Supplier sustainability audits advancing sustainable business practices
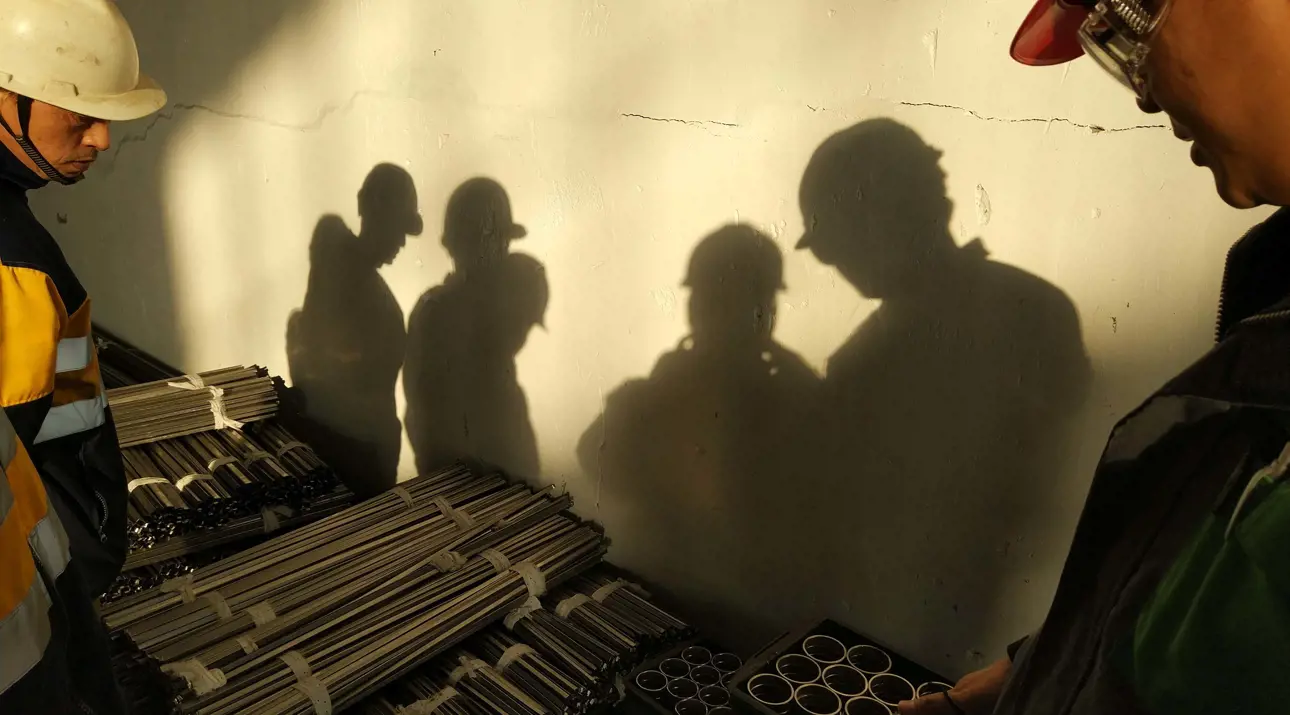
Valmet’s sustainable supply chain program was established in 2014, and China was the first country in which it was implemented. Supplier sustainability audits began the following year, and excellent progress has been made since. As a result, a number of constructive and creative solutions have been reached where room for improvement was found.
Valmet China has now performed over 50 sustainability audits among its key suppliers. Audits concentrate on the five areas of Valmet’s sustainable supply chain policy: business ethics, compliance, human and labor rights, health & safety, and environmental management.
The backbone of our sustainable supply chain program has been strong management support and ownership, with internal process owners spending a great deal of time and effort to find the correct ways of working within procurement teams. Internal trainings on the topic were also held in several Chinese locations, including Shanghai, Wuxi and X´ian. These accumulated efforts have really paid off, with suppliers proceeding well according to commonly agreed corrective action plans.
Auditing in practice
A good example was the case of one of our Chinese suppliers, where the majority of audit findings concerned health and safety. For instance, our auditors identified a high platform without a safety fence where workers were exposed to an obvious risk of falling. After the audit, in its corrective action plan, the supplier proposed action in the form of a ladder and handrails around the platform, and implementation started to move on and soon these corrective measures were verified.
In the case of another supplier, the pickling process of stainless steel products required attention. To ensure the process met environmental requirements, the supplier partly acquired a chemical treatment company to manage this process step. However, majority of corrective actions are related to process changes and small scale investments e.g. in safety gear.
"Even though the number of audited companies is relatively high in China, it does not cover all our suppliers," says Juha Rajala, Valmet’s Senior Manager of Supplier Quality Management. "That’s why in Valmet China’s supplier quality management, we have started to integrate sustainability to our existing quality assurance processes. In practice this means we have started to collect not only quality-related findings from suppliers during our visits, but also sustainability-related findings, and using the same tools."
"Suppliers are an integral part of our manufacturing and delivery processes," adds David Sun, Director of China Supply Chain at Valmet. "It is our responsibility to reduce negative environment and social impacts throughout our value chain. I am happy to see that we are successfully integrating sustainability into our way of operating in procurement, and at an excellent pace."
Other examples of improvements made as a result of such audits have included our suppliers:
- Establishing a business ethics policy and communicating it to employees
- Setting up a system to identify, evaluate and comply with local laws concerning labor rights, health and safety, and the environment
- Providing employees with annual leave and social insurance
- Taking safety measures such as supplying helmets
- Making contracts with licensed bodies for the collection and treatment of chemicals
Improving the auditing process
The supplier sustainability auditing process itself has also been developed since its implementation, with improvements and best practices being shared between different areas of the company.
"I am very proud of our team of auditors," says Laura Puustjärvi, Valmet’s Head of Sustainability. "What they have achieved represents a huge progress for the entire company. To assess whether global processes are followed everywhere, we have held training sessions across our geographical areas, in which we walked through auditing processes and pointed out any necessary improvements."
Puustjärvi explains that feedback on these best practice-sharing sessions has been very positive. They are seen to have been highly beneficial for the improvement of Valmet’s own processes, helping the company to achieve even better improvement results from its suppliers in future.