Pioneering bio-based raw materials in press felts
Valmet is determined to lower the carbon footprint of their paper machine clothing. As a result of intensive work, Valmet has launched the first press felt containing bio-based raw materials. Valmet Press Felt EMX M Bioneer is here now.
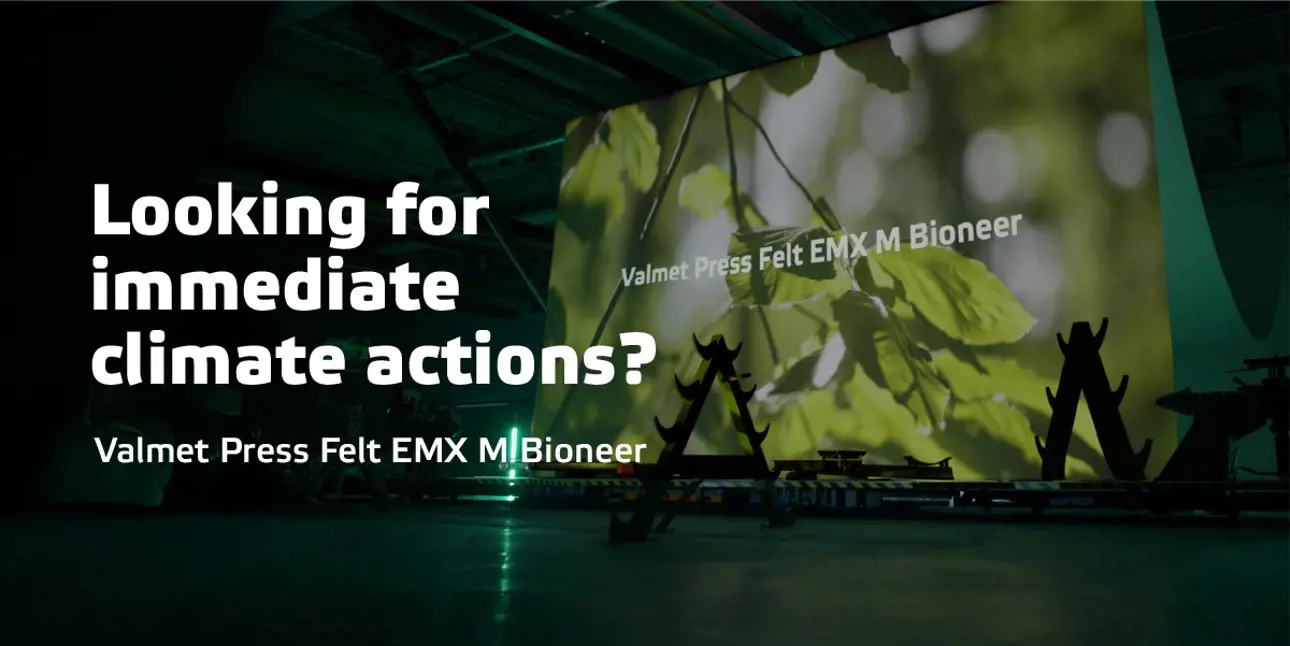
Developing a more sustainable press felt hasn’t been an easy cruise in the fast lane. On the contrary – it’s been a long journey. Indeed, introducing Valmet Press Felt EMX M Bioneer is just the first step.
“Valmet’s Fabrics business unit released its sustainability action plan in 2021, and we’ve since been working to reduce our products’ climate impact. In addition to improving material efficiency and developing recycling practices for used paper machine clothing, we’ve spent hundreds of hours searching for the possibilities to use bio-based or recycled materials in our production. Introducing the first press felt with a lower carbon footprint is an excellent outcome of that work, and I’m really proud of our team’s achievement,” says Katriina Markkula, R&D Manager at Valmet.
Katriina Markkula, R&D Manager, Valmet, and Leena Silakoski, Senior Manager, Press Felts and Belts, Valmet, say that developing more sustainable products is a long journey that needs to be travelled step by step.
What is Valmet Press Felt EMX M Bioneer?
When it comes to quality, Valmet Press Felt EMX M Bioneer is exactly the same as its predecessor, Valmet Press Felt EMX M, a stable press felt with good water handling capacity and a long lifetime – but with a smaller carbon footprint. How is this possible?
In Valmet Press Felt EMX M Bioneer, part of the fossil-based raw material is replaced with a bio-based alternative using a “mass balance” approach.
“In practice, raw materials like forestry residuals and used cooking oil are broken down into monomers (basic organic chemicals), which have identical characteristics to fossil monomers. When these are processed into polymers and further to yarns and fibers, their characteristics remain the same – meaning it’s impossible to distinguish between bio-based and fossil-based materials in the end product,” explains Satu Hagfors, R&D Project Manager at Valmet.
The mass balance approach relies on accurate bookkeeping, and the entire supply chain needs to be certified to ensure that there are no omissions at any stage. Valmet’s press felt production in Tampere, Finland, is certified with the International Sustainability and Carbon Certification (ISCC) PLUS.
Tested for high and consistent quality
Although it is known that partially bio-based yarns’ characteristics are identical to those of traditional yarns made from fossil oil, comprehensive testing has been run, just as with any other product development project.
“The test results show that the quality of this yarn is exactly as good as that of our traditional yarn. We’ve also manufactured some trial felts, and there were no deviations in the production process. Customer trials in paper machines show that press felts made with this yarn perform just as well as those made with traditional yarn. So, knowing that the performance is as good as before but with a reduced carbon footprint, I would say that Valmet Press Felt EMX M Bioneer is great,” says Kati Mikkonen, Senior R&D Engineer, and the Project Manager for the Bioneer project at Valmet.
Press felts are exposed to extreme conditions in pulp, board, paper, and tissue production, and our first priority is to offer high-performing products with a long lifetime.
“The mass balance approach enables the use of bio-based raw materials without compromising product quality, and we’re looking forward to improving our customers’ climate performance with our products – starting with Valmet Press Felt EMX M Bioneer,” says Leena Silakoski, Senior Manager, Press felts and Belts at Valmet.
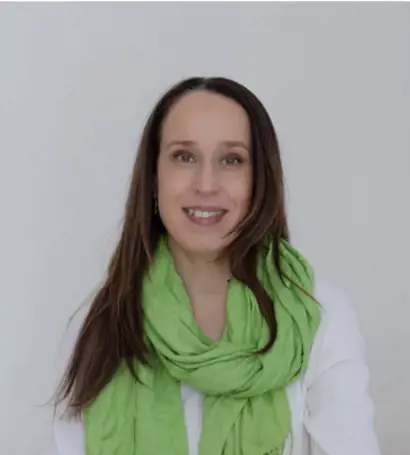
Related articles