When even the smallest details count – Valmet Refiner Segments contribute to the smooth operation of Klabin’s PM27
Jun 26, 2024
Having delivered numerous technologies to Klabin’s multi-billion investment Puma II project, the inauguration of the new kraftliner machine PM27 was eagerly waited for within Valmet. After the successful startup in August 2021, also the refiner segment team was celebrating – the refiners were operating very well and contributing to the overall performance of the entire production line.
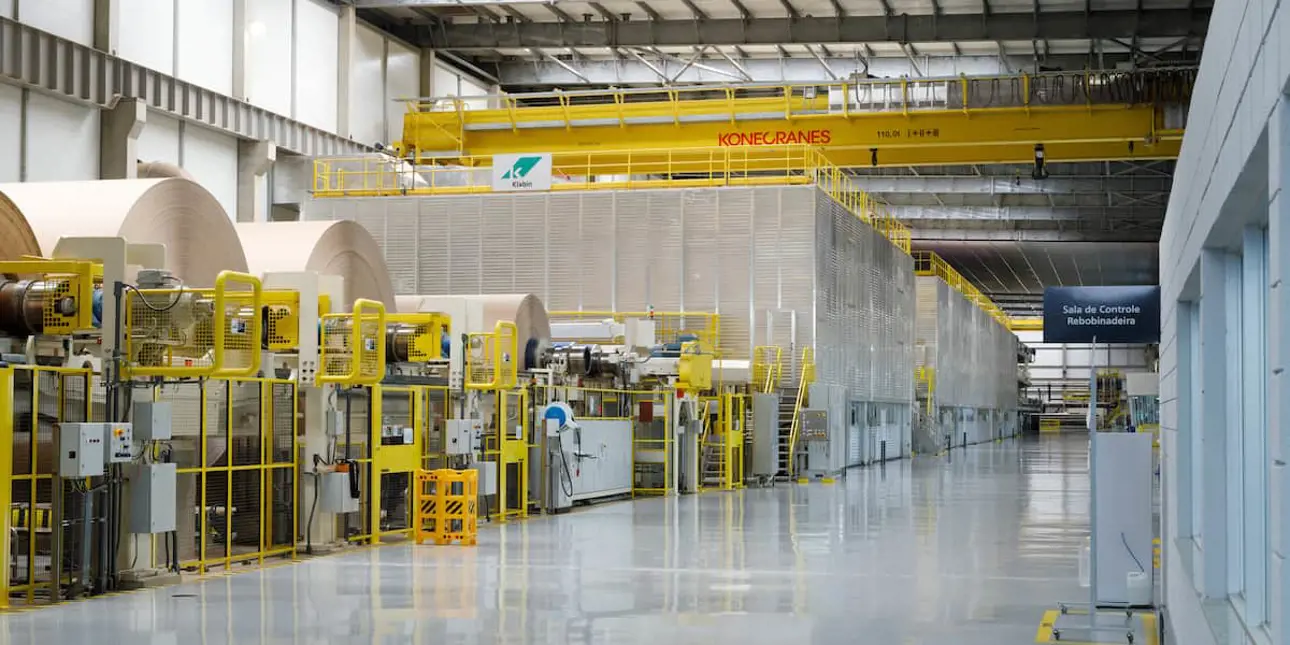
In the first phase of Klabin SA’s Puma II project, Valmet’s delivery included, among other technologies, a complete cooking plant and a fiber line with a capacity of 2000 ADt per day. They were to feed the new kraftliner machine PM27 at Klabin’s mill located in Ortigueira, Paraná state in Brazil.
“Thanks to the good co-operation with Klabin at their nearby Monte Alegre mill, we were able to offer a refiner solution that the customer was already confident with. The overall solution was specially designed to meet the conditions of the new production line and the customer’s performance targets,” says Jan Laredius, Senior Product Manager at Valmet.
For the fiberline, Valmet’s solution included a scrap separator for removing stones, metals and other impurities from pulp before it enters the refiners, first of its kind in blowline application EVO 46 K with a unique centerplate design, and a RGP 262 A deshive refiner. In addition, Valmet delivered a startup package of refiner segments with two sets of spares.
Stable performance during the startup
Starting up a greenfield mill is always quite a challenge – it can take several months before the production reaches the expected capacity and quality.
“Often during a startup there are certain variations in the process that affect the pulp flow and consistency. In this case, the refiners and the refiner segments handled the variations better than expected, leading to good fiber quality and availability of the refiners throughout the startup,” says José Rinaldo Ribeiro Junior, Fibers and Pulp Manager at Klabin.
“In these applications, refiners need to have high availability. For that, we need segments that are easy to operate and forgiving, which we managed to find right away,” says Karl Lönngren, Global Product Manager for Fiber Process Parts at Valmet.
Good performance leads to improved quality
In order for Klabin to take over the operations, Valmet needs to reach the guaranteed targets for production rate and pulp quality.
Today, we are operating without the reject refiner, and still have a very low shive level on final pulp, meaning that the deshive refiner segments’ performance is excellent,” Junior says.
“The main target of the chemical pulping refiner applications is to reduce shives while keeping fiber properties. I was very happy to see that the quality targets were met instantly,” Lönngren adds.
The lifetime of the refiner segments was a positive surprise
Prior to the startup of PM27 in Ortigueira, Klabin had experience of Valmet’s refiner segments from the Monte Alegre mill.
“We were used to replacing the refiner segments after approximately 2300 hours. It was a huge surprise to us when we reached 4000 hours and could go for more,” says Junior.
“In addition to their top-notch pulp quality, the lifetime of the refiner segments is dependent on the entire refiner solution. In Ortigueira, I believe we succeeded in the overall process design, starting from the scrap separator to the blowline refiners with the unique centerplate design. Together these solutions improve the purity of the pulp, contributing to the lifetime of the refiner segments as well,” Lönngren explains.
Photos: Klabin Puma 2
Text: Karl Lönngren & Mateus Argenton do Amaral
Related pages
Related articles