Pick-up roll running time extended from four to 14 months
Hamburger Hungaria was troubled by short running times, an unscheduled downtime and extensive maintenance on its PM 7 pick-up rolls. Since the installation of a new Valmet pick-up roll and roll upgrades, the running time has more than tripled.
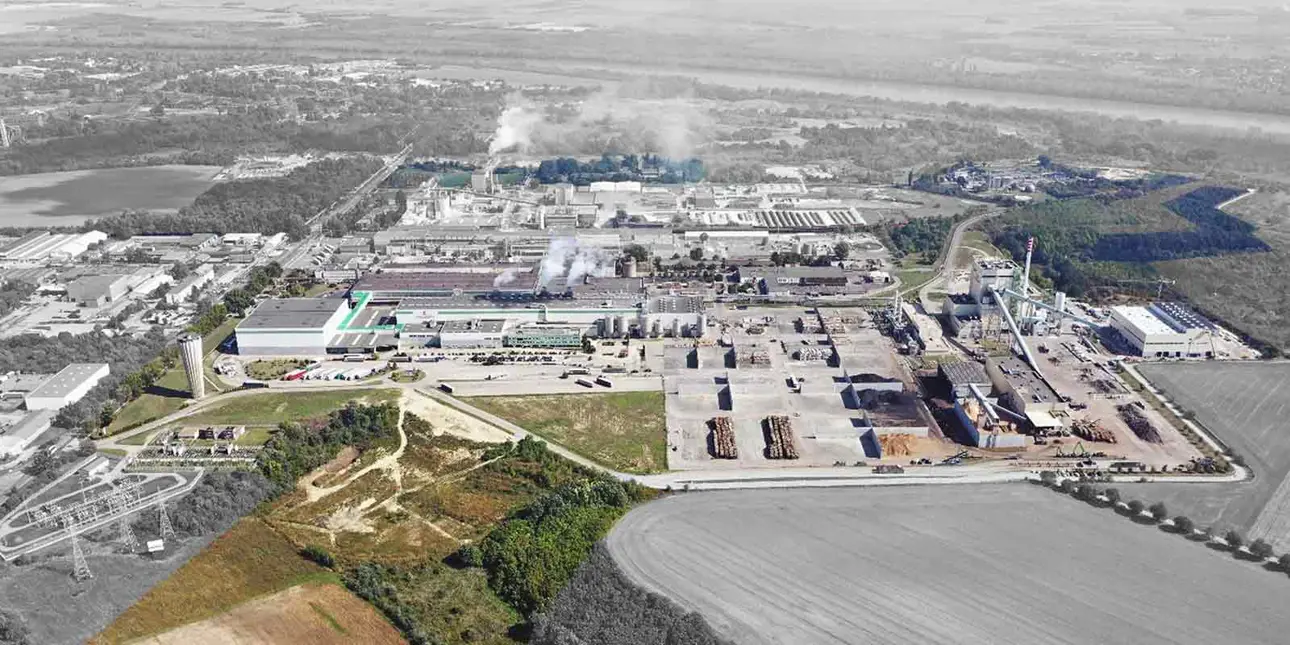
The Hamburger Hungaria mill in Dunaújváros, Hungary, 70 km south of Budapest, has always aimed for better results and has been able to improve PM 7 productivity and efficiency year after year.
Started up in 2009, the containerboard machine produces 100 percent waste-based lightweight brown liner and corrugated medium. It has an annual capacity of approximately 470,000 tonnes, a width of 7.8 m and a maximum original production speed of 1,400 m/min.
There were many challenges on the PM 7 pick-up roll. Its running times were short, requiring additional shutdowns for roll changes. The shell had to be thoroughly cleaned, causing even more downtime and safety risks. Extensive maintenance measures and additional repairs were needed to restore the roll condition. Moreover, axial seal wear was causing vacuum losses.
“We were looking for a solution to extend pick-up suction roll running times by avoiding shell hole plugging and axial seal wearing issues. They had been causing unplanned roll changes every three to four months since the machine start-up,” says Attila Varga, Technical Manager, Hamburger Hungaria. “We wanted to get rid of shell plugging and axial seal wear issues and extend the roll running time to at least 12 months.”
Many upgrades to improve roll performance
In 2019, Valmet delivered two oil-lubricated pick-up rolls with a two-suction chamber solution to the mill.
The rolls were equipped with high vacuum extensions on both sides to improve roll performance and machine runnability, with fewer web breaks. During web transfer, the web adheres to the felt thanks to a vacuum produced inside the pick-up roll, and travels into the press section. If the vacuum effect is removed too soon, the edges of the web may be detached from the felt. Loose web edges will flutter as they travel into the press, increasing the likelihood of web breaks.
In the future, we intend to extend the pick-up running time even more, by up to 24 months.
The delivery also included a Valmet Suction Roll Upgrade Lock Seal to relieve seal strips from the suction roll shell during running, improving the energy efficiency of the roll and extending the lifetime of the suction roll axial seals and shell. As the axial seals have little or no contact with the rotating shell, wear is minimal. As seal friction is minimized, the roll can operate on less energy. Depending on the machine’s layout, size and speed, the annual energy saving potential can be as much as 4 GWh from a single machine. The use of water for axial seal lubrication can be minimized or even completely eliminated. This can entail a savings potential of more than 100,000 m³.
Caption: New Lock Seal axial seals were installed in the pick-up suction box PM 7 at the Valmet workshop
Valmet also delivered a Valmet Suction Roll Upgrade Edge Blow to improve the efficiency of the pick-up roll. It contributes to more uniform web edge pick-up from the forming fabric and prevents the trim traveling with the paper web into the press section.
To improve suction roll seal lubrication, the delivery included Valmet Suction Roll Upgrade Seal Flow. This is an axial seal lubrication shower, which represents the newest technology and features an improved showering process and moisture profiles. Through significantly lower water consumption, it reduces the roll’s environmental impact.
Savings of up to 50 percent can be achieved in the water used in the showers with the Seal Flow upgrade. On a paper or board machine, this can mean annual savings of EUR 2,500–5,000 per roll meter every year (EUR 25,000–50,000 a year on a 10-meter machine). As well as saving money, this will have a positive impact on the service life of axial seals and rolls, moisture poles, and shell and cover lifetime.
Additionally, the rolls delivered to PM 7 featured an adjustable vacuum flow in the second chamber.
Running time more than tripled
The new pick-up roll and upgrades have met the mill’s expectations. “We’re very satisfied with the roll performance. With the new Valmet suction roll including a Shell Flow shell cleaning shower and Lock Seal axial seals, we were able to get rid of shell plugging and axial seal wearing issues. Moreover, the roll running time was extended from four to 14 months,” says Attila Varga.
When the first Valmet pick-up roll was removed in a scheduled shutdown, the axial seals were in perfect condition, even after the long running time. They were reused. No defects due to normal wear were found, and no additional cleaning work was required during roll operation.