several safety and operational benefits come with the new hatches. The new solution has considerably less joint surface, so it leaks less than the old solution, keeping the hot air in the dryer. The surface temperature of fabric is much lower than with steel. The new hatches enable an open view throughout the dryer and at the same time make it possible to cool down the dryer more quickly.
“I really want to credit Stora Enso’s Imatra Mills’ willingness to try new and innovative solutions, and the great people working there who are enthusiastic about launching new innovations,” says Similä.
“The whole project went smoothly, and we like the way Valmet reacts quickly if any problems arise,” concludes Kinnunen.
TEXT Heli Kankare
PHOTOS Stora Enso
Article published in Forward magazine 3/2019.