Valmet’s Advantage ViscoNip Press at Kimberly-Clark results in high-capacity production
Running a tissue machine at high speed, efficiency and capacity is a challenge for most tissue producers. Kimberly-Clark Bajío team has managed to go from learning how to operate the first Advantage ViscoNip press in Mexico to running their Advantage DCT200 line at world record speed day in and day out. How did they do it and what does it take?
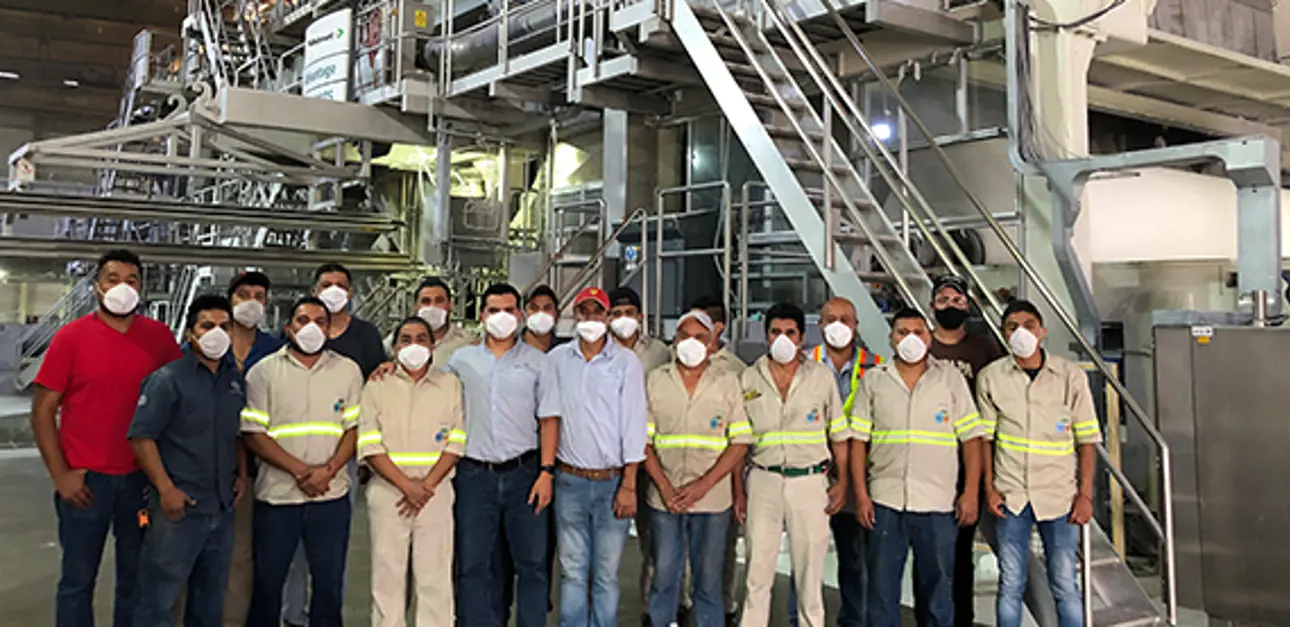
Increasing capacity step by step
When trying to do something that has not been done before it was of most importance for the team to address each challenge step by step. Being unaware of how the machine would react, reaching the desired point of capacity was performed gradually over a 15-day period. During the first week speed was slowly increased little by little from 2,000 m/min to 2,010, 2,050 and the second week up to 2,100 m/min making sure everything was running smoothly. At that time the team at Bajío felt confident enough to increase the speed even further to 2,200 m/min. Even though operation was good they wanted to make some adjustments to maximize the efficiency even further.
First aiming for a lower basis weight of 14 grams per square meter was successfully conducted. Further using 100% recycled fiber was also possible. At this point the only real problem was that they had to adjust the tail turn up to maintain good turnovers. After some work they were also successful in maintaining the machine efficiency at around 89% - a great achievement for the team.
Teamwork is the key to everything
As most experienced tissue makers know, running a machine at this speed is not easy. We asked Alberto Rodriquez, Superintendent of Production Machines 3 and 4 and Juan Carlos Sandoval, Maintenance Manager at the Bajio mill about the secret behind their success.
“The secret starts with the whole team” Alberto begins. “Transparency and educating the team members, making sure everyone is aware of the purpose; where we are going and what we want to achieve. But also an understanding of the potential loss of time during every change of roll is significant. Everything needs to be done correctly”.
As previously mentioned, the mill in Bajio was the first in Mexico investing in the Advantage ViscoNip press. When comparing their conventional machine having a suction press roll, with this machine having the ViscoNip press the result speaks for itself. Alberto continues “the profile of this roll is much different from the suction press roll, very flat with no issues”.
Energy vs. speed
One major reason to invest in the ViscoNip press was to lower the consumption of energy. Today the results support that investment. Because when comparing to the other machines at the mill it does consume less energy. The difference compared to the other machines producing the same quality is 15% less energy total with a 35% reduction in gas consumption. Of course, a lot of finetuning was required during the 3-week period when the increase of speed was performed.
As the mill also produces towels the machine must alternate between 2200 m/min and 1650 m/min as the production of towels are more demanding from a drying point of view. This is being done with no complications. When the machine decreases or accelerates the speed because of alternating between towel and bath production, the team is documenting and closely monitoring the energy consumption in order to follow the possible best practice example. Overall, Alberto Rodriquez and his team are very pleased with the result achieved so far.
When operating at such as high speed it is natural to believe that maintenance must be performed more often. We were quite surprised when Alberto explains their findings. Both felt and belt have actually lasted longer since the increase of production speed. Felt life increased from 38 to 45 days on average and the belt life is about 8 months. Juan Carlos is also mentioning how well the components of the machine are performing.
The journey continues
We are pleased to hear about the great results from Alberto and Juan Carlos at the Bajio mill. For us at Valmet focus is always the performance of the machine and making sure production is running according to expectations. But as we are always looking to improve and cater to the market demands we are of course interested in hearing more about the Mexican consumer trends. According to Alberto softer products are becoming more appealing. Further as KC Bajío is today producing with 100% secondary fiber, they can meet the expectation of more and more sough-after sustainable products.
As we understand by the investments done in the ViscoNip press and the goal of energy savings, sustainability is an important topic for the company. By using renewable fiber each product has a second life as they explain it. Simultaneously many more initiatives are being made every single day such as reduction of fresh water and forest conservation.
Currently the machine is running at an impressive speed of 2200 m/min in continuous operation without any complications. Since the installation the production has increased from 160 to 170 tons per day. Looking at the future the plan is to aim even higher. Increasing the efficiency from 85% to 90% is a good number and the goal is to maintain the speed. It is a big challenge to lower the basis weight, which in combination with high speed is difficult to achieve. Albert and Juan Carlos are hopeful for the future, and despite being quite nervous when they initially made the transition into such high speed, they are now confident in the performance of the machine as it has proven to be very stable.
For more information contact Jan L. Larsson, Director of Sales North America
Related articles