Maximizing the pulp drying availability with Valmet’s services
Mar 5, 2025
As a pulp producer, you know the importance of the pulp dryer for your mill – as a world-leading technology expert, we know how to secure its availability and runnability every day, year after year.
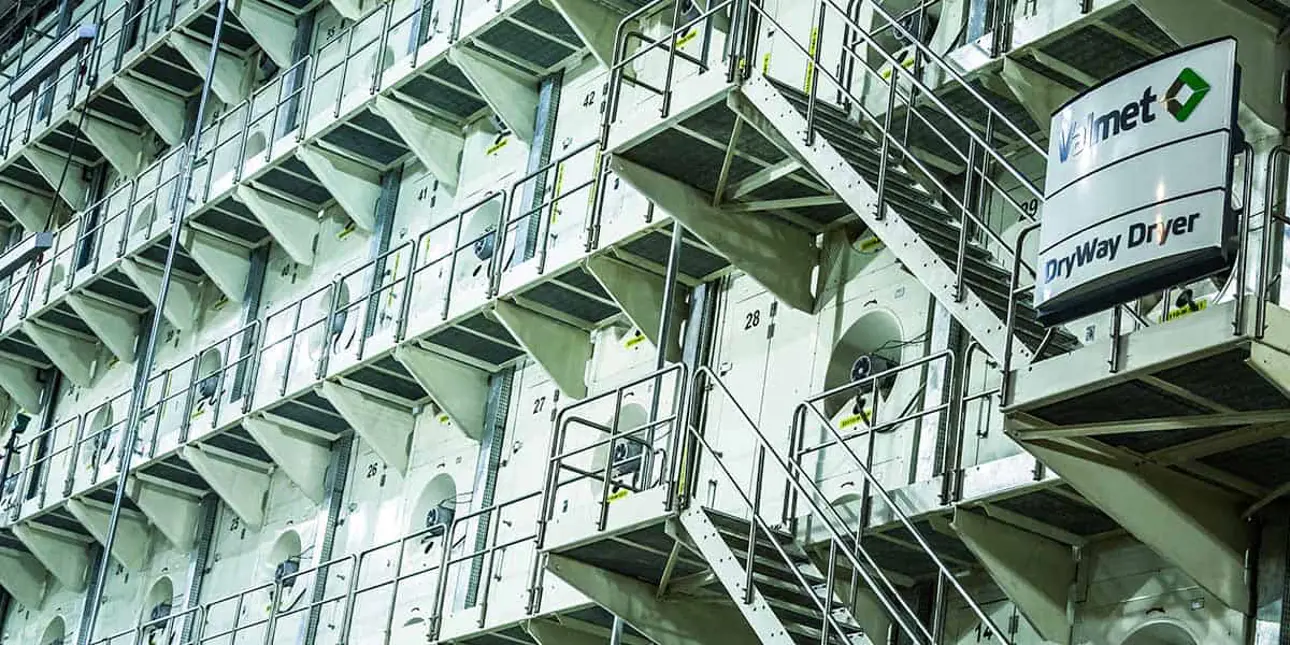
Valmet offers a wide variety of services for pulp drying process: workshop reconditioning services, rolls and roll covers as well as roll maintenance and upgrade services – all improving the pulp drying performance at customer sites around the world.
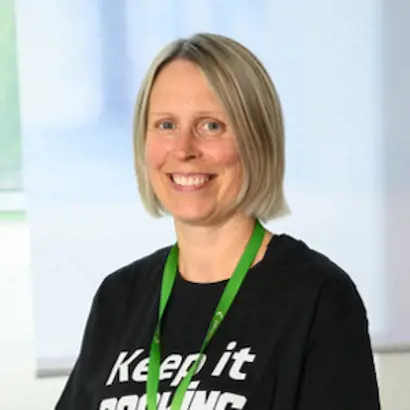
“Globally, there are about 300 pulp drying lines in operation, and 120 of them are Valmet’s own installed base. With our expertise and know-how, we are however totally capable of servicing competitor equipment as well. With Valmet’s services, our customers can maximize the availability of their pulp dying,” says Ulla Kanerva, Global Technology Manager, Roll Covers and Maintenance at Valmet.
“Valmet is the global leader in state-of-the-art pulp drying technology. Together with our long experience in the service business – over the decades, Valmet’s specialists have solved hundreds or even thousands of customer challenges – it has helped us build a know-how that no other company has. That, I believe, differentiates us from our competitors,” Kanerva says.
Reconditioning for a more sustainable future
Valmet’s services are designed to meet our customers’ needs throughout the entire life cycle of their pulp drying line, securing stable running with minimum unplanned shutdowns. As such, our solutions enhance energy efficiency, cost efficiency, material efficiency, and safety of pulp drying, thus improving the sustainability of customer operations
To further boost sustainability, Valmet offers a variety of cost-effective reconditioning services, that also help to diminish the carbon footprint of pulp producers. For example, machine screen rotors are widely reconditioned with good results.
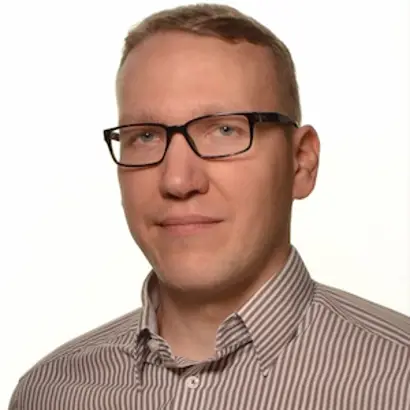
Jarmo Viitaharju, Global Technology Manager, Workshop Services at Valmet, says:
“When a rotor is reconditioned, its screening performance is as good as if it was new. Its capacity is also brought back to the desired level, maintaining operational efficiency. By choosing reconditioning instead of manufacturing a new rotor, CO₂ emissions are reduced by 3.7 tons per unit. Additionally, the process saves 90% of the steel material required for production, reducing the demand for raw materials and minimizing environmental impact.”
Understanding the customer needs
Based on Valmet’s experience, pulp producers are looking at improving their pulp drying’s machine reliability and availability, cost efficiency, sustainability and energy efficiency, machine runnability, and safety.
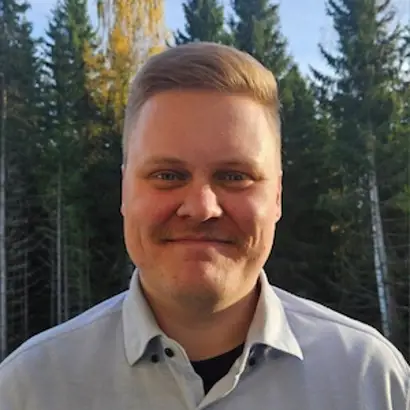
“Our offering emphasizes services that improve machine runnability and availability, as it is the key behind reliable production without costly interruptions – our customers’ first priority. The others are of course important as well, and they often go hand in hand like for example cost efficiency and energy efficiency,” says Lasse Janhunen, Global Technology Manager, Roll Covers and Maintenance at Valmet.
References play an important role in the customers’ decision-making.
“We know that our customers are keen on knowing how their competitors have solved certain challenges or what kind of technological solutions they have in use. The power of real-life case examples is huge, and we are proud to be able to share so many of our customers’ success stories,” says Jarmo Viitaharju.
Find out how we have helped our customers to improve their pulp drying – read case examples below
Case: Extended running time with suction box cleaning shower upgrade
Suction rolls have a tendency of drawing pulp into the suction box internals and to the space between the suction box and the shell. This additional mass can limit the suction roll dewatering capacity and impede the rotation of the shell thus requiring greater driving power.
One of Valmet’s customer mills struggled with short roll change interval, only 12 months, due to pulp mass accumulation in the suction box.
To improve the situation, Valmet proposed and delivered a suction box cleaning shower upgrade. In the upgrade, the suction roll was equipped with an additional shower that clears excess paper pulp thus reducing the need for maintenance and cleaning.
After the upgrade, roll running time was extended from 12 months to 24 months. Other benefits were longer maintenance intervals, improved energy efficiency and dewatering of the suction box, reduced moisture variation, and extended axial seal life.
Roll internals after 6 months of running (before upgrade) and roll internals after 12 months of running (after upgrade)
Case: Reliable roll cover performance in pulp dryer
In pulp production, quality and reliability are the key to profitability. In 2023, a new pulp drying line was started up at LD Celulose’s mill in Brazil, immediately leading to an extraordinary achievement. The pulp drying line ran for over 270 days without any web breaks. In addition to having the right machine design to handle the unique properties of the dissolving pulp, roll covers played an important role in the successful start-up.
The pulp drying line was equipped for example with Valmet Press Roll Cover PT rubber covers on the wire turning roll and second press roll in a combi press, and Valmet Press Roll Cover VT composite cover on the shoe counter roll.
Valmet Press Roll Cover VT has been successfully applied in many green field pulp drying lines’ shoe counter rolls, reaching running times of as long as seven years.
Valmet Press Roll Cover VT is an excellent cover solution for shoe counter rolls – it is tough and wear resistant cover with excellent chemical and hydrolysis resistance.