Valmet’s environmental savings: A success story from the Columbus Service Center upgrades
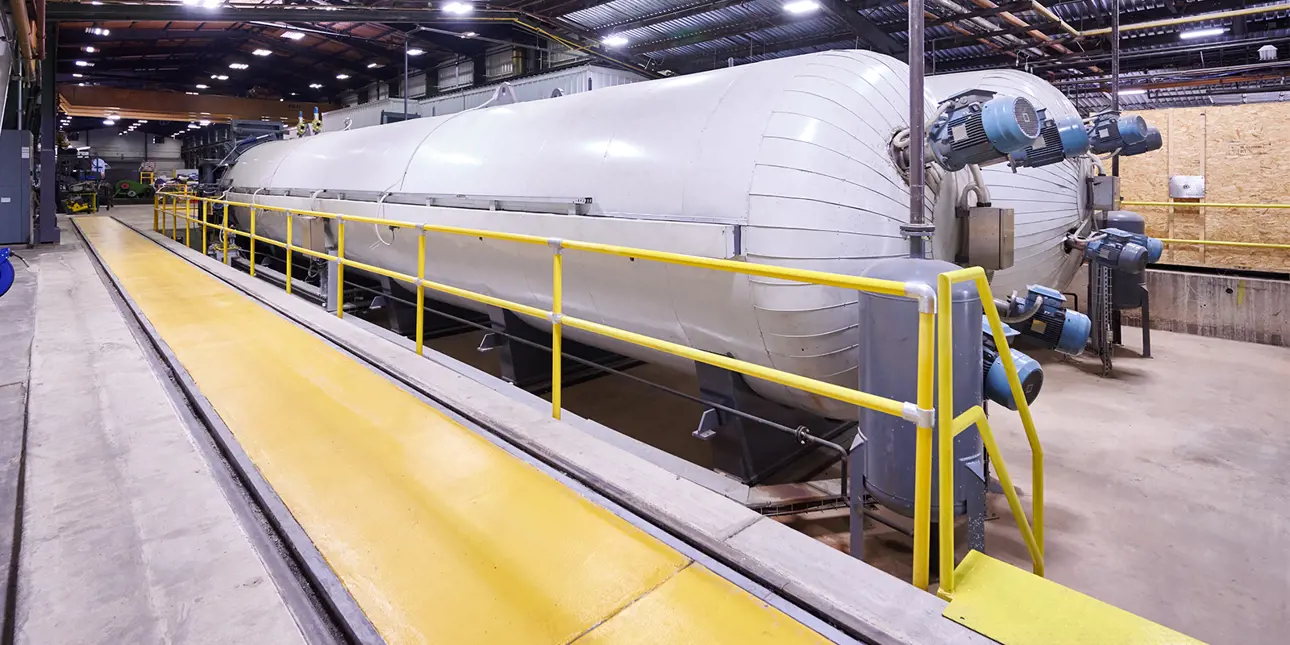
As previously announced at the end of 2023, Valmet invested significantly in upgrading the company’s roll cover production in Columbus, Mississippi including the vulcanizer upgrades. The project has now been successfully completed, resulting in substantial environmental savings and operational improvements.
The project aimed to enhance operational efficiency, reduce environmental impact, and improve overall performance. Check out the details below from this transformation and the positive outcomes it has yielded.
Background
The existing equipment faced several challenges:
- Polyurethane Machine: Purchased in the early 2000s, this machine was designed for a specific cover type and had served well for 15 years.
- Composite Wrap Machine: Manufactured by Beloit Manhattan in the early 1980s, it had seen minimal updates over the decades.
- Autoclaves: These water-cure operated autoclaves, dating back to the 1940s, consumed substantial energy during the curing process.
- Dry Steam Ovens: Used for Poly/Composite, these ovens relied on steam radiators but were prone to leaks and maintenance issues.
The Investment
Valmet invested significantly in upgrading the vulcanizer. The project took several years to complete, and the results are now evident.
Positive Impact
- Quality: The upgraded equipment ensures consistent and high-quality cover production.
- Safety: By separating the cover process from the normal work environment, Valmet has improved safety conditions for its employees.
- Productivity: Reduced cycle time for poly covers (single-pass process) has increased monthly production units.
- Market Share: Valmet’s enhanced capabilities position it competitively in the market.
- Sustainability: The project significantly contributes to environmental sustainability.
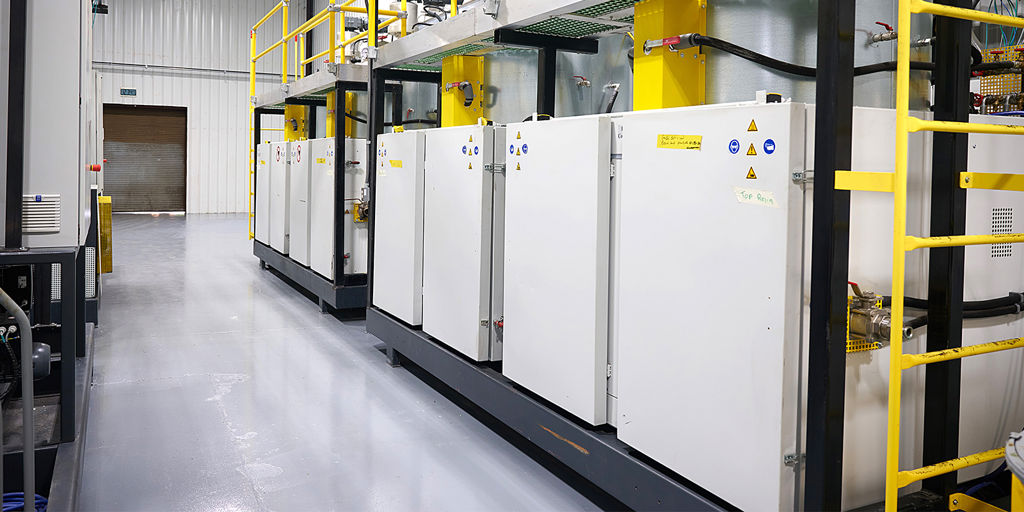
Environmental Savings
The environmental impact of the investment is substantial.
- Electric Autoclaves: Valmet transitioned from water-cure autoclaves to electric ones, resulting in a 95% reduction in location water usage and a 20% reduction in natural gas consumption.
- Gas Boilers: By shutting down and removing gas boilers, Valmet curtailed emissions and improved its carbon footprint.
- Nozzle Application: Moving from dipping to nozzle application minimized resin and curative waste.
- Improved Washroom: The relocated washroom now features better containment and filtration, further reducing water usage during roll cleaning.
Valmet’s dedication to environmental sustainability, operational excellence, and safety has yielded significant benefits. The Columbus covering upgrades exemplify how strategic investments in operations can achieve financial gains while promoting a greener future,” says Jonathan Demers, Director, Roll Services, North America, Valmet
Valmet’s commitment to environmental sustainability, operational excellence, and safety has resulted in tangible benefits. The Columbus vulcanizer upgrades showcase how investing in operations can lead to both financial gains and a greener future.