Service agreement improves boiler reliability at the Ngodwana mill
Sappi’s Ngodwana mill entered a long-term service agreement with Valmet in 2016. Valmet has since been responsible for the maintenance and shutdown operations of the mill’s three boilers. As a result, the boilers’ performance has met Sappi’s availability and reliability targets.
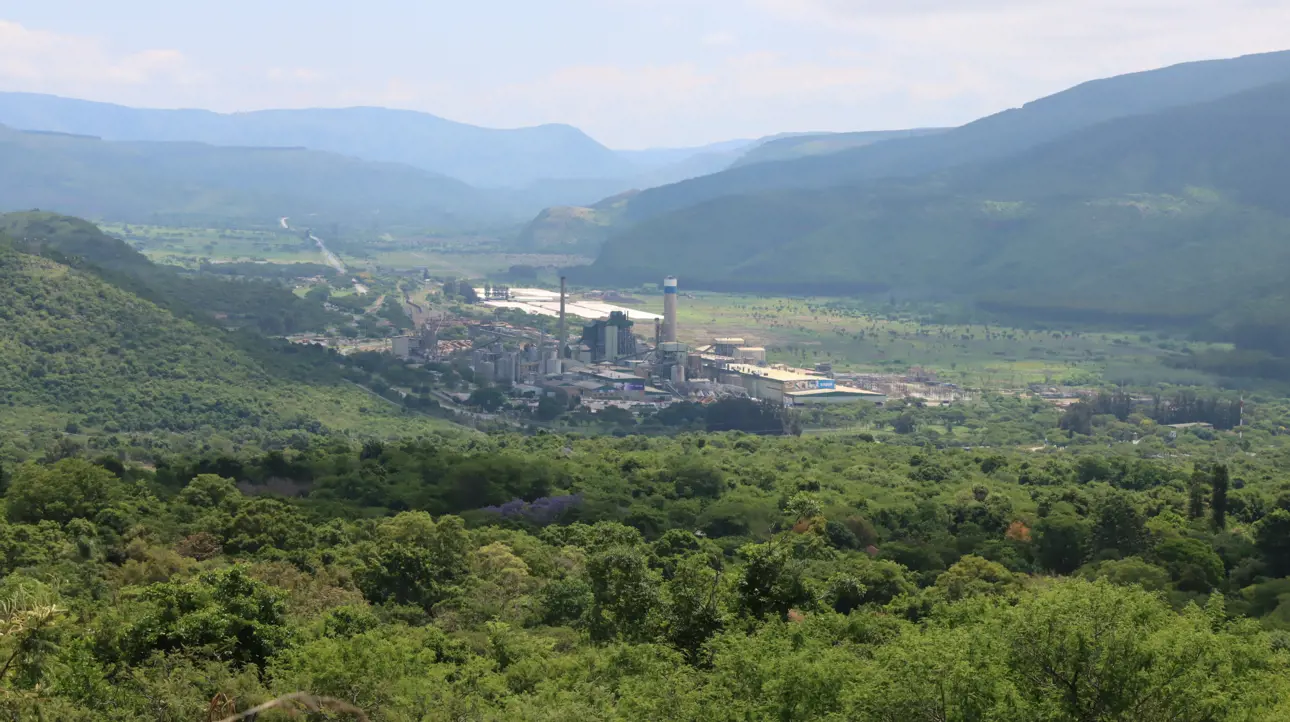
The Sappi Ngodwana mill is an integrated pulp and paper mill located in the heart of Mpumalanga province in South Africa. The mill produces 320,000 tonnes of paper pulp for its own consumption, as well as 380,000 tonnes of newsprint paper and kraft linerboard, and 255,000 tonnes of dissolving pulp.
Sappi Ngodwana and Valmet have cooperated closely since they entered a long-term boiler service agreement in 2016. The agreement covers the maintenance of the mill’s two recovery boilers and a pulverized coal power boiler and includes services such as annual boiler and evaporation plant inspections, shutdown planning and management support, process studies, and spare parts management. Recently, the agreement was again extended to cover the next three shutdowns.
Gopalan Naidoo, Mill General Manager at Sappi Ngodwana, comments:
Sappi’s long-term strategy is to grow in the packaging paper segment, which means the Ngodwana mill is also undergoing an aggressive development plan. We are looking to increase the mill’s capacity in the packaging paper production and the pulping section, and we are therefore currently investing in upgrading the infrastructure at our mill. We believe partnerships like the boiler service agreement with Valmet support our short- and long-term strategies very well.
Gordon Batho, Regional Boiler Manager and Gopalan Naidoo, Mill General Manager at Sappi Ngodwana
Preventive maintenance leads to operational excellence
Valmet’s service agreements are always tailored to meet the customer’s needs. At Sappi Ngodwana, preventive maintenance is the core of the service agreement – regular inspections, maintenance planning and the timely execution of daily maintenance work secure the boilers’ performance without mechanical failure from shutdown to shutdown.
“I think the service agreement is an integral part of our reliability journey – it is an excellent way to mitigate the operational risks in the boiler section. I appreciate Valmet’s will and ability to accommodate our requests with short response times. The main driver to continue the agreement year after year is the skill that Valmet brings to the party,” Gopalan Naidoo says.
Sappi Ngodwana and Valmet have mutually agreed targets that are regularly monitored to evaluate the onsite success. The targets include the shutdown duration, safety record, weld failure rate and unplanned boiler outages. An example of the success of the work is that there have been no tube leaks in four years.
“In addition to Valmet’s ability to innovate and introduce new technologies, I appreciate how they work safely at speed. During the seven years of the service agreement with Valmet, we’ve achieved several key milestones at Ngodwana, and I’m eager to encourage anyone to engage themselves in a similar agreement. We value the good partnership with Valmet and look forward to continuing our cooperation,” Naidoo says.
Latest shutdown a landmark of successful cooperation
Going into the agreement, Valmet appointed a dedicated team with a thorough knowledge of the site and its boilers, thus securing the successful execution of critical maintenance tasks. The roadmap for future upgrades is jointly developed and updated, allowing the customer to plan and budget for upcoming shutdowns well in advance.
The latest shutdown at the Ngodwana mill took place in November 2023. This time, in addition to the regular maintenance work, Valmet conducted several upgrades in the boiler area: a side wall replacement at the larger recovery boiler, as well as burner corner and wall panel replacements at the power boiler. It required extensive planning and site operations management, as Valmet’s onsite headcount at the work’s peak was nearly 150 persons.
Gordon Batho, Regional Boiler Manager at Sappi Ngodwana, comments:
Thanks to Valmet’s support, we were again able to execute the upgrades as scheduled during the shutdown. In my opinion, Valmet’s expertise is crucial for the complex tasks required by such boilers. In general, I value the open dialog and good relationship we’ve been able to develop with Valmet over the years, always keeping the focus on improving the boiler reliability and availability.