Five tips for improving your production’s energy efficiency
In today’s world, improving energy efficiency is not just a cost-saving measure but a crucial step toward sustainability. Industrial companies, with their significant energy consumption, have a unique opportunity to make a substantial impact. At Valmet, we are committed to reducing carbon dioxide emissions by 80 percent by 2023 in our own operations – for example, by replacing fossil fuels with renewables and implementing energy efficiency improvements. Here are five tips for improving energy efficiency in production based on our actions at Valmet’s Shrewsbury valve manufacturing site in the United States.
1. Fix compressed air leaks in the production pipeline
Our focus has been on identifying compressed air leaks in the manufacturing process pipeline. The production machines use compressed air to operate; it is like electricity for them. Air leaks cause unnecessary electricity use, which can be prevented by eliminating the leaks. Reducing air leaks in production has an impact on overall carbon emissions because less electricity is consumed. During the 2020–2021 period, 86 significant air leaks were identified from within hoses and fittings, leaking a total of 122.6 standard cubic feet per minute (SCFM) of air. The actions included an evaluation of weekend air leaks, and it was decided to install Valmet’s Jamesbury™ shut-off valve with a Valvcon™ intelligent actuator to automatically shut off the compressed air during weekends and at certain times of night.
2. Optimize heating and cooling
To help maintain a stable internal environment and reduce the need for excessive heating or cooling, we decided to invest in a new Heating, Ventilation, and Air Conditioning (HVAC) system in 2022. This system provides precise control over the indoor working climate, ensuring comfort throughout the year. The system is energy efficient, reducing both energy consumption and utility bills.
3. Optimize working temperature at the premises
Investing in modern energy-efficient machinery can lead to significant energy savings. Look for equipment with high energy ratings and consider the long-term savings over the initial investment. Regular maintenance of existing equipment also ensures it operates at optimal efficiency. In addition to the new HVAC system, we replaced the older make-up air units with newer models that could maintain the indoor temperature steadily at 65 °F (~18 °C). The older units consumed a lot of electricity, as they had to heat air from 40 °F to 70 °F each time.
4. Utilize renewable energy sources
Incorporating renewable energy sources such as solar, wind, or hydrogen can reduce reliance on fossil fuels. Onsite renewable energy generation can provide sustainable and cost-effective energy supply while reducing the company’s carbon footprint. In Shrewsbury, we have now finalized the use of hydrogen fuel cell system for charging 28 forklifts, targeting a reduction in electricity use. Hydrogen fuel cells replace the old lead acid batteries in forklift power generation. With hydrogen fuel cells now in place, we have estimated a 30 percent reduction in carbon dioxide emissions during the first year, and 51 percent after six. We will regain 585 m2 of factory floor space from the charging area, which will reduce the wasted motion for the operators.
5. Use energy-efficient lighting
One of the actions focused on energy-efficient lighting. We decided to replace fluorescent light bulbs with LED lights throughout the facility. LED lights are significantly more energy efficient than fluorescent bulbs. They convert up to 95 percent of their energy into light, with only 5 percent lost as heat. LED lights have a much longer operational life, typically lasting between 25,000 and 50,000 hours. They are also more environmentally friendly. They do not contain hazardous materials like mercury, which is present in fluorescent bulbs.
To date, the site’s electricity usage has dropped by approximately 37 percent, reaching the target level of 10,027 MWh in line with Valmet’s climate program targets.
By taking these steps, industrial companies can not only reduce their energy costs but also contribute to a more sustainable future. Energy efficiency is a win-win strategy that benefits both the bottom line and the environment.
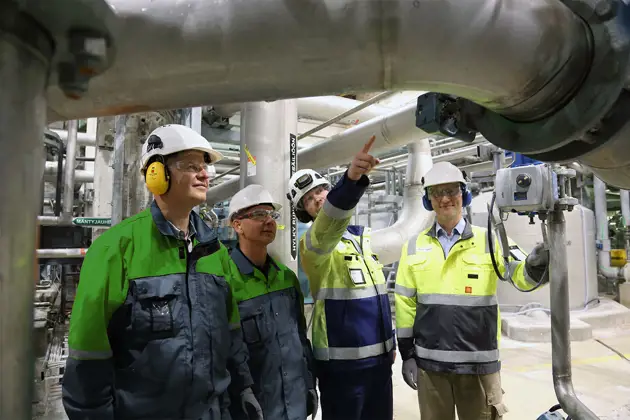
Subscribe to our newsletter
Subscribe now to our 'Go with the flow' newsletter and receive the latest insights directly to your email.
Subscribe