When it comes to wear in valves, not all materials were created equal
The Neles™ WearBlock™ Metal Matrix Composite makes a strong point for why you simply can’t afford to buy the cheapest valves available for demanding oil & gas applications. An investment into superior quality wear materials will pay itself back in the form of extended valve lifetime, superior predictability and improved safety and sustainability.
Perhaps not everyone shares a similar excitement over a new composite material with someone who has spent more than 30 years in powder metallurgical development like myself. But the real-life benefits this material delivers can’t easily be ignored. Wear, and erosion in particular, can have serious and costly consequences if not addressed correctly.
So, what would you say if we claimed that by selecting a valve equipped with our unique solution could reduce on-site valve-related HSE risks by up to 90% while simultaneously increasing said valve’s lifetime by 800%? Well, this is exactly what I claimed in our latest webinar, of course based on recorded data from real-life Fluid Catalytic Cracking (FCC) applications. So, when you factor in that it lasts 8 times longer and all but eliminates the risk of catastrophic valve failure and expensive unexpected downtime, the slightly higher unit price of a valve with Neles WearBlock technology become almost inconsequential.
If you’re not 100% convinced, perhaps you’d like to view the recording of the Worn out -webinar where I discuss the importance of the material composition and thickness of wear protection in oil & gas industry valve applications. I invite you to find out why we are so excited about the Neles WearBlock solution. And if after viewing the webinar recording you are still left with some questions, please don’t hesitate to get in touch.
Discover more around the topic
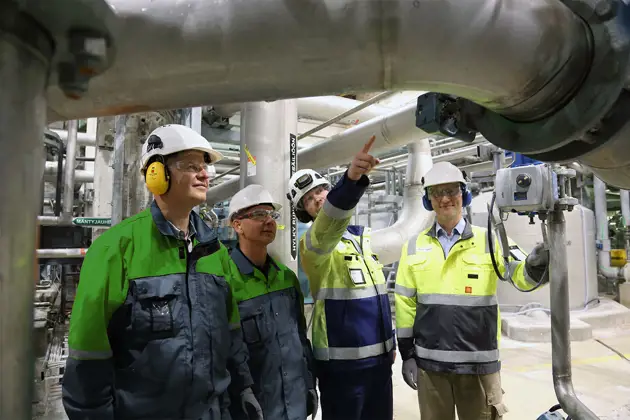
Subscribe to our newsletter
Subscribe now to flow control newsletter and receive the latest insights directly to your email.
Subscribe