Observations from the field: improving recovery boiler operations
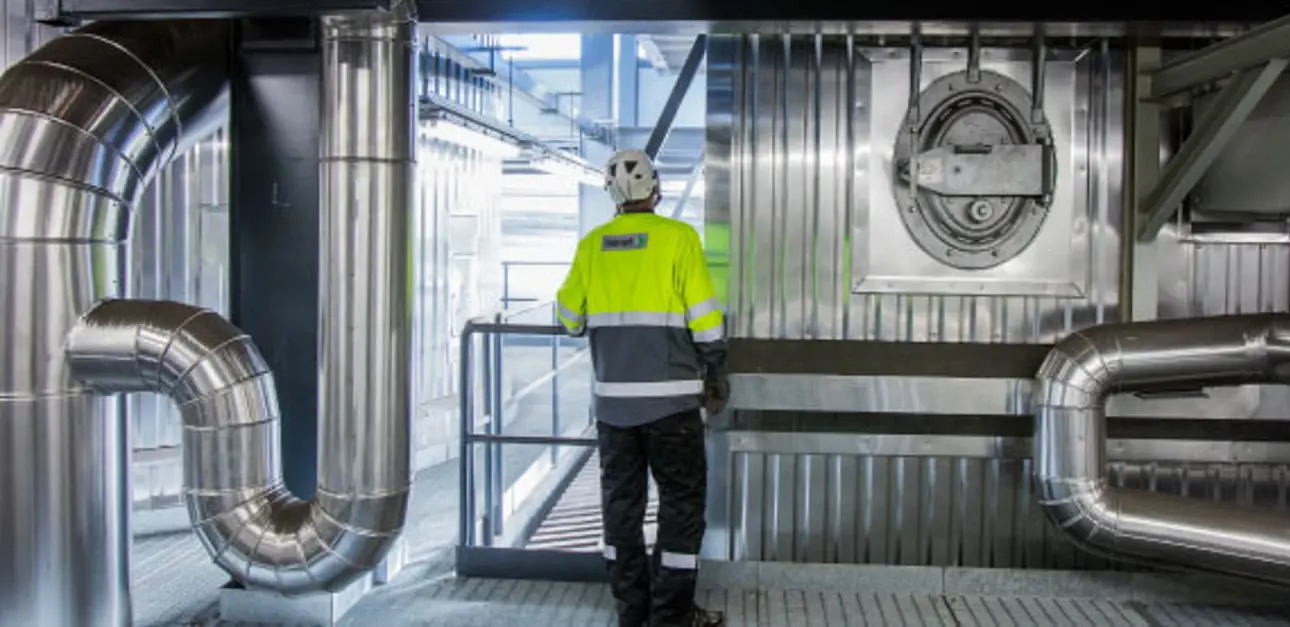
In your role you work closely with pulp and energy producers to help solve problems and achieve specific goals. Have you observed any common themes or universal concerns across the many mills with which you’ve worked?
Over the past 10+ years I’ve helped mills solve problems in many different ways, including: outage inspections & outage management, condition assessments, boiler emissions tuning, advanced tuning & operations, engineering studies troubleshooting & root cause analysis, training & simulators, chemical cleaning, steam blows, vapor phase cleaning, commissioning services and service agreements. At the end of the day, safety, performance, and sustainability are at the heart of all plant operations. Those three factors (safety, performance and sustainability) play critical roles in the development of all Valmet pulp and energy services.
Earlier this year, you highlighted Valmet’s Liquor Spray Station in a webinar about 'improving personnel safety and recovery boiler performance.' What makes this technology so important?
Optimized liquor firing has a critical impact on recovery boiler operation. The Liquor Spray Station moves with the boiler as it changes, expands, or contracts. Additionally, working around recovery boilers typically requires safety mitigation efforts to prevent personnel injury. Valmet Liquor Spray Station factors in both considerations with a design that optimizes the spraying of black liquor and keeps operations and maintenance safe.
While there are many examples, a few features worth mentioning are: the BLRBAC-approved safety door that isolates service work from the boiler and creates a safe working environment, the nozzle cutter for optimal spray distribution and the patented cradle design that securely locks the liquor nozzle in place. We are also able to use mobile furnace cameras to commission and tune the liquor sprays. At one mill recently, we installed four liquor spray stations on a recovery boiler and observed the customer improve reduction efficiencies by six percent.
What is an example of an important everyday maintenance item that might often get overlooked?
Boiler tube deposit inspections. Preventing tube failures in recovery boilers is vital to safe and sustained operations. Scale deposit build up on boiler water wall tubing can result in costly energy losses and loss of tube cooling, which may result in tube failure. Periodic chemical cleaning of the boiler tubes is also important, but if improperly performed, can also result in tube damage. This is where Valmet Field Services and Liquor Optimization teams can help.
Utilizing Valmet Boiler Tube Deposit Inspection services, we can get the clearest picture possible, providing mills with a virtual look inside their boiler water wall tubes. This non-destructive scale deposit measurement can be made at any number of locations on the boiler water wall, giving us a comprehensive idea of tube wall conditions. Valmet's inspection services provide maintenance personnel with another tool for the development of a complete boiler water chemistry control program. You can take a closer look at this technology and how it works by watching the video on Boiler Tube Deposit Inspection Services.
Are there any other best practices you can suggest to customers as they review their goals and plan for future outages?
Don't be afraid to ask questions of your field service partners. Qualified service engineers have the experience and equipment to help you optimize your equipment. Also, don't overlook the need for tune-ups. Many mills and/or plants must demonstrate compliance with EPA MACT requirements regarding boiler and/or process heater tuning for carbon monoxide emissions. These, and other tune-up options, are quick and easy to schedule and complete. More information about Valmet’s EPA MACT Tune-up Services can be found here.
For more information on improving recovery boiler operation and safety, view our webinars and contact your Valmet representative.