Beyond Circularity: Innovative results from ecosystem projects
We have started the fourth and final year of our Beyond Circularity R&D program and ecosystem. During the last three years, the program has made significant progress and has already surpassed many of its original goals. We originally aimed to have 115 partners, but by the end of 2024, more than 290 ecosystem partners were collaborating with us on 37 joint projects. The program has also provided a substantial boost to Valmet’s R&D efforts internally, and around 400 R&D professionals at Valmet have been actively involved.
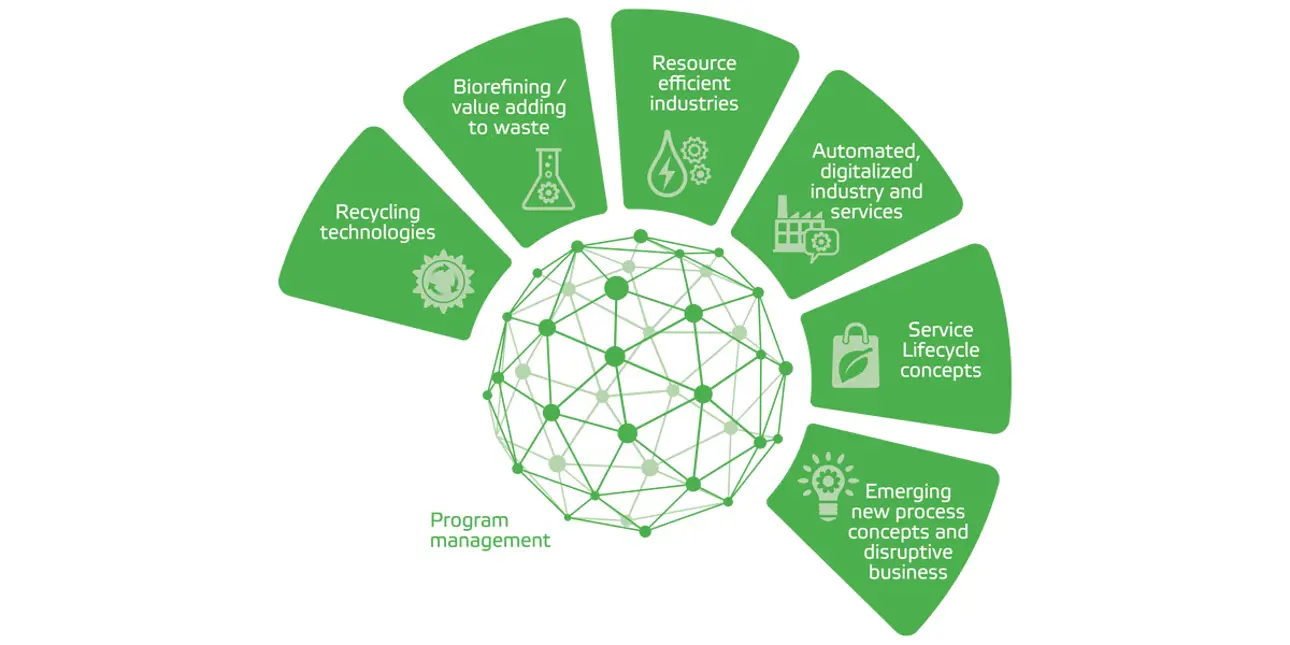
The program is partly funded by Business Finland and is part of the “Veturi” initiative.
During 2024, the Beyond Circularity program gained excellent speed and momentum, with the first launches emerging from the program.
"The launches are also great examples of the program’s contribution to Valmet’s overall sustainability targets, including reducing CO2 emissions and promoting circular economy principles. We’re also continuing the extensive R&D work this year, but the focus is gradually shifting to accelerating the commercialization of the innovative solutions developed within the program, ensuring that they’re market-ready and can be produced on an industrial scale,” says Marke Kallio, Director, R&D Programs at Valmet.
The Beyond Circularity program is partly funded by Business Finland and is part of the “Veturi” initiative.
Promising results from ecosystem projects
The Beyond Circularity program has demonstrated how collaborative efforts can drive innovation and the circular economy, helping partners and participating companies be part of the green transition – not just for environmental reasons but also for improved competitiveness,
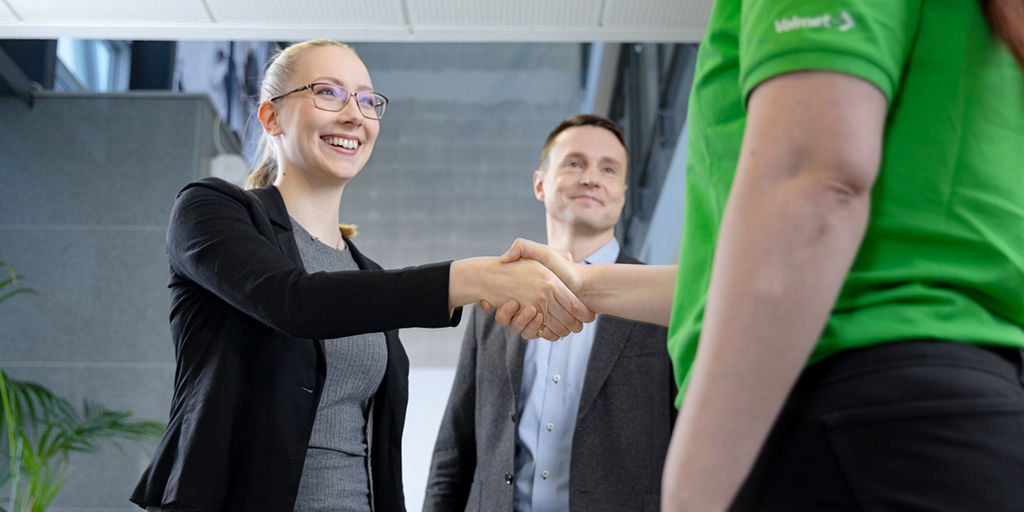
Four ecosystem projects were completed in 2024, with promising results.
SUSTAFIT – Sustainable fit-for-purpose nonwovens
The nonwovens industry faces growing global sustainability challenges that require a rapid transition to a circular economy. In the SUSTAFIT project, Tampere University of Applied Sciences (TAMK), VTT, and Aalto University innovated more sustainable nonwoven solutions and researched the topic with 17 companies, including Valmet. The project explored the sustainability of nonwovens from different perspectives to improve raw materials, processing methods, recyclability, and business models.
A tangible result of the project was the Sustainable nonwovens of the future – From research into business opportunities workbook. It is designed to give insights into how to make products in the nonwovens industry more sustainable in the future.
The SUSTAFIT project was very successful from Valmet’s perspective, resulting in significant new contacts with research institutions and industry companies. New nonwoven fabric structures were developed in the SUSTAFIT project using various techniques, which also supported the development of Valmet Automation’s measurement technologies for applications in the nonwovens industry.
Read about the results on the release by Tampere University of Applied Sciences.
High Performance Cellulose-based Composites (HiPer)
In this project, Valmet collaborated with nine other Finnish companies and the VTT Technical Research Centre of Finland to study the use of biocomposites on an industrial scale. The project team successfully demonstrated the manufacturing of thermoplastic composites on a pilot paper machine. They used foam forming technology, originally developed for the paper industry, to produce pulp-based biocomposites. This novel technology enables high production volumes, energy-efficient production, and increased flexibility with new raw materials.
“At Valmet, we have solid paper machine and process technology expertise. The HiPer project allowed us to investigate new products with partners which could be made with paper machines. Even though the ecosystem project is now complete, we’re continuing work at Valmet. The project provides us with a solid foundation for more detailed machine concept design,” says Mervi Kuoppamäki, Development Manager, R&D, and Valmet’s representative in the project.
The project presented two new HiPer material demos to showcase the versatility and potential of HiPer biocomposite materials: the HiPer Suitcase, made entirely from HiPer biocomposite material, and the Tutto Active chair by ISKU, crafted from a cellulose-plastic compound that uses natural annual fibers, polypropylene, and wood pulp from Finnish forests as raw materials.
Photo: VTT, Niina Hyry, 2023
Read more about the project and its results: Beyond Circularity: Manufacturing industrial-scale biocomposites
UrbanMill - Chemical recycling for plastics
Mechanical recycling alone cannot meet the plastics recycling targets set in the EU and national legislation. Chemical recycling offers another important route for recycling plastics. The UrbanMill project aimed to develop next-generation pyrolysis-based chemical recycling to produce equivalent-to-new quality recycled plastics from mixed plastic waste and to increase plastic recycling rates. The work plan consisted of extensive experimental research from laboratory to pilot scale, supported by techno-economic and environmental impact assessments for the process concept.
The project was led by VTT Technical Research Centre of Finland in partnership with Aalto University. The partner companies covered the whole value chain of the chemical recycling of plastics in Finland.
The project increased pyrolysis-based recycling knowledge and R&I capabilities. Its results also showed that polyolefin-rich mixed plastic waste containing polystyrene, polyamide, and PET could be recycled using fast pyrolysis. The process concept assessment demonstrates economic viability and indicates the critical steps needed to improve the overall yield and CO2 footprint. Furthermore, specific required analytical methods were developed during the project that will pave the way for future research initiatives.
Antti Raiko, Valmet’s project manager for plastic chemical recycling in the Valmet Beyond Circularity program, says: “The UrbanMill project has increased our knowledge and competencies in plastic chemical recycling and thus accelerated our own Pyrolyzer development. I’m keen to see fluidized bed pyrolysis technology being commercialized in the near future.”
It is planned that the UrbanMill work will continue in the UrbanFactory project, with the main target to notably increase pyrolysis product yields and further increase the TRL level of the concept based on fluidized-bed pyrolysis technology. This will boost plastics waste recycling, reduce incineration, and make significant contributions to reducing CO2 emissions across the plastics industry value chain.
Read more about the results in VTT’s article.
SEEDForest Coach
Valmet worked with VTT Technical Research Centre of Finland, other research partners, and companies in the SEEDForest COACH project to create steps towards the human-centered, technologically enabled intelligent industrial work of the future.
“Valmet’s focus was on discovering how we could support our employees, partners, and customers in adopting new working and planning modes. We’ve been working with user experience and human interaction with different systems since the 1970s. Every innovation should stem from actual user needs and make their work easier. When new concepts support users in their work, they become easier to adopt,” Valmet’s UX Manager Nina Flink says.