Rethinking energy sustainability in tissue production
When it comes to sustainability in tissue production, simply presenting a “green corporate image” is no longer good enough to stay competitive. Authorities around the world have set greater environmental legislative requirements for tissue manufacturing, and consumers everywhere want certified environmentally-friendly products. That means tissue mills need to take concrete steps for more sustainable production processes.
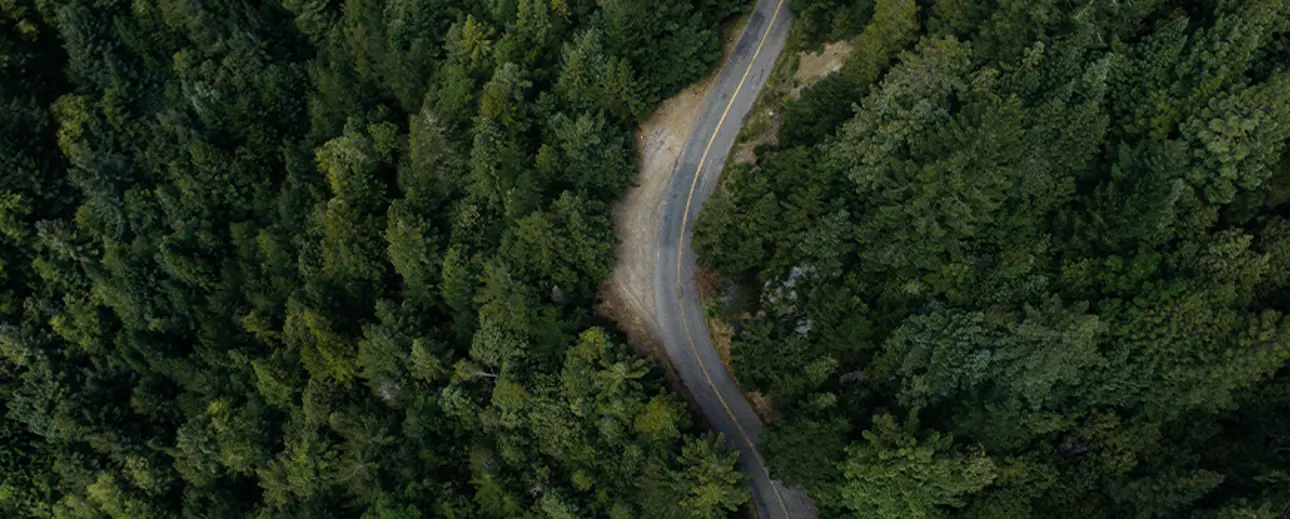
Energy consumption has long been an area of interest for many manufacturers. Tissue making is a particularly energy-intensive industry, and today the challenges are greater than ever. The growing demand for tissue globally is increasing energy needs as businesses work to produce more at a faster and faster rate.
While the goal of more efficient energy use is nothing new, the focus has traditionally been on recycling “wasted” energy in the tissue making process. Today’s challenges mean that the time has come for a new way of thinking and a more holistic approach. The starting point should be limiting the amount of energy needed in the first place, and the next step is to find ways to make required production processes more efficient. These two efforts greatly limit lost energy in production, which can then be addressed as a final consideration.
Step 1: Reducing demand
There are many ways to limit the energy needed for making tissue, but the most efficient action a manufacturer can take is to improve post-press dryness. Greater post-press dryness can significantly reduce the demand on the Yankee dryer, which in turn limits the dryer’s energy output.
For example, if a mill producing 200 tons of product every day increased post-press dryness just slightly, from 44% to 46%, it would reduce the amount of water that needs to evaporate by 98 kilograms per ton. The resulting energy savings would be around 166 kWh per ton, which is as good for the mill’s bottom line as it is for the environment. Based on Central European energy prices, that translates to over €350,000 in savings each year.
But this is only the start. As previously noted, true energy sustainability demands a holistic view, which means considering the entire production line. Every piece of technology in a mill offers potential for energy savings. Reducing the flow through the headbox, for example, minimizes the energy consumption of the approach system with little impact to product quality.
Step 2: Increasing efficiency
Even after minimizing the need of energy, tissue making remains quite energy-demanding. However, by again taking a view of the production line as a whole, it is possible to find ways to make existing processes much more efficient.
Here, the first consideration is mill design. How process equipment is arranged relative to one another as well as the dimensioning of equipment according to the products being manufactured can have a significant impact on energy consumption. For example, oversized equipment can unnecessarily increase the power needed for stock and water pumps, driving up production costs. Thus, ensuring an appropriate mill design from the start can mean more efficient production in the long-term.
Smart automation also plays an important role. Even if a mill is well-designed with the right machines, it needs to be utilized in the most efficient way to get the most sustainable result. An intelligent control system helps manages processes and maintains center-line parameters automatically. It can also include features such as valuable feedback on energy and resource consumption, as well as remote diagnostic possibilities for online support from experts.
While thinking about utilization, it is also worth considering the skill levels of your operators. Smart controls can solve many issues, but if an operator lacks the expertise to interpret feedback from systems and use the technology in an efficient way, it will not be possible to optimize the mill’s full production capacity. All operators should therefore receive adequate training on how to best use the mill’s equipment and the behaviors that support sustainable production.
Step 3: Recovering losses
Of course, even with the most advanced technology and best operational practices, a certain degree of heat loss is still unavoidable. The step for reducing energy consumption is therefore figuring out how heat can be recovered and put to different use.For mills located in areas with considerable heating needs, there are already smart ways to recycle heat waste. An air to water recovery system is a valuable tool that can be used for heating parts of the facility from the machine hall to administrative offices. This contributes to energy sustainability as well as reducing power costs related to heating.
Elsewhere, there remains a challenge to continue developing new technologies that not only capture losses, but transform them into useful forms of energy for other purposes. Today for example, innovations are making it possible to recover kinetic energy from the tissue-making process and convert it into electricity that can be put back into the production line. These possibilities, along with many other ongoing developments, will soon make it even easier to approach sustainability holistically – and achieve unprecedented levels of energy efficiency in tissue production.
More information about a sustainable business.
Category: Sustainability
Industry level: Intermediate
Est. read time: 5 minutes
Summary: This article examines different steps that tissue mills can take to enable more sustainable production and stay competitive.