The rewinder as an enabler
Converting tissue paper to finished products is not always as straight forward as it can look, especially if the final product will be folded. Quite often a step between tissue machine and converting is needed. That’s were the rewinder comes in the play.
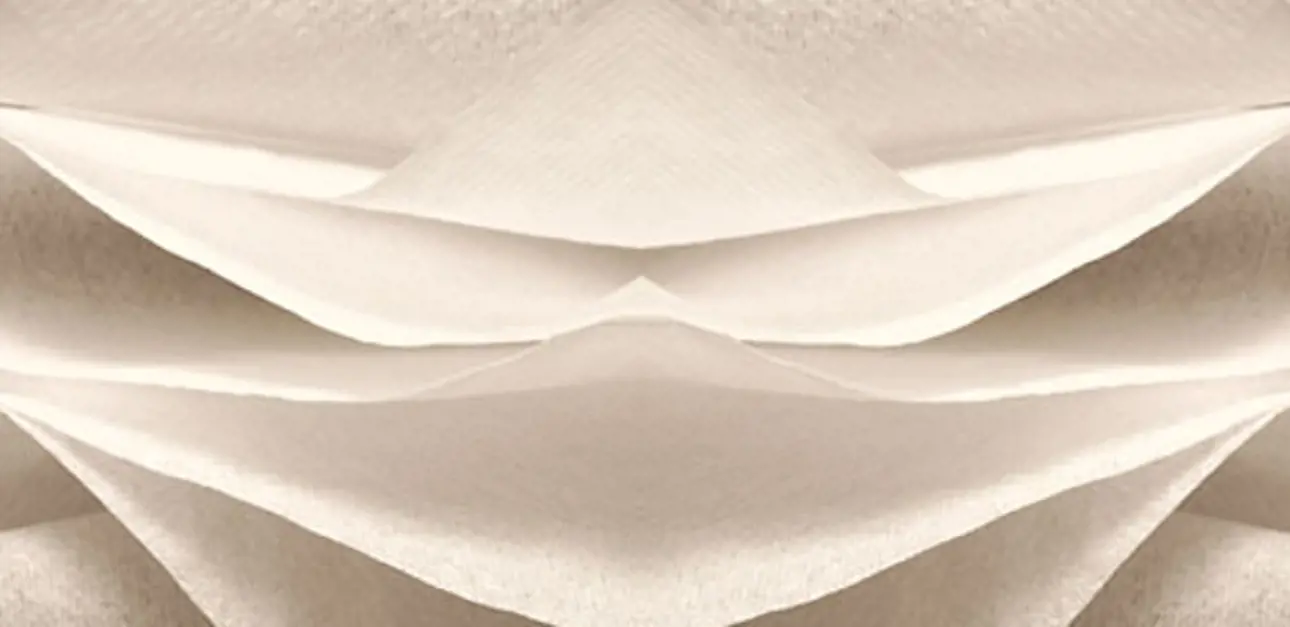
The mother reel coming from the tissue machine is the first stage of a quite long converting journey before the tissue paper ends up in the consumer market as toilet roll, kitchen towel, napkin, handkerchief etc.
To convert tissue folded products and in many cases rolled products, the mother reels need to be combined, or slit, or slit and combined, depending of the characteristic of the finished converted product. To enable this the mother reels are processed through a tissue combiner/slit rewinder machine.
The rewinder needs to have a versatile design since different mill set-ups and different desired end products highlight different needs of a rewinder.
The many roles of the rewinder
Paper mills that have a converting plant integrated in their organization produce mother reels from the tissue machine. The rewinder combines and slits those for wholesale dealers and/or for their internal converting plant.
Paper mills that do not have any converting plant will produce mother reels from the tissue machine and then combine and slit jumbos for wholesale dealers or converting companies.
Companies that only convert tissue rolls, folded and interfolded products can buy already combined and slit rolls from a wholesale dealer or mother reels directly from the mills. If the strategy is to purchase mother reels, they can use a rewinder for combining and/or slitting reels according to their production needs.
Key requirements for rewinding
The challenge for the slitter rewinder is to produce a maximum number of combined and/or slit reels per day corresponding to a pre-defined specification with regards to number of plies, number of slits and desired roll diameter. These combined and/or slit reels will be converted one more time by the converting plant (integrated or not) to a finished tissue product to satisfy the market request.
Any converting action has influence on the paper characteristic produced at the tissue machine. The embossing process increases web thickness with a reduction in tensile, and an inaccurate tension control may have a negative effect on the percentage of crepe. The rewinder, even if frequently located in line with the tissue machine, could be considered the first step of the converting process and the rewinding challenge is to ensure that as much as possible of the original paper characteristics are preserved.
Another thing to take into consideration is the fact that converting machines have a different efficiency and machine availability compared to tissue machines. The production capacity, according the converting or market demand characteristics, need to be calculated in advance in order to avoid any potential delay on the tissue machine production.
When correctly configured, the rewinder is the toolbox that enables the tissue machine output to satisfy every tissue consumer’s need throughout the whole production chain.
"When selecting a rewinder, it´s important to consider any future needs that may arise in your business."
Future enabler
When selecting a rewinder, there are several key parameters that need to be considered to calculate correct production output in terms tonnage, number of plies, number of slits and desired roll diameter. Web width, basis weight, density and size of mother reel all have an impact on the production output. Crepe ratio influences how many meters will be winded on each roll while how many unwind stands that are needed depends on how many plies are needed. More plies will consume more mother rolls from the tissue machine. The number of slitters depends on the desired finished roll widths. Finished reel diameter range and core diameters are also important parameters for the production output from the rewinder. If there is a need for enhanced smoothness in the end product, a calendar can be added as well as other features.
However, the most important thing is to select a rewinder that preserves the tissue quality generated in the tissue machine with equipment that can adapt to any future needs that might arise in your business. Instead of a possible future bottle neck, the rewinder can be your future enabler.
Contact person:
Andrea Coluccini andrea.coluccini@valmet.com
Product Sales Manager, Tissue Rewinders
Category: Guidance
Industry level: Intermediate
Est. read time: 4 minutes
Summary: Describes different scenarios in the transformation of tissue mother rolls into finished products, so that the tissue machine output can meet the needs of every tissue consumer throughout the production chain.