Innovative solutions help tissue manufacturers be more efficient and competitive
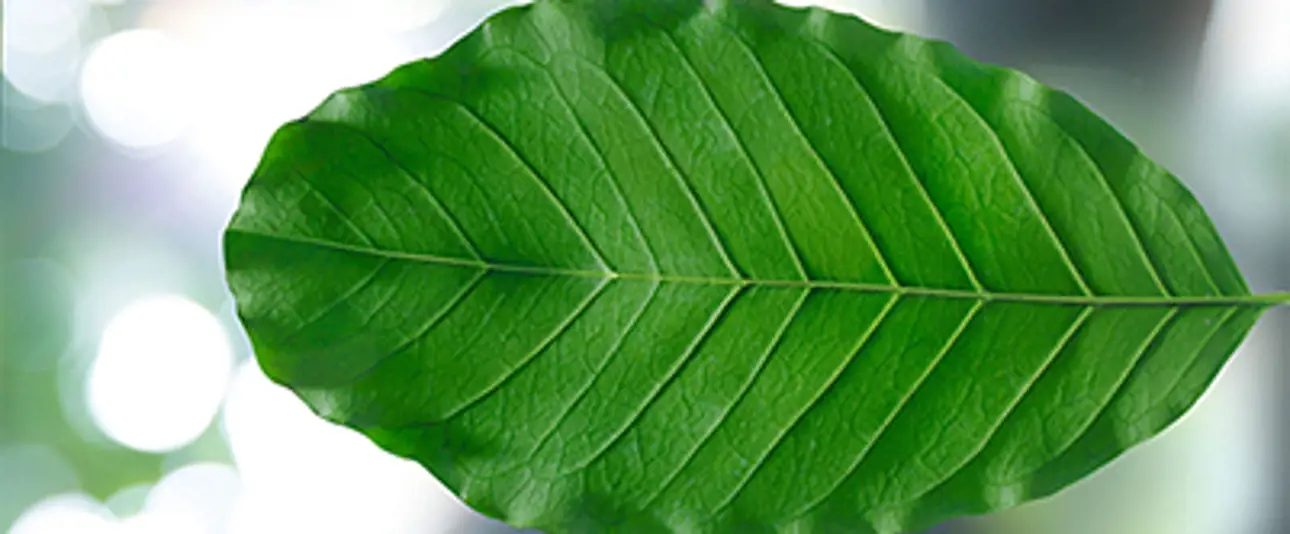
Competitive advantage in the tissue industry is paramount for manufacturers. Leveraging innovation in technologies and equipment provides key opportunities for gaining market share, especially when partnering with a world leader in tissue technologies.
Valmet continues to engineer solutions that improve production efficiencies and outcomes for manufacturers, as evidenced by the launch of three exciting new pieces of equipment.
Casmatic B23
For more than two decades, the Casmatic CMB 202 and 202 EVO bundlers have been highly regarded in the industry for productivity, ease of use, and versatility in medium and high speed bundler options.
Now, tissue manufacturers have an innovative new choice — the Casmatic B23.
A merger and complete redesign of the already popular 202 and 202 EVO bundlers, Casmatic B23 provides:
- Revamped, advanced hardware and software
- A completely redesigned frame with modular segments that can be assembled separately then joined, configured, and installed on a production line with simple electrical connections
- Continuous-feed chain belts constructed from individual panels, making them cost-effective and low maintenance. Unlike traditional conveyors, these belts do not require periodic realignment. In addition, the individual panels are detachable which allows for easy, efficient replacement in the event of damage — without adversely affecting productivity
- Continuous-feed belts constructed from individual panels that minimize product shifting and equipment adjustments that occurred when using traditional conveyor belts. The panels are also detachable, which allows for easy and cost-effective replacement without adversely impacting productivity
- Adjustable extractor fingers that eliminate physical replacement of teeth sets for various product formats
- The modular design simplifies and reduces installation time by up to 40% over current bundler solutions
- Safety guards that attach directly to the modular frame instead of being free-standing, significantly improving visibility while also reducing the equipment footprint by approximately 30%
- Training and labor cost savings — it operates exactly as the predecessor models
- Automatic format changeover prearrangement, a technology that can also be retrofitted onto standard machines after installation
- Smoother infeed launcher drives place less stress on the tissue product
- Six optional infeed combinations
- 23 bundles/minute bundling capacity
- Standard 500 millimeter bundle height
Casmatic F12
Folded tissue products — specifically facial tissues and paper napkins — generate significant global demand. As such, getting folded products to market reliably and quickly translates to competitive advantage for manufacturers.
The Casmatic F12 combines the consistency and trustworthiness of the Casmastic brand with folded product packaging capabilities that align with the entire Valmet ecosystem. The Casmatic F12 delivers high-quality outcomes at speeds up to 120 packs/minute, and can run either poly or paper packaging to support sustainability initiatives.
Casmatic Omnia 1000
Splitting product rows into multiple channels needs to occur at high speed in order to keep up with a log saw’s high-capacity output and customer needs. It’s been a long-time challenge for tissue manufacturers, with no viable solution other than an often cost-prohibitive investment in an additional log saw to divide upstream production speed.
Valmet engineers recognized and responded to the need with a completely new technological approach. The patent-pending Casmatic Omnia 1000 is designed around performance. Output can be configured to use only one, some, or all of the eight available channels — with diverter speeds reaching a maximum of 1,000 rolls/minute.
The one-of-a-kind dual-frame diverter mechanism coordinates flow between launchers, channels, and product conveyor belts to create a high-speed, adjustable production system that seamlessly meets the needs of each product batch for maximum flexibility. Since each component of the diverter system is independently motorized, the Casmatic Omnia 1000 can even accommodate channel bypassing to ensure constant production.
Contact the Valmet team for more information about the equipment. We look forward to hearing from and seeing you!