Two reasons data can make your processes more profitable
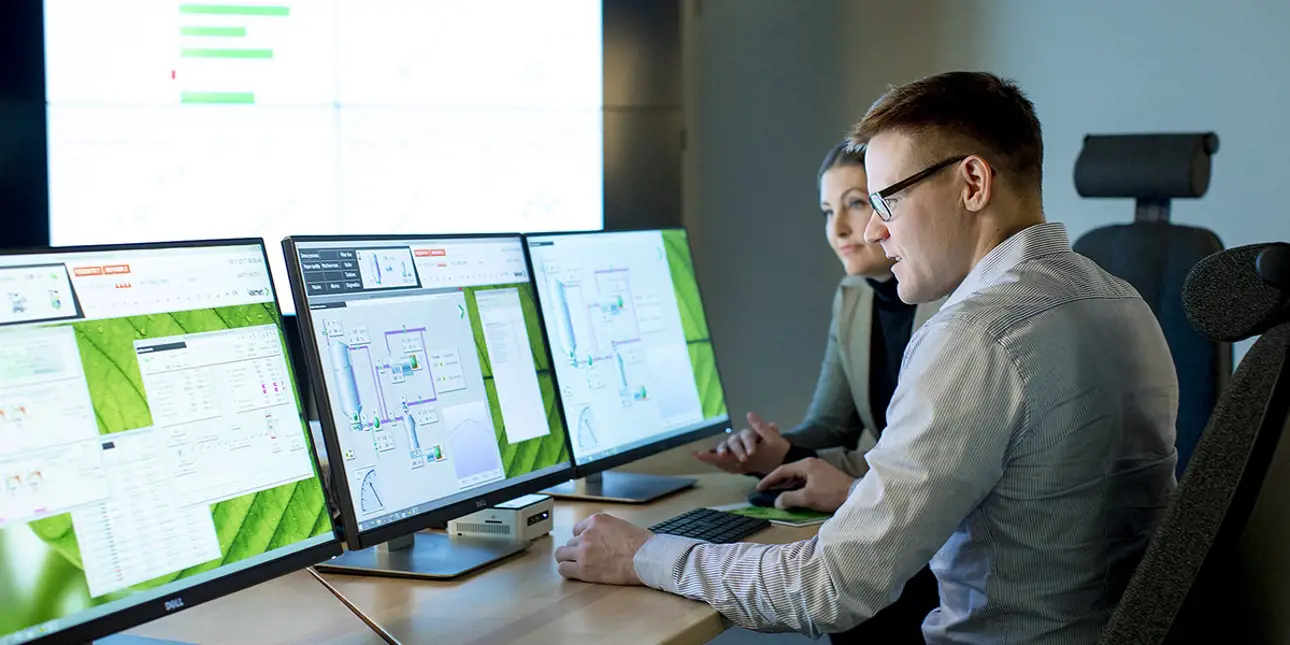
Today, we produce more data in 24 hours than human beings produced before 2006. Most of the data is created when devices are connected to the Internet and are in constant communication with each other.
Every smartphone owner has numerous examples of new applications and services built around data that save us time and money, and make our lives easier in multiple ways. As consumers, many of us rely on the navigation systems of our phones and cars, for example. They suggest a detour because of an incident on the road. However, although similar advisory solutions are also available today for industrial operations, their potential remains somewhat untapped.
From system-level control to a holistic process approach
In future, machines and equipment will be one part of a wider production system that creates value, with software transforming data into digital services and solutions.
For example, at a paper mill, a huge amount of data is created in smart process equipment, process measurements, automation systems, ERP systems and other systems essential to the business.
Traditionally, this data has been utilized at the system level to control a particular segment. But how can the collected data be utilized comprehensively to maximize the plant’s or mill’s production and profitability?
Thanks to the accumulated data, it’s possible to take a holistic approach and optimize production by evaluating the entire production chain. The target is to cut raw material and energy costs, minimize unplanned shutdowns and reduce the number of web breaks.
Operating costs can be reduced while increasing output at the plant and process level. For example, raw materials and energy can make up some 80 percent of paper machine production costs. With data-driven technologies, production can be optimized to achieve the optimal overall profit margin.
Turning the gray area of lost time into profit
The more machines can be kept up and running, the better the return on the capital investment. These principles and tools can be applied to every industrial operation.
Downtime is often a gray area in operating costs. For example, paper grade changes on a paper machine reduce production time. With data-driven technologies, these grade changes can be accelerated more effectively by identifying when the new production grade reaches a good quality.
Mill- or plant-wide optimization enables these operations to be better linked to production schedules. Instead of traditional production planning, this can be done by the planner setting high-level targets, but an Artificial Intelligence (AI) solution allocates these customer rolls to jumbo rolls and time slots to minimize the amount of trim and length losses, as well as grade changes. AI could also assist in relieving the bottlenecks in automated mill logistics by predicting the number of customer rolls that will be put through the system, and optimizing the production levels accordingly.
Paper machines can also be equipped with features that predict failures – but how effectively? Practice proves that a comprehensive failure predictor requires expert process knowledge to work, but typically consists of multiple solutions examining break history, as well as slow and fast developing faults such as process-related or mechanical web breaks. This typically leads to the fact that there may suddenly be a total of 5 or 6 different tools. How about having access to one integrated view instead of spending hours on drawing conclusions from different tools?
The utilization of data eventually affects all stages of the production process and benefits the business comprehensively by making the supply chain more efficient, decreasing life-cycle costs and adding value through more efficient processes.
And ultimately – by making it easier to make the right decisions.
Related reading