A catalyst, by definition, is a substance that enhances a chemical reaction. In the refining industry, catalysts are extensively used in many upgrading processes. One common upgrading process in refineries is the Fluid Catalytic Cracking unit (FCC) unit, which converts heavier distillation cuts into lighter, more profitable products, such as gasoline. This unit has many severe service valve applications that require special attention to design and material selection.
One such application that is historically considered “high maintenance” is the oil slurry control valve in the bottoms circuit. The catalyst used in the FCC is very small in size, but, over time, this catalyst breaks down to an even smaller size particulate and eventually makes its way to the slurry oil. These fine particles, often referred to as cat fines, are very dense and abrasive and can quickly erode conventional valve trim.
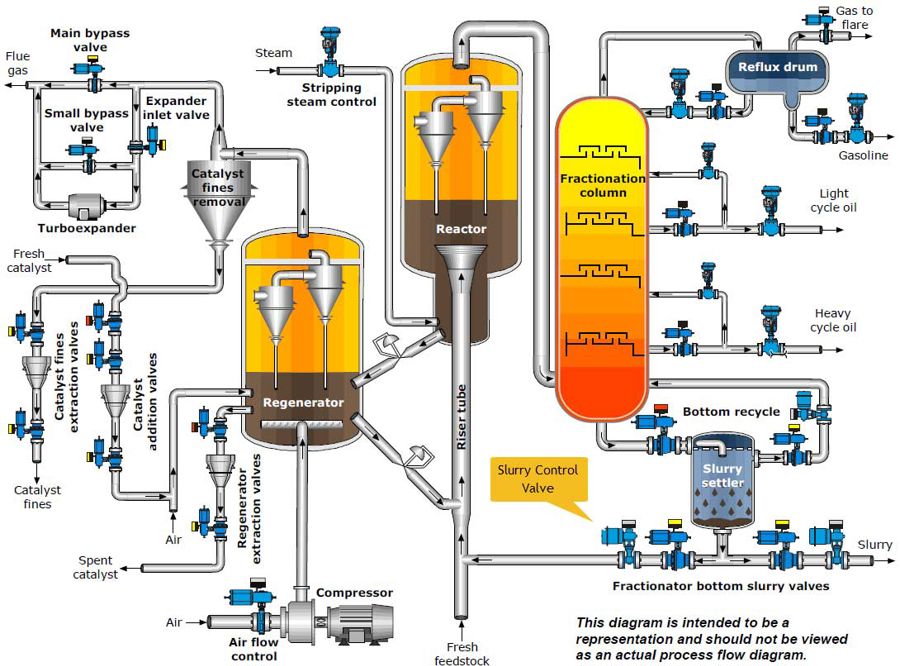
Erosion-resistant valve design can improve the reliability of an FCC unit
An FCC unit typically operates for five years between turnarounds. Erosion is relatively benign during the first three years after a turnaround; however, the last two years can be very erosive, due to the accumulation of catalyst fines. Typical control valves in the bottoms circuit are rotary eccentric plug or V-ball control valves. During the last two years of an FCC run, these valves can fail within six months. Replacing these valves forces the FCC to shut down and/or to operate in an unsafe condition. As valve reliability can be one of the most important cost factors impacting FCC profitability, reliability can often override cost considerations. In these extreme erosive cases, we have successfully replaced existing rotary control valves with a fully ceramic-lined ball control valve.
The Neles E-Series ceramic ball valve offers one of the most erosion-resistant designs available on the market.
- All ceramic wetted parts, ensuring the best possible erosion resistance.
- Special zirconia grade offers impact resistance exceeding most other ceramics
- Excellent thermal shock resistance
- Proven reliability – we have numerous installations in high-abrasion applications showing significant service life improvements
- Same take-out dimensions as existing rotary control – ease of replacement, no piping modifications needed
Costs associated with valve replacement in an FCC unit can be particularly high, as these valves can range from 2”-10” in size. However, we have found refineries to be pleased with both the elimination of frequent valve replacement costs and the dramatic improvements in FCC unit uptime and process throughput – all of which went directly to the unit’s bottom line.
Tailored performance with new materials
Our metal matrix composite (MMC) materials are another key innovation in the field of wear protection. The superior hardness of ceramics and the toughness of metals are incorporated into our metal matrix composite materials, which thus offer the best combination of wear resistance and mechanical reliability. The Neles MMC materials are available in WearBlock™ bi-metal valves, but also as an option (hybrid-E) for ceramic insert parts in our ceramic ball valves. Your valve performance can be tailored to align with your service and maintenance strategy. Balancing out process requirements, planned maintenance schedules and lifecycle costs, we can help you select the valve solutions that work best for you. By pairing your valves with our smart devices, you can monitor valve condition and performance in real time, allowing for well-planned maintenance and service operations without any nasty surprises.
The text has been updated in April 2022, due to the company name change to Valmet.