From Fiber to Finished Product: Improving Tissue Manufacturing with an End-to-End Approach
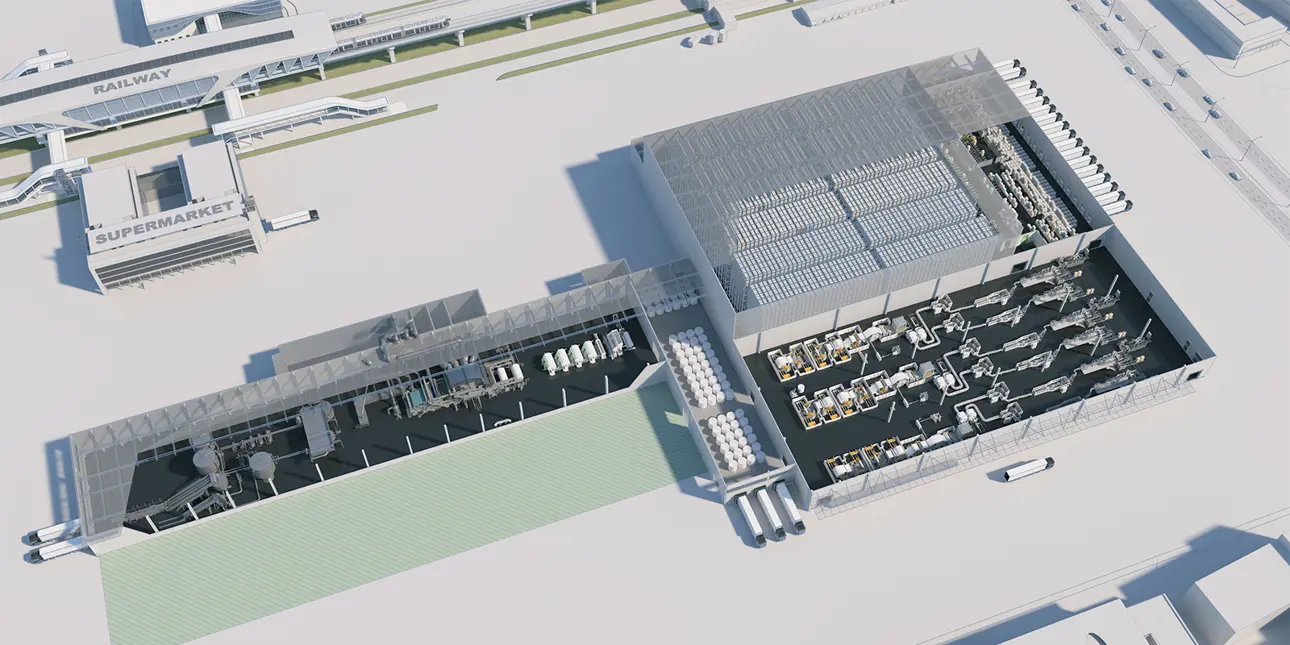
Note: This article first appeared in Tissue360° digital edition, which is a semi-annual TAPPI publication covering the global tissue, toweling, and associated converting industries, with a focus on mill and plant operating floor technologies and applications. Access the complete article here.
Manufacturers across the tissue value chain—from pulp mills to tissue mills to converters—face a unique opportunity. Growing populations and bourgeoning economies are driving global hygiene standards higher, and the tissue industry stands to benefit with an expected CAGR of 3.4 percent from 2022 to 2030.
At the same time, tight labor markets are creating wide knowledge gaps in the industry. Aging, legacy equipment, disparate processes, and a general lack of clarity due to industrywide consolidations and acquisitions add to tissue makers’ challenges. And high energy costs drive up the price of pulp and other materials.
In a global market environment marked by rising costs of energy and raw materials, maintaining efficient production is critical for the tissue industry today. Tissue manufacturing demands more energy use than standard printing paper, mainly due to more intensive drying processes. Optimizing processes across the value chain can reduce energy consumption while also enabling better overall equipment effectiveness (OEE), more consistent quality, and better runnability for tissue-converting processes downstream.
The balance among softness, strength, and sustainability is paramount in tissue manufacturing. Manufacturers must meet exacting specifications with high-volume efficiency to be competitive. From the precise control required in stock preparation to the complexities of pressing, drying, and creping processes, each step is crucial in determining the quality of the final product and the profitability of an operation.
To effectively meet growing demand while maintaining high standards, tissue producers throughout the value chain will need to overcome industry challenges. Many tissue producers are pursuing trends like automation, digitalization, and sustainability as solutions within the tissue industry. Important strategies that can improve tissue production include modernizing production with automation solutions to ease labor pressures, simplifying maintenance and minimizing downtime with digital monitoring technologies, and reducing environmental footprints through renewable energy sources and more efficient equipment. But making these investments takes planning, expertise, and big-picture thinking to be effective.
For the average tissue manufacturer, the task can seem overwhelming. Without standardized processes, clear benchmarking, or the support of an expert partner, operations run the risk of choosing piecemeal solutions that don’t deliver an impactful return on investment. But manufacturers don’t have to navigate these overlapping challenges alone. Working with an original equipment manufacturer (OEM) that takes an end-to-end approach to solutions for the entire tissue-manufacturing value chain can help manufacturers fully capitalize on automation, digitalization, and sustainability to optimize efficiency and scale up production.
Standardizing operations end to end through digitalization and partnership
Whether it’s a large organization that owns the entire tissue-making process, from stock preparation to converting, or a niche operation focused only on refining pulp, standardizing operations is a crucial step to boosting efficiency and productivity. By standardizing how machinery is operated and maintained, companies can significantly reduce variability in their processes, leading to more predictable and consistent output. This consistency is crucial for upholding product quality and meeting customer expectations, while standardized maintenance procedures can minimize down-time from unexpected failures or repairs.
Integrating digital technology and machine monitoring solutions to collect data and standardize KPIs can help optimize efficiency in existing operations and uncover new opportunities. With instrumentation for quality control, sensors for condition monitoring, and modern machine and process control systems, tissue manufacturers can quickly identify areas for improvement, adjust processes in real time, and ultimately enhance overall efficiency. Digital tools can also speed up training and competence development and respond to turnover and onboarding challenges.
Although there is a wide range of digital solutions providers for tracking manufacturing performance, collaborating with an OEM partner who is ingrained in the entire tissuemaking process can significantly bolster these efforts. An OEM with deep industry knowledge can support tissue manufacturers by benchmarking KPIs against those of other machines used across the industry, identifying best practices and ways to enhance performance.
When making investments in new machinery or new production lines, partnering with an OEM who has solutions and expertise for every part of the process can help close production gaps to create a more cohesive system. Some tissue-manufacturing OEMs provide end-to-end support, helping with everything from planning and piloting to deployment and maintenance support. They can offer guidance on selecting the right equipment to fit into a standardized framework, ensuring that new machinery integrates seamlessly with existing operations and contributes to the overarching goal of operational efficiency and reliability. And working with a single-supplier OEM to standardize equipment across operations can help simplify maintenance, streamline spare parts inventory, and ensure compatibility across systems, further optimizing production.
Optimizing efficiency and equipping production for a smaller environmental footprint
With standardized processes, mills can achieve a higher level of automation to improve efficiency. Automation can play a crucial role in reducing waste and optimizing production processes, ensuring that equipment operates only when necessary and at optimal efficiency levels. Advanced process controls measure machine parameters and automatically adjust settings during production. During the drying process, this technology can keep the air balance in the hood at an optimum level to significantly reduce energy consumption.
Modernizing outdated equipment is another way operations can meaningfully improve their use of resources and reduce carbon emissions throughout the entire process. Energy recovery solutions can help refiners reduce consumption in the forming section during stock preparation. While in pressing and drying operations, advanced pressing technologies can increase the press load without jeopardizing the paper quality, while at the same time significantly reducing the energy demand of drying processes and improving the runnability for converters. Fiber savings can also be gained through different types of clothing, in combination with adaptable pressing elements.
There are also a variety of services available to optimize existing machinery. Process experts can conduct on-site audits and studies in the woodyard, on the fiber line, and throughout the liquor cycle to identify opportunities to improve efficiency. Field service experts can also help with everything from troubleshooting to regular planned maintenance to spare parts planning, further optimizing equipment and processes on-site or remotely from performance centers.
Working with an expert OEM that can offer sustainable solutions for the entire process can help manufacturers make big leaps toward their sustainability goals. Through their expertise and experience, expert OEMs can guide companies in identifying and implementing strategies to reduce waste throughout the production process. Some OEMs can even offer engineering services to lower water usage by custom-designing production lines based on the available water resources. By partnering with these OEMs, manufacturers can take advantage of services for evaluating fiber mix and receive advice on solutions and best practices to reduce their carbon footprint.
The collaboration between tissue manufacturers and experienced OEMs can drive substantial improvements in both energy efficiency and environmental sustainability. These efforts not only contribute to the global push for environmental responsibility, but can also position a manufacturer as a sustainability leader within the industry, potentially offering a competitive edge in a market that values eco-friendly practices.
![]() |
VP, Head of Valmet Tissue Converting Business Unit. |
Related articles