Beyond Circularity: Collaborative R&D for automated and digitalized industry
In 2022, Valmet launched the Beyond Circularity R&D program and ecosystem with the aim of transforming waste and emissions into valuable resources for sustainable growth. The program is being implemented in seven streams. Now it’s time to dive into stream 5: Automated digitalized industry and services.
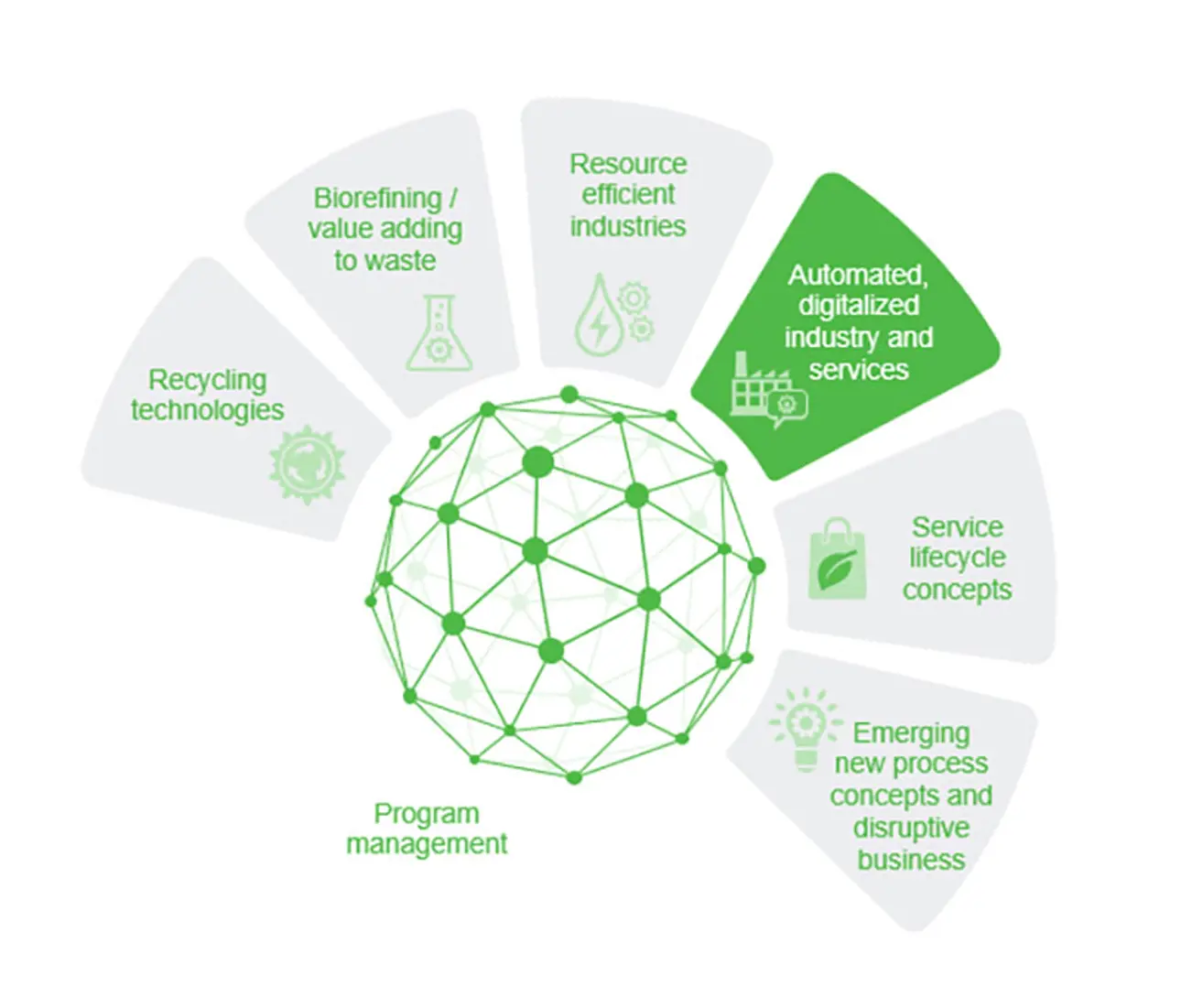
Let’s ask Jukka Ylijoki, who leads this stream, for more information. Jukka has a long career in research and development, currently heading R&D in Valmet’s Automation Systems business line.
Why was “Automated digitalized industry and services” selected as one of the Beyond Circularity streams?
Valmet is innovating and developing many new processes and solutions to enhance our customers’ green transition in the Beyond Circularity program. These processes and solutions need automation and digitalization to harness all the benefits, so it was natural to include these topics in the program.
We combined all automation- and digitalization-related Beyond Circularity R&D projects into this stream. As our stream supports other streams, close collaboration is critical. We must listen carefully to the needs from other streams, and based on them, we can investigate if we have existing solutions we can use or develop new ones if we don’t.
However, our stream isn’t limited to the Beyond Circularity program; we are also looking more widely for new business opportunities.

Jukka Ylijoki shared the latest updates from Automated digitalized industry and services stream in the Beyond Circularity ecosystem event.
What are stream’s targets and topics?
We are working with these main topics:
- Measurements for new processes
- Digital platform
- Environmental services.
We aim to enable major leaps toward autonomous mills and even safer processes, create a thriving network with partners to develop energy-saving and emission-reducing services, and innovate novel process measurements for an insight into the new processes developed within Beyond Circularity.
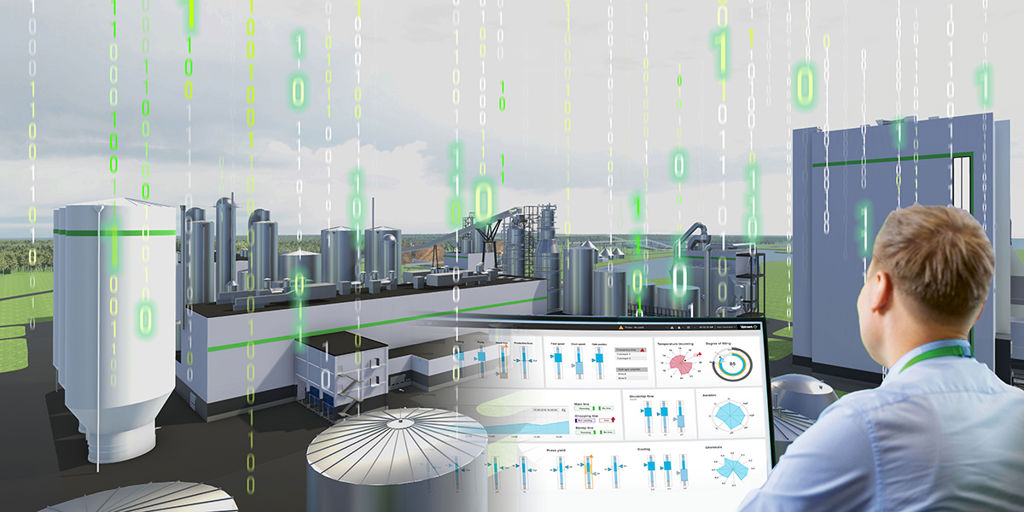
Fruitful collaboration with ecosystem partners
We are working on five co-innovation and three co-research projects with our ecosystem partners.
Co-innovation projects:
- BETTER – Beyond traditional roll service
- Biond4.0 – Data-driven control for bioprocesses
- CTAC 2.0 – Cybersecurity assurance
- USWA – Ultra scalable wireless access
- Virtual sea trial – Ensuring that a single shortened sea trial is sufficient to pass in future ship commissions.
Co-research projects:
- CEBIPRO – New analysis technologies for circular economy biorefineries.
- SEEDForest COACH creates steps toward the human-focused, technologically enabled intelligent industrial work of the future.
- Hydrogen UnderGround (HUG) focuses on the underground storage of hydrogen.
Read more about some exciting ecosystem projects
HUG - Developing hydrogen underground storage
Valmet is joining forces with VTT Technical Research Centre of Finland, Geological Survey of Finland (GTK), and 15 industrial partners in a pioneering research project called Hydrogen UnderGround (HUG).
Hydrogen underground storage is widely seen as playing a critical role in the green hydrogen value chain in balancing the production of and demand for hydrogen. Storing hydrogen above ground is impractical for cost and safety reasons. Preliminary reviews confirm underground storage is the safest affordable large-scale option.
With more than 50 years’ experience in serving the hydrogen industry, Valmet brings valuable technology knowledge to the project. The company’s portfolio covers both valve and automation solutions for the hydrogen industry.
Read more about this co-research project.
SEEDForest COACH - Exploring tomorrow’s intelligent industrial work
Working with VTT Technical Research Centre of Finland and other research partners, Valmet is participating in SEEDForest’s COACH project, which aims to take steps toward the human-centered, technologically enabled intelligent industrial work of the future. SEEDForest is a collaborative project platform that brings together the forest and chemical, process technology, automation, engineering, service companies, and IT industries. It aims to develop Finnish industrial capability toward a twin transformation: a more sustainable future through smart digitalization.
“Valmet’s focus is on identifying how we can support our staff, partners, and customers to adopt new ways of working and planning. We’ve been working with user experience and human interaction with different systems since the 1970s. Every innovation should stem from users’ actual needs and make their work easier. When new concepts support users in their work, they become easier to adopt,” says Valmet’s UX Manager, Nina Flink.
One of SEEDForest COACH’s case studies features Valmet’s Performance Center service, which provides Valmet’s customers with remote services and support. Broad international user interviews have been conducted to discover what new requirements, educational needs, and tools the ongoing industrial shift will entail for process experts.
Wrapping up in late 2024, SEEDForest COACH will offer tangible suggestions for the project findings’ application in practice and what kind of further research is required.
Read more about this co-research project.
Virtual Sea Trial - a shared, distributed test environment for simulated system integration testing
As modern ship designs become more complex due to stricter energy efficiency requirements and higher levels of autonomy, early simulation-aided testing is increasingly needed. The Virtual Sea Trial project aims to create a shared, distributed test environment for simulated system integration testing.
The main development topics are commissioning interfaces​, benefits realization, and test-driven design and commissioning.
“Valmet expects to achieve more automated testing with Digital Twin(s), which can be connected to simulate actual process/machinery. One promising result is an implementation that can use the OPC UA Server with Functional Mockup Interface (FMI) -based simulation models. This enables the use of FMU files and simulations. Simulation inputs/outputs can be connected to Valmet DNAe. This increases automation quality, allowing a quicker and easier start-up. The vision is to use Digital Twins more widely as a part of automated mills,” Mika Karaila, Research Director, Automation Systems business line, Valmet.
Read more about this co-innovation project on the project’s home page.