Machine rebuild in Turkey
Hayat Kimya A.S., part of the Turkey-based Hayat Group, is today the largest tissue manufacturer for Africa, the Middle East and Eastern Europe with a production capacity of 420,000 tons per year. The company first made the decision to enter the tissue business in 2004, and their first tissue machine – TM1 – went into operation in 2006 at a mill in Izmit, Turkey.
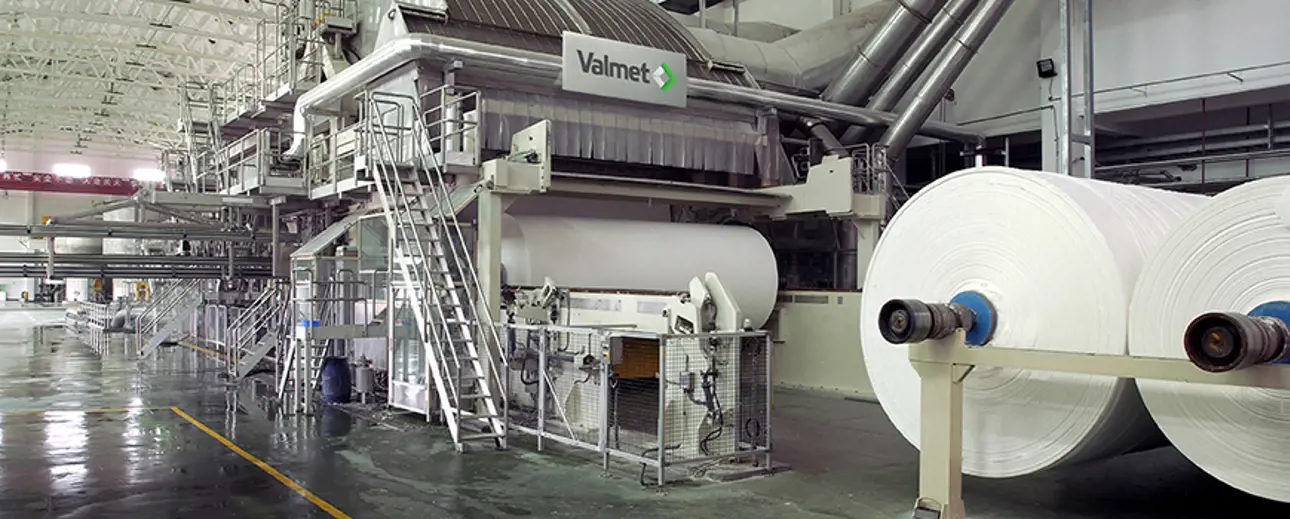
Hayat Kimya’s tissue business has seen rapid growth from the start. The TM1 was quickly followed a second machine, an Advantage DCT supplied by Valmet. That installation, dubbed TM2, was the first of several such tissue lines in Hayat Kimya’s mills in Turkey as well as Iran, Russia, and Egypt.
While the original TM1 operated with high efficiency for nine years, the Izmit mill encountered issues as a result of weak parts related to the hood and press section, as well as a cogeneration system in need of an upgrade. Because of the success Hayat Kimya had experienced with their newer machines, they decided to rebuild TM1 with Advantage DCT technology to match the rest of their tissue lines.
A complex upgrade project
The Hayat TM1 upgrade was a major rebuild project. The work had to be done within a narrow physical space, and there were only five weeks to complete the project. Thorough planning was essential to overcome these challenges. Fortunately, the project engineers were able to work closely with the Hayat Kimya team to ensure the installation was completed on time with successful results.
“A new installation is easy, but a rebuild project is a very big effort,” recalls Kemal Arslan, the Investment and Project Manager at Hayat Kimya. “Planning was difficult as 100 people were involved.”
Hayat Kimya has a systematic method for approaching installations, relying on team members with experience from previous projects. For the TM1 rebuild, they sent Izmit operators to view the TM4 in Russia and the TM5 in Mersin, Turkey. Here, they received first-hand knowledge of the Advantage DCT machines, particularly the nip wet press technology, which would be new to the Izmit mill. As a result, they were already familiar with the system, as well as the mechanical and electrical maintenance needs, once the upgrade was in operation.
“Within two or three days we were running at the same level as before,” says Lüfti Aydin, Global Paper Group Director at Hayat Kimya. “That was a positive surprise, and our team did a very good job together with project engineers.”
A magic device for increased capacity
Problems in the press section had long been an issue with TM1. The Izmit mill tried various improvements over the years, such as installing a steambox to correct the moisture profiles, but issues remained. Having seen the success of ViscoNip technology on other tissue lines, they were convinced it would be a good solution for TM1.
“The ViscoNip press is the new magic for tissue makers, a new standard for tissue machines,” says Kemal Arslan. “We have seen many improvements. It has allowed us to increase the moisture level at the reel, which has given a 1-1.5% production increase.”
Web breaks have also been virtually eliminated since the upgrade, which has in turn increased machine speed. “Before the rebuild our production capacity was eight to nine tons per hour,” adds Lüfti Aydin. “Now we can easily make ten, eleven and sometimes even twelve tons per hour.”
Innovations for improved mill efficiency
Not only has the nip wet press meant greater reliability and thus increased productivity, it has also improved energy efficiency at the Izmit mill. “The flexibility in nip load has made it possible to increase capacity up to 6% with lower energy consumption,” says Kemal Arslan. “Or we can keep the same level of production as before with 16% less energy.”
But the nip wet press is just one of many new features of the rebuilt TM1. The upgrade also included a new cross-directional Yankee hood, which has helped to address mechanical instability that Izmit had with their old hood. Where they previously had big temperature variations on the Yankee surface, the new hood has a helical design with tilted headers for a very even drying profile.
“To compare results, we tried to create the same conditions as we had in the old hood, with the same press load producing the same product,” explains Kemal Arslan. “And we found a 7% increase in hood efficiency.”
Additionally, TM1’s cogeneration system experienced an upgrade, making it possible to generate steam, even when the machine has stopped. “It has raised the exhaust temperature about 20 degrees, which gave two extra tons of steam,” Kemal Arslan notes. “We also save 70 tons of water as we need less fresh water for the boilers.”
A successful partnership
The improvements to TM1 ultimately exceeded the Izmit mill’s expectations, and they continue to be pleased with the results of their close work with Valmet. Today Hayat Kimya mills have six Advantage DCT tissue machines in operation, in addition to the rebuilt TM1.
Article publisher: Björn Magnus
Interview with the Chairman of Hayat Kimya. Read the interview
Hayat moving at world class speed
Category: Experiences
Industry level: Intermediate
Est. read time: 5 minutes
Summary: In this case story, a Turkish mill decided to upgrade their initial tissue machine based on success they had experienced with newer technology in other machines.