SsangYong C&B optimizes tissue press nip efficiency
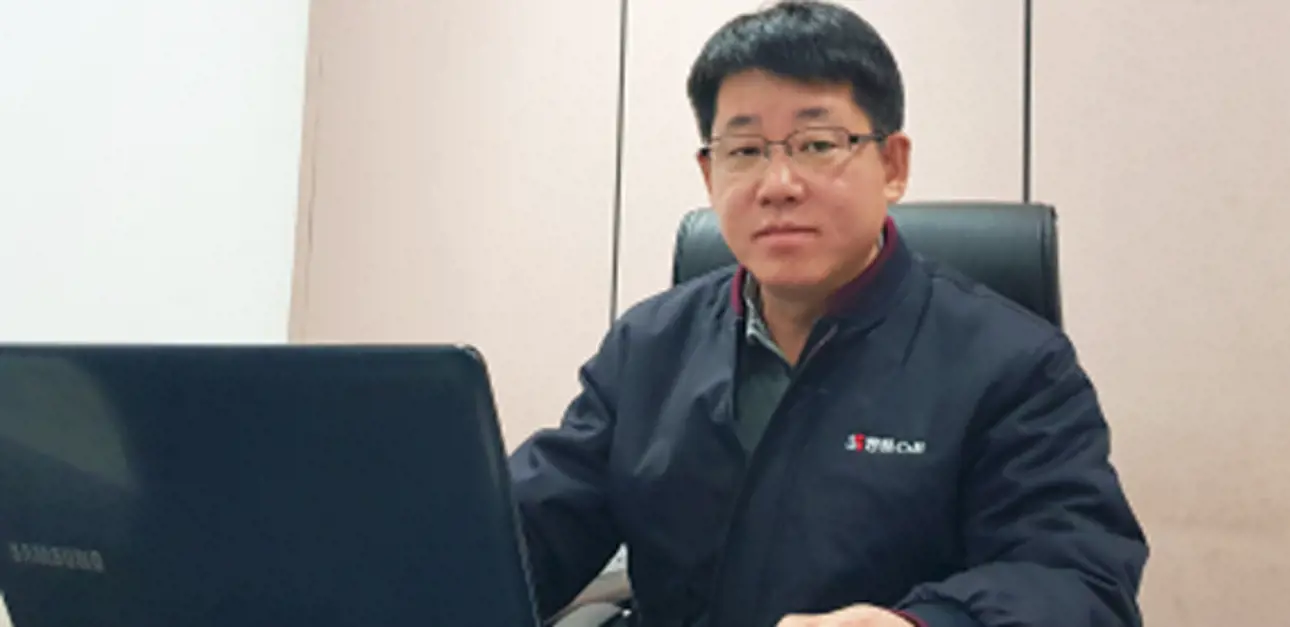
A press roll cover upgrade and iRoll technology, used for nip profile optimization, enabled SsangYong C&B to improve tissue dryness and felt profiles, save energy, and increase tissue machine speed.
In line with its slogan “Clean and Best,” SsangYong C&B emphasizes getting the best achievable performance and quality at all times. The company is one of South Korea’s biggest tissue producers and converters.
Located in the city of Sejong, Jochiwon TM 4 produces consumer bath tissue in the 14–22 g/m2 range. TM 4 has a wire width of 4,700 mm, two roll nips and a production capacity of 100 tonnes a day.
To optimize press nip efficiency for TM 4, SsangYong turned to Valmet. The main targets were to improve energy efficiency by lowering steam consumption through higher post-press dryness, and to get more uniform moisture profiles by improving dryness profiles. Moreover, the mill wanted to extend roll cover and felt lifetimes, which requires optimal performance of the press loading equipment.
Achieving all these targets would allow SsangYong to run the machine at a higher speed, too.
The results from cooperation with Valmet has been satisfying in energy savings and machine speed increase. We are looking forward to continue the development further in order to improve the energy and production efficiency even further and to get more cost savings.”
Mr. Jong-Dae Byun, Director & Mill Manager
Harder press roll covers and a new grooving pattern
To find ways for improving press performance, Valmet analyzed the conditions that the roll covers were experiencing in the press section. Removing more water from the web generally requires a higher nip pressure. The cover material was changed from rubber to a harder polyurethane cover to enable higher load levels and extend the cover lifetime. Additionally, the grooving pattern of the cover was changed to enable efficient water removal.
The choice of cover stemmed from simulations run with Valmet’s PressSim and NipSim software. These tools make it possible to find the best combination of cover material, hardness and surface topography to maximize dewatering. The suction press roll was equipped with Valmet Press Roll Cover PF-V with a hardness of 15 P&J, with Valmet Press Roll Cover PH chosen for the second press roll, with the same hardness.
500th profile analysis with Valmet iRoll
In order to improve moisture profiles, Valmet analyzed the nip loading and the performance of the press equipment under dynamic conditions with portable iRoll technology. This marked the 500th case to utilize Valmet iRoll technology. With iRoll measurements, it is possible to study profiles quickly and flexibly in real-life conditions with old covers on the machine.
The iRoll data showed that it was necessary to calculate a new crowning shape for the press rolls on TM 4. This was done with Valmet’s CrownSim software, a sophisticated tool that can read existing cover and crown parameters, and calculate the required update from iRoll data to obtain the desired nip load profile shape. For TM 4, this approach meant that the roll covers could be equipped with optimal crowning when they were taken into use.
Second press nip load profile measured dynamically with iRoll portable reveals low edge loading.
New optimized freeform crowning calculated using iRoll data. The target was to increase press nip load in edge areas.
The iRoll analysis revealed the press loading equipment performance, too. The second press nip loading was working correctly, but the suction press roll remained skewed, despite changes in loading levels and attempts to fix it with nip load parameters.
This was finally addressed to by adjusting the height of the flexible joint for the front-side vacuum tubing. The mill maintenance team added shims to prevent the tubing from affecting the nip loading, as well as checking and adjusting the alignment of the press area. These measures improved the symmetry of both the suction press nip and profiles.
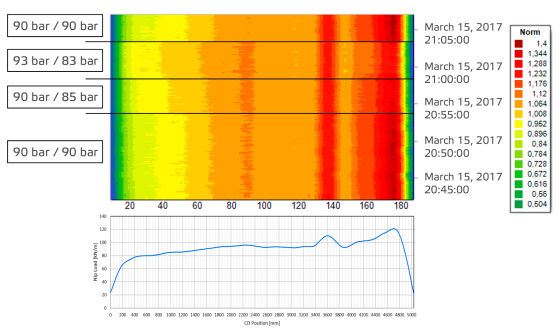
Suction press nip profile during load trials, measured dynamically with iRoll portable, revealing skewed loading conditions.
Targets reached
SsangYong C&B achieved the improvement targets set for optimizing the press nip efficiency of TM 4 tissue machine. The dry content and profiles improved, leading to energy savings through five percent less steam consumption. More energy savings came from a five percent decrease in roll drive loads. The nips now function better, as the skewed loading was corrected and crowning updated.
And finally, the machine speed was increased by up by 30 m/min.
The payback of the cover upgrade and iRoll project has been clear. As a result, Valmet and SsangYong have agreed to continue to cooperate with the same approach for other tissue machine lines at the sister mill, Monalisa Co. Ltd.
Mr. Jong-Dae Byun, Director & Mill Manager, is pleased with the achievements of the project.