Don’t get left behind: Upgrade your processes to fieldbus connectivity with Flowrox™ pumps
In an era where efficiency and reliability are paramount, the industrial sector continually seeks technological advancements to refine operations. A pivotal shift in this quest for enhancement is the adoption of fieldbus connectivity in place of traditional analog signal control. Flowrox pumps, particularly the FXM metering pump series, exemplify this transition by incorporating Modbus TCP, Ethernet/IP, and Profinet, offering a glimpse into the future of industrial automation. Our expert Simo Rounela, Automation Product Manager for Pumps, was asked to answer the question: “Why should you go for fieldbus connectivity with Flowrox pumps?” Read his thoughts below.
The superiority of fieldbus technology over analog signal control
Unlike an analog signal control, which transmits a single variable and is susceptible to noise and signal degradation over long distances, fieldbus technology offers robust communication capabilities. It enables the transmission of multiple data types, including diagnostic information, over a single cable. This not only simplifies wiring but also enhances data accuracy and system diagnostics, facilitating predictive maintenance and reducing downtime.
Comparing fieldbus technologies: Modbus TCP, Ethernet/IP, and Profinet
Each fieldbus technology comes with its unique strengths, making them suitable for different industrial applications:
- Modbus TCP is renowned for its simplicity and interoperability across various equipment and network systems, making it a cost-effective option for many applications.
- Ethernet/IP, which is widely used in the United States. It excels in integrating industrial devices over an Ethernet connection, offering high-speed data exchange and compatibility with standard internet protocols.
- Profinet, which is preferred in Europe and for applications requiring precise real-time data transmission. It supports a wide range of communication relationships and is known for its flexibility and scalability.
Harsh condition requirements
Flowrox pumps are engineered for demanding applications, often operating in harsh conditions like mining sites. These environments require robust technology not just in terms of physical durability but also in communication reliability. Fieldbus technologies provide substantial advantages here, offering higher protection against electromagnetic interference, moisture, and physical damage, thanks to advanced shielding and error-checking capabilities. With excellent IP ratings, Flowrox pumps ensure sustained operation and data integrity in even the most challenging conditions.
Flowrox FXM metering pumps are equipped with the latest fieldbus technology.
Fieldbus for enhanced analytics and condition monitoring
The integration of fieldbus technology into Flowrox pumps is not just about immediate efficiencies and reliability; it's also about laying the groundwork for future advancements in analytics and condition monitoring. Through fieldbus data, operators can gain insights into pump performance, predict maintenance needs, and optimize operational parameters in real-time, thus extending the life of the equipment and improving overall system performance.
Conclusion
The transition to fieldbus connectivity offers a multitude of benefits over traditional analog control, including improved data accuracy, enhanced diagnostics, and the ability to transmit multiple variables over a single connection. For users of Flowrox pumps, this means not only a more reliable and efficient operation today but also a platform for leveraging advanced analytics and condition monitoring capabilities tomorrow. As we move forward, the importance of selecting the right fieldbus technology — considering the specific requirements of your operation and the harsh conditions in which you operate — cannot be overstated. With the right approach, fieldbus technology can transform the way industrial processes are monitored, controlled, and optimized.
Text by Simo Rounela. For more information, contact via e-mail simo.rounela@valmet.com
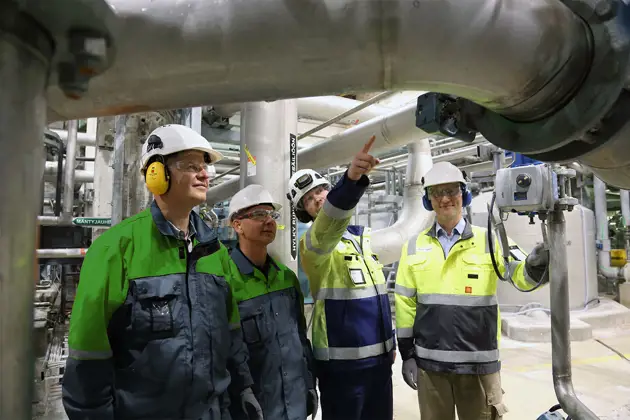
Subscribe to our newsletter
Subscribe now to flow control newsletter and receive the latest insights directly to your email.
Subscribe