Interview with resident engineer Pertti Puurunen
Flow control services are integral part of customer plant maintenance. Working with customers is rewarding and challenging in a positive way. We interviewed resident engineer Pertti Puurunen. He works daily in close collaboration with major flow control customers.
You work as a Resident Engineer. Tell us briefly what it means.
I serve as a dedicated contact person for specific customers. I answer all their questions and respond to their needs concerning valves. My work includes two areas: planning and management of maintenance shutdowns, as well as field device management. I’m responsible for three major customers in the pulp, paper, mining and chemical industries. I spend around one day a week with some customers, and longer periods with others, even several weeks in connection with shutdowns and their preparation. Of course, I also visit them whenever necessary.
Shutdown planning usually starts a year ahead. First, we compile a list of the necessary work, including periodic work. Any defects detected through condition monitoring will be added to the list later. We also acquire all the necessary spare parts in advance to ensure smooth implementation. Around one month before the shutdown, together with the customer, we make sure that everything has been prepared correctly, and that the spare parts are available. I’m responsible for the supervision of work during a shutdown.
I also have a connection to the systems of one of my customers. I review the condition monitoring of their mill, analyze valve diagnostics, and send lists of my observations and any defects to the customer. In connection with such work, I may sometimes find a few faults, which must then be reported to be included in the shutdown work list.
They only have one thing to worry about, and we take care of the rest.
Can you describe your typical workday if there is one?
My working days vary a lot. I carry out shutdown planning almost daily. I also regularly follow condition monitoring to detect any issues. If a valve is acting up, sometimes I repair it myself. If a customer has a challenge or problem, they contact me first and I check it out.
I also make suggestions for replacement valves when devices come to the end of their service life. With one customer, I’m responsible for flow sensors and other field devices. The customer is happy with the service, as they need no resourcing for this purpose.
During a shutdown, the working days are long, and work is also carried out on weekends. As part of our availability service agreement, we also service our competitors’ devices during a shutdown. This makes planning simpler and the service easy to use for the customer. They only have one thing to worry about, and we take care of the rest.
You work closely with customers. How do you feel about that?
Solving challenges together is also very rewarding, and we learn from one another. After being a customer for 20 years, I can serve my own customers better, as I know what they want and require. It’s good to hear that my work is appreciated
I truly enjoy working with our customers. After being a customer for 20 years, I can now serve the customers better, as I know what they want and require.
What are the benefits of Valmet's Resident engineer services?
Valmet’s flow control expertise and know-how have developed through decades of experience, so we can provide our customers with services, development ideas, tips and maintenance recommendations that are genuinely necessary. This also saves the customer’s valuable time for other important tasks, as the Resident Engineer takes care of the valves as a turnkey service in shutdown planning. Such expertise cannot be purchased elsewhere.
Our Valve Performance Moitoring service on top of Field Device Manager tools has also been found useful. Unnecessary scheduled maintenance has been eliminated. Previously, the valves were usually replaced when we felt that it was the right time. Now, thanks to the service, only critical valves that are actually faulty are serviced or replaced. The program provides notification of future faults in good time, so unnecessary interruptions and shutdowns are avoided.
What are your current efforts to improve service and cooperation with customers?
We are starting to use Valmet customer portal with our service customers. Through the portal, the customer can see their own installed base with spare parts and service instructions. All documents, such as availability and diagnostics service documents, can be shared with the customer. Having important resources available in the same place will further improve cooperation and transparency. Many customers are already using the portal, which is being developed based on customer feedback and needs.
Many customers are also aiming to upgrade their positioner base to the new intelligent Neles NDX ™ 2.0 valve controller. Thanks to its ease of use and enhanced accuracy, the customer can benefit from better process quality and profitability. The Neles NDX 2.0 also reduces air consumption, potentially by up to 90%, which translates to lower energy costs and reduced CO2 emissions.
Any other things you want to highlight/mention.
Well-planned is half-done: shutdown planning takes the same time as the implementation. Advance planning and scheduling are key, in addition to determining who does what, where and when. Together we can get things done smoothly!
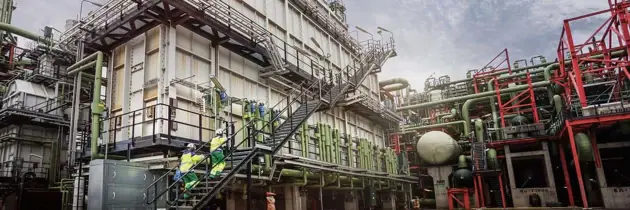
Services for valves and pumps
Reliability is at the core of every successful process plant’s operations. It leads to higher availability, safety – and profitability. By taking a proactive approach, you can stay ahead and gain deeper understanding of your plant and equipment. Valmet helps to transform plant data into valuable information. These insights enable you making the best decisions on which valve or pump to monitor, what to repair, and what to replace.
DiscoverRead more about Flow control services