Pioneering innovations in tissue making for over 50 years
Mar 4, 2025
Valmet has a rich history of innovation in the paper and tissue manufacturing industry. This is the story of how relentless pursuit of excellence has transformed the tissue industry, one invention at a time.
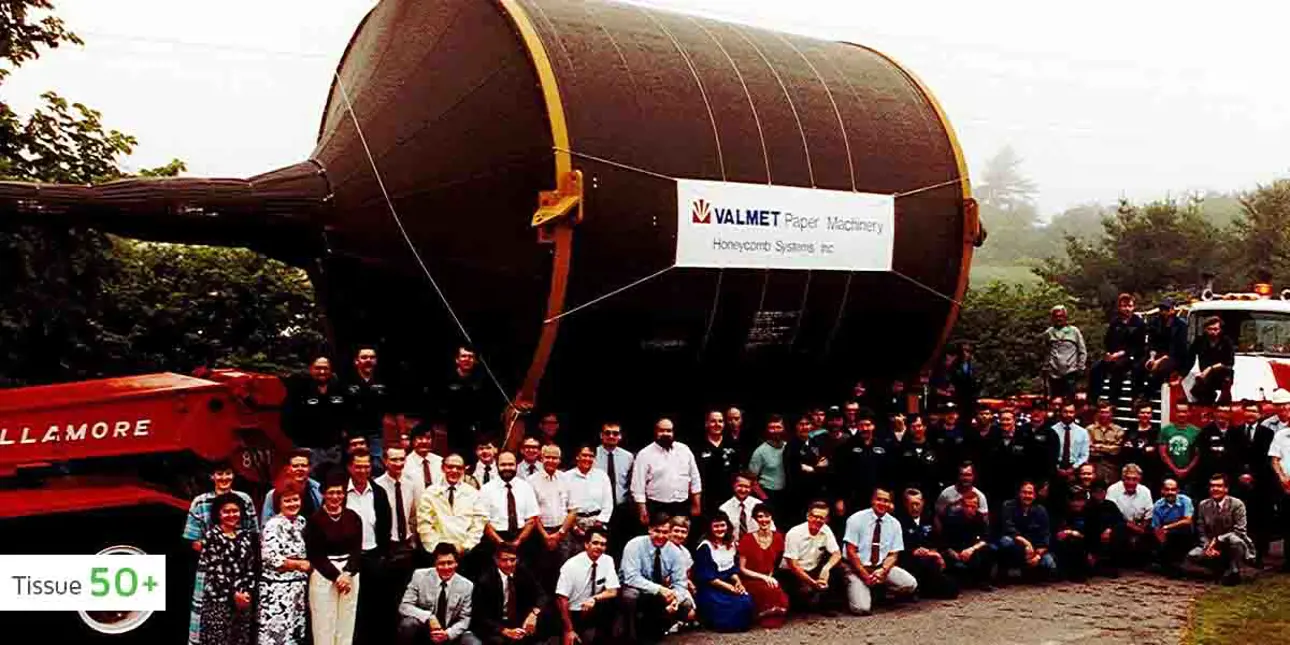
Early innovations bring challenges and insights
In the early ‘70s, Valmet (then KMW, Karlstads Mekaniska Verkstad) was known for delivering standard paper technology, Fourdrinier, and pulp extraction machines. The real breakthrough for higher capacity machines came with the invention of the double-wire machine, where the wire wrapped around a roll to dewater the pulp. This technique revolutionized paper manufacturing and remains in use still today.
Valmet’s innovative spirit led us to test the double-wire technique to wrap a Yankee cylinder with a wire, aiming to improve formation and the drying process. However, as brilliant as it seemed, this resulted in challenges due to low speed and high energy consumption as the Yankee cylinder was constantly cooled down by the water from the headbox. Nevertheless, it provided valuable insights into tissue manufacturing.
From a fortuitous meeting to the first startup
At the 1973 SPCI exhibition in Stockholm, Valmet’s development team met representatives from one of the largest tissue producers in the world. We introduced the technique of using a wire-wrapped roll technology to create pressure for dewatering a paper web. The tissue producer saw potential in this idea and, after spending the following day at the paper pilot machine in Karlstad, became determined that the technique held promise for tissue manufacturing.
This resulted in countless hours of development and collaboration. With the introduction of the Periformer- S, followed by LW for low basis weights, and MW for higher basis weights, we crafted the foundation for modern tissue manufacturing technology, where tissue machines could achieve unprecedented speeds and quality. And in 1974 the first Valmet machine started up in Katrinefors, Mariestad, Sweden.
Verner Höök and Bo Kihlström with their model of a PERIFORMER-MW, scale 1:20, which was displayed at the Valmet stand at the 1978 SPCI exhibition in Stockholm.
Pursuit of perfection with the multi-layer headbox
But why stop here? In the late ‘70s and early ’80 the quest for perfection continued. At that time, tissue producers struggled to achieve high quality in their single-layered products, some of which were made from raw materials derived from recycled newspapers.
The team at Valmet came up with an idea: what if you could have stronger fibers in the middle, softer fibers on the surface, all thanks to air wedges between layers. And with that, the Multi-layer Head Box was born. This innovation wasn't just about making tissue; it was about crafting a product that was both strong and soft, meeting the highest standards of quality. With today’s technology, double-layered products are standard in most countries, and in some even triple-layered.
Adapting to change with strategic acquisitions
The fast growth of the Through Air Drying technology (TAD) in the latter half of the ‘80s posed challenges for the organization. Although significant development resources had been devoted at the pilot machine, we had to accept the reality; we did not manage to become a complete machine supplier on our own.
A small team at Valmet planted a seed that later proved to blossom. If we can't invent it ourselves, why not acquire the best innovations available?
One of the big tissue producers in the U.S. had developed a machine concept with three TAD rolls in succession, where air blew from the inside out. Valmet approached their supplier, Honeycomb Systems from Maine, USA, which operated under great confidentiality to manufacture these large rolls, similar to a honeycomb structure.
Around the same time Brunnschweiler, an Italian supplier of air systems for the paper industry was acquired. Entering Valmet, the development of a modern high temperature drying hood for tissue machines wrapping the Yankee cylinder was initiated. And this is how the Advantage™ AirCap™ was born. Before joining Valmet, Brunnschweiler had started collaborating with an industrial designer not only to meet technical requirements but also to enhance the visual appeal of tissue machines. This was a new approach for the industry.
With these acquisitions Valmet became the sole supplier of complete through air drying machines and the Advantage™ ThruAir® concept was introduced.
Process demand came from customers, and Valmet effectively translated this into machine solutions resulting in significant improvements, leading to better product quality, runnability, and line speed.
Resting on our laurels is not in our nature
Development continued with a new headbox along with a new former for higher capacity. Together with one of the leading U.S. tissue producers we developed a completely new reel that did not have a roll as a counter-pressure during winding but a belt that the jumbo roll rested against. This product, protected by several patents, became a well-established solution, showcasing the power of teamwork and shared vision. The BeltReel was later further developed into today’s Advantage™ SoftReelB.
Making high-performance tissue more accessible
As the market demand for TAD slowed down, we broaden our horizons. How could Valmet reach a new segment of privately owned smaller and mid-sized mills after working primarily with large enterprises for decades?
We decided to develop a dry crepe tissue concept with a new former, new headbox, and new reel and launched, the Advantage™ DCT® technology as a cost-effective concept with the best functionality and performance. The modular DCT concept allows tissue makers to build an optimized machine using standardized, proven solutions that ensure cost efficiency and easy operation. Fast startup curves enable even smaller producers to achieve high-quality results. This innovation set a new standard in the industry, proving that excellence could be achieved without breaking the bank.
Further, Valmet was the first machine supplier to "productize" tissue machines and give them concept names, a practice that was later copied by other machine suppliers.
Valmet's (then Metso) Advantage DCT technology, early 2000. The curved hood, was a result of the industrial designer's wish to make the tissue machine more appealing.
A star is born – Advantage ViscoNip press
Another remarkable chapter in Valmet’s innovative story is the development of the Advantage™ ViscoNip® press. In the beginning of the new millennium, focus increased on reducing both energy consumption and water usage to make processes more efficient and environmentally friendly. What if we could modify the SymBelt press, used for other grades of paper, with a flexible viscous shoe inside the press roll? The invention of the Advantage ViscoNip press improved the pressing profile and increased dryness while significantly reducing energy consumption. It was a game-changer, now sold in over 100 units and used in both new machines and many upgrades of existing machines. Tissue makers report enhanced product quality, increased flexibility and runnability, along with cost reductions, savings from fiber conservation and more stability in the sheet once in the converting line. It is undoubtedly one of the most important components in today’s tissue making process.
Valmet Advantage ViscoNip press
Closing the gap with the hybrid concepts
With machines that could offer conventional tissue at lower cost, to structured tissue at supreme quality we identified a gap in our product portfolio. How could we combine high quality and absorption capacity with energy efficiency and saving fiber costs?
One of the big tissue makers approached Valmet with a request to develop a concept to increase bulk and save fibers. We accepted the challenge and the many trials on Valmet’s pilot machine resulted in the innovation of rush transfer and ten years later reformulated into the Advantage™ QRT® concept – a true milestone for the tissue industry.
From the learnings of this project, we developed the Advantage™ NTT®, which became the first hybrid concept introduced to the market. This concept met demands with softer tissue while using less fibers and reduced energy consumption compared with TAD technology. It has been used primarily for bath and facial production where high quality is needed.
Around the same time, Georgia-Pacific had developed its own hybrid concept, eTAD, over the past ten years on their pilot machine. When GP decided to license eTAD, Valmet saw an opportunity, that historically had been successful, to acknowledge a unique innovation. Today, Valmet markets, manufactures and installs Advantage™ eTAD™ machines for tissue customers outside North America.
Hybrid concepts offer the flexibility to produce a range of high-quality tissue products tailored to market needs, delivering excellent bulk, softness, and water absorption while reducing environmental impact through lower energy consumption. Today, they are used in markets worldwide, from China to the U.S., proving that innovation knows no boundaries.
Commitment to excellence with 50+ years of innovation
For 50+ years, Valmet has always kept production efficiency, tissue quality and environmental sustainability at the heart of tissue manufacturing. A key enabler of this continuous development is the tissue pilot machine, where new ideas are tested—often in close collaboration with our customers. Our story of innovations is one of relentless will of improvements, customer collaboration, and a commitment to excellence. Although we could list all our innovations from the past decades, this article would be far too long. What we can do is to continue our dedication of leading the way in tissue making for at least another 50 years ahead.
2025 marks the year we're celebrating more than 50 years of delivering tissue technology to the world. Through a series of articles, we’ll highlight key milestones, share inspiring personal stories, and, above all, honor the people who have truly made a difference over the decades.
Tissue 50+
Decades of shaping the industry.
We welcome you to explore more industry leading innovations