Juntai Technology overcomes a shoe press challenge in pulp drying
Jan 17, 2022
A shoe press bottom roll’s poor performance was a restricting factor not only for Juntai Technology’s pulp drying machine but the entire mill. Valmet’s roll service experts swiftly removed the issue.
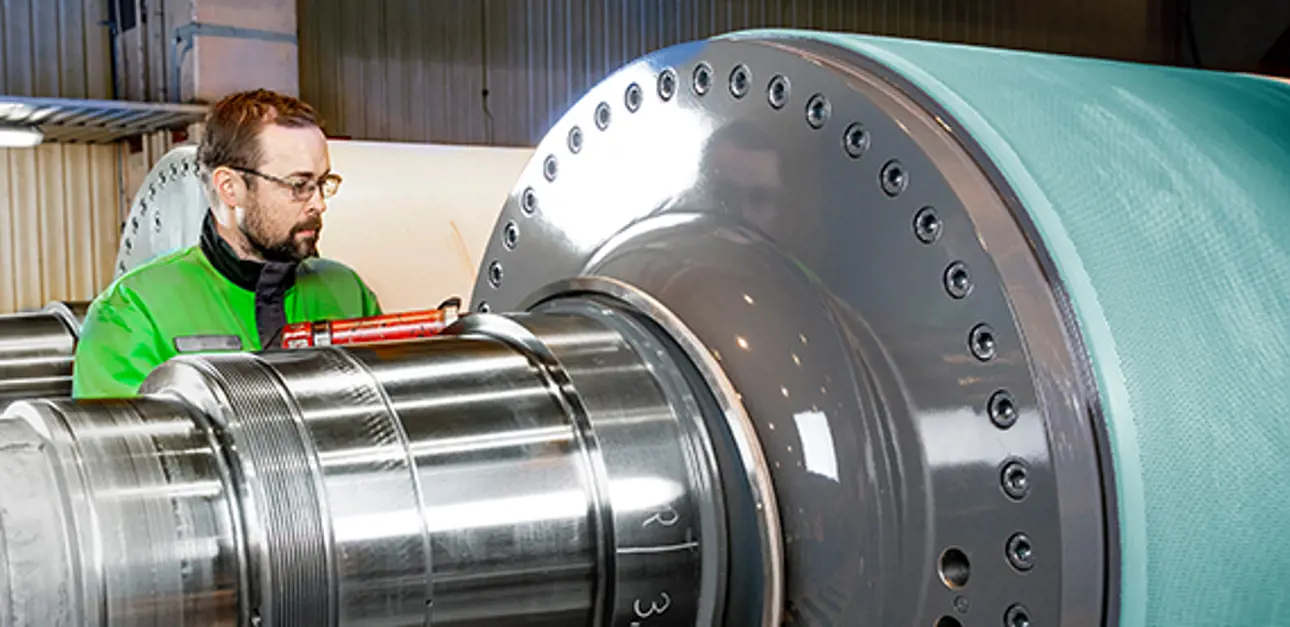
A few years after the start-up of its pulp drying line, Hunan Juntai New Material Technology Co., Ltd. (Juntai Technology for short) in Huaihua, China, encountered a serious challenge with its shoe press. Its performance was unstable, mainly because its nip load could not reach the design value. Several problems, including broken head bolts and cracks in the shell, had a major impact on the pulp drying capacity. As the shoe press was not performing as expected, it presented a shutdown risk for the entire line.
Valmet’s roll service experts called for support
The company’s good cooperation with Valmet dates to 2011. When they need roll service support, Juntai Technology knows who to contact. “After receiving the customer’s request, we sent a roll expert to the site to collect data and check the operating condition of the shoe press counter roll, as well as to analyze and discuss the causes of the roll problem with the customer – and find a solution, of course,” says Valmet’s Product Sales Manager Hu Yunhua.
Valmet’s roll experts and global roll engineers evaluated the problem through a remote connection to the site. They concluded it might be related to the existing roll head structure design, the material used for the head, matching tolerance selection between the head and the roll shell, or processing accuracy.
“The customer chose Valmet as the supplier for a new shoe press bottom solid roll. Valmet’s Finnish roll engineering experts designed a new roll head based on the current roll performance requirements without changing the critical roll dimensions. The shoe press bottom solid roll was processed and manufactured by Valmet in Finland, and the roll surface was covered with Valmet Press Roll Cover VT composite cover before it was delivered to the customer site,” adds Senior Manager of Valmet’s New Rolls Stephen Ren.
Continuous operation for more than two years
The new shoe press bottom solid roll was installed during an annual production shutdown. “During the start-up, we identified structural problems in the original bearing seat seals, accepted Valmet’s suggestions for improvement and redesigned the existing sealing structure. Valmet’s Guangzhou workshop modified the bearing seat sealing structure for testing and delivered the roll to us in January 2019,” recalls Sun Yajun, Pulp Making and PDM Facility Manager, Juntai Technology.
“The shoe press bottom roll is the key equipment of our pulp drying machine, and it was a restricting factor for our entire mill. Based on the current situation, its performance meets our expectations,” says Yajun Sun (left) Pulp Making and PDM Facility Manager, Juntai Technology. Valmet’s Mill Sales Manager Yunhua Hu is on the right.
Since the new shoe press roll was installed, the pulp drying machine has been running continuously and stably for more than two years without failure. The nip load of the shoe press is maintained at 1,000 kN/m in stable operation. “The shoe press bottom roll is the key equipment of our pulp drying machine, and it was a restricting factor for our entire mill. Based on the current situation, its performance meets our expectations,” Sun Yajun continues.
“A good partner we can trust”
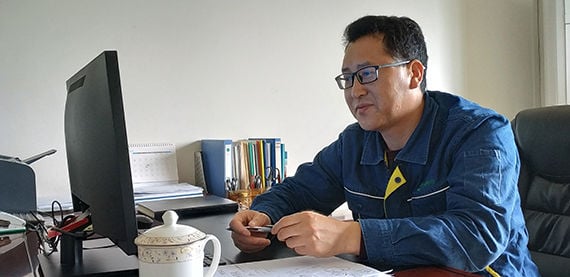
“Valmet can provide a full range of products and services, and is a good partner we can trust,” says Chen Wensheng, Manager, Energy Business Department (former Director of Equipment Management Department), Juntai Technology.
Chen Wensheng, Manager of Energy Business Department (former Director of Equipment Management Department), Juntai Technology, adds: “Valmet can provide a full range of products and services, and is a good partner we can trust. The shoe press bottom roll is a good example. We overcame the challenge with the shoe press and hope Valmet can also recommend reliable and cost-effective products and services in the future that will help us increase production, reduce energy and raw material consumption, and improve quality.”
Juntai Technology, formerly known as Hunan Juntai Pulp and Paper Co. Ltd., is a large state-owned hi-tech enterprise that integrates cellulose manufacturing and sales, comprehensive processing of forest chemical products, power and heating production and supply, and import and export trade.
Valmet can provide a full range of products and services, and is a good partner we can trust.”
The pulp drying machine has been running continuously and stably for more than two years without failure.”
Related articles