Output doubled at Mosaico Tolmezzo
Mosaico Tolmezzo doubled production and gained more reliable operation with high-speed Valmet Trim Collector* system.
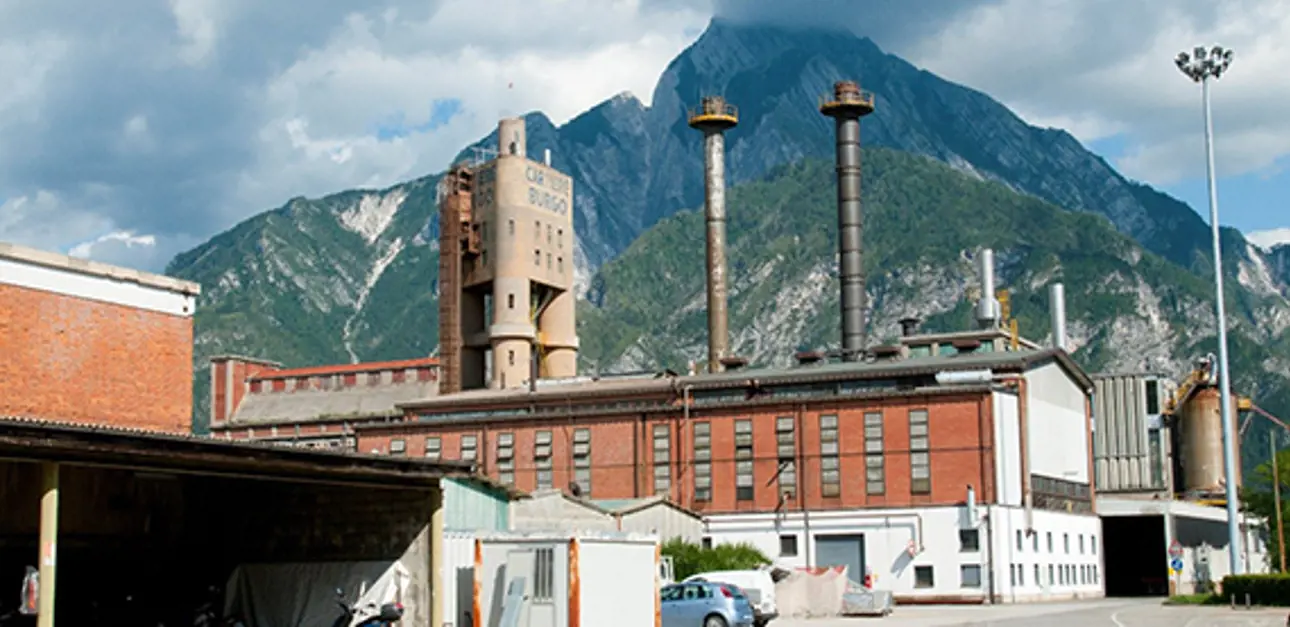
In 2014, the Mosaico Tolmezzo paper mill in northern Italy realized that the old trim removal system in the forming section of their paper machine PM 1 was no longer effective. They installed Valmet Trim Collector system in March 2015, since when the Tolmezzo mill has experienced fewer breaks and increased machine runnability. The new trim collector system has overcome the bottlenecks that had been preventing the mill from doubling its production. PM 1 at the Tolmezzo mill produces machine-glazed (MG) paper with a grade range of 17–40 g/m2. The mill was strongly committed to finding the optimal solution to their trimming problem. “With a speed of 450 m/min and 20 centimeters of trim, we had water jets removing the stock from the fabric. After increasing the speed followed by a rebuild of PM 1, our system revealed its limits, with a lot of breaks and build-up of pulp and fibers,” says Furio Azzopardo, Mill Manager at Tolmezzo.
For the mill, a traditional trim removal system that sets down the trim on the fabric was not an alternative. “We needed a system that removes the stock from the fabric before the nip of the pick-up,” says Azzopardo. “We discussed it with colleagues and competitors, but they had nothing for the geometry of our machine. Since we had already talked about the technical solutions with Valmet and knew that they had done similar installations elsewhere, it did not take us long to decide to order the trim collector system.”
Valmet Trim Collector allows doubled speed and production
Valmet Trim Collector solution cleans the trim area effectively and allows controlled recovery of high-quality trim for reuse as fiber raw material. The solution is installed so that the trim can be blown off the surface of the fabric.
“Valmet's trim collector is designed specifically to work at high speeds, so after Tolmezzo rebuilt PM 1, we just needed to find the optimal setup,” explains Maurizio Sala, Mill Sales Manager at Valmet.
The trim collector start-up took place smoothly in March 2015, and the mill was immediately able to run the machine at speeds of up to 700 m/min. After some additional fine-tuning in May to increase the speed further, the system showed its true capabilities. Running steadily at 900 m/min, there was still some margin left for increasing the speed. With the help of trim collector, the mill has now achieved its target of doubling both speed and production. All the saved broke goes to PM 3 for reuse.
“Actually, the faster the speed, the better the system works,” Azzopardo laughs. The mill has also noticed that the new solution is not only effective, but easy to use and adjust. “For us, it’s important that we can change the speed without having to touch the system.”
![]() |
“Our biggest interest from the very beginning was to avoid breaks and have a good trim. We have achieved all these targets more quickly than expected,” says Furio Azzopardo, Mill Manager (right), with Maurizio Sala from Valmet (left). |
Estimated payback in just a few months
In terms of better runnability and increased machine speed, the mill has achieved all its targets more quickly than expected. “We were aiming to reach our targets within the first year, but we reached maximum speed in only two months,” Azzopardo says. “The start-up curve was very impressive and the payback time for Valmet Trim Collector was less than six months.”
The amount of web breaks has also decreased substantially. “Before, we had two or three breaks a day due to the previous trim removal system running at 500 to 550 m/min. Now, three or four days can pass without any breaks. Sure, we still have breaks and there are areas for improvement, but our detectors show that the time efficiency of PM 1 is now 97%. This includes overall breaks, shutdowns and felt changes.”
Cleaner trim area and happy operators
There are also other benefits, like a decreased need for maintenance and improved cleanliness around the trim area. By fall of 2015, PM 1 had not required any maintenance, just one planned shutdown.
“Of course, you can still see fibers on the machine, but now they don’t cause breaks, which is important for us. The best thing is that our operators are now happy, because they don’t even have to touch the system in order to clean it! Before, they had to clean the trim area four or five times every shift. Now the system runs smoothly and we only do the cleaning every two or three days. Life is so much easier for them now.”
Installing Valmet Trim Collector allowed the Tolmezzo mill to reduce breaks, increase machine runnability and overcome bottlenecks that were preventing the mill from doubling their production.
*earlier known as TrimRecovery