Improving press performance step by step
After a four-phase improvement project, Thai Cane Paper enjoys lower steam consumption, better runnability, higher paper dryness, longer felt lifetimes, and vacuum energy savings in its PM 2 press section.
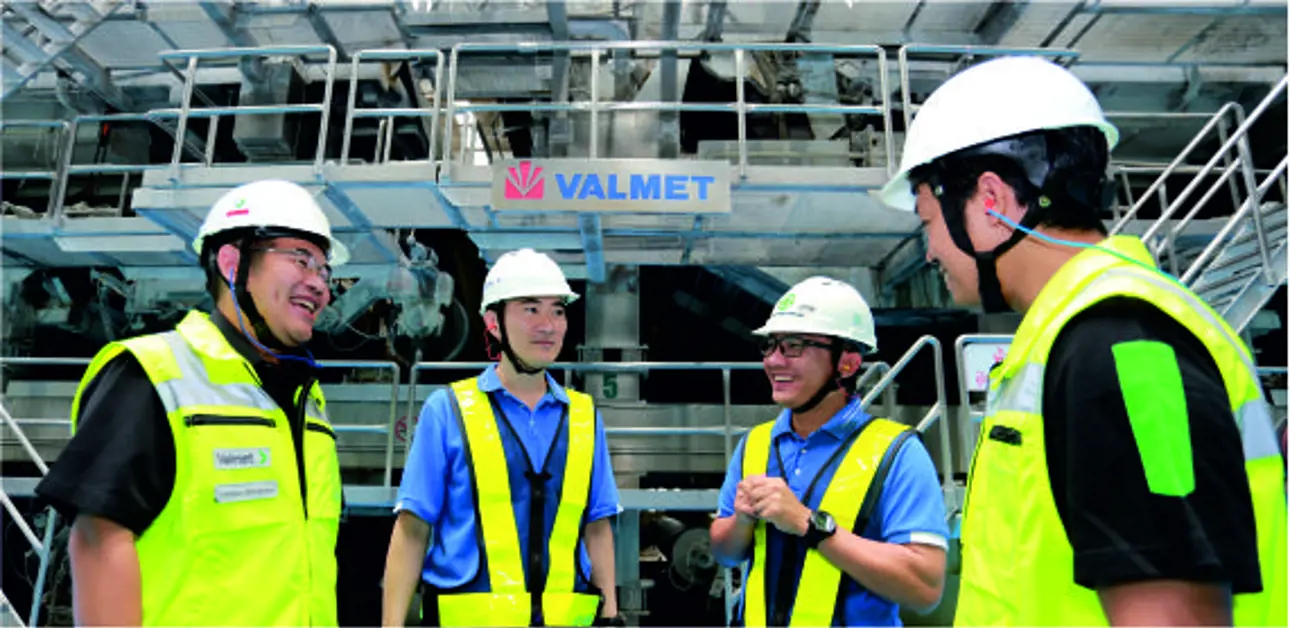
Operating the press section of a paper machine is demanding, but it offers chances for optimization. The main factors affecting performance are the press felts, roll covers and vacuum system. Changing any of them immediately impacts the others, and ultimately the overall performance of the press section.
Thai Cane Paper is a subsidiary of Packaging Business in SCG, one of the largest kraft paper producers in Thailand. They had been having challenges with the press section of their PM 2. Press felt lifetime was too short, dewatering was poor, and sheets tended to drop off during pick-up or follow the top-ply wire. There were also issues with felt marking.
The mill tackled these problems step by step in close cooperation with Valmet's Laem Chabang Service Center and global experts.
Focus on press felts and dewatering
Due to the high Uhle box vacuum capacity of a turbo blower installed in 2014, existing traditional felt designs were not performing well. Their lifetime had dropped from 60 days to just 35 days, and average paper dryness after the press was 47.6 percent, sometimes dropping as low as 44.7 percent.
Valmet's study and felt trials showed that the felt designs were quite open and ran dry, as there was not enough hydraulic pressure under the nips. Valmet Press Felt SPMs with a 100-percent woven laminated structure and special soft paper-side yarns were installed. The felt design matches the vacuum capacity, carries more water and is more compressible under nip load to create effective hydraulic pressure. An optimized felt batt combination and a soft top-side base weave minimize felt marking even when the felt is dry.
Optimizing the vacuum system
The next phase focused on the vacuum system to eliminate paper drop-off from the pick-up roll and its tendency to follow the top-ply wire due to the poor vacuum capacity of the transfer suction box. To cope with them, the mill had to open a vacuum pump. Changing to perforated Uhle box covers improved
Uhle box dewatering with less air flow and less vacuum system control tuning, and closed the extra vacuum pump. Vacuum optimization increased felt lifetimes, too.
Further improving sheet dryness and roll performance
To further improve sheet dryness and roll performance, a Valmet Press Roll Cover PP was installed on the second press. Combining it with the Valmet Press Felt SPM and the optimized vacuum system immediately improved operating results. Average dryness after the press immediately rose from 49 to 51.6 percent. The total drive load of the second press fell to 14 percent. With the new covers, press rolls can be operated without water-cooling, which saves money.
Training ensures high performance in the future, too
During the final phase of the project, Valmet trained the mill staff to maintain the results and high performance.
“Valmet is our partner and gave us good services and support for this improvement. So, we would like to thank the Valmet team for providing this four-phase approach to our PM 2,” says Sontaya Tunsaranuwat, Production
Department Manager at Thai Cane Paper.
Lower steam consumption, longer felt lifetime, energy savings
All in all, the results of this project have been impressive. The biggest is the average steam consumption decrease, down from 45.6 to 40.2 tonnes an hour. Suitable felt air permeability combined with vacuum optimization using
perforated covers and vacuum control system modifications have allowed the mill to permanently close the vacuum pump without sheet drop-off problems. With a vacuum level recommendation for the Uhle boxes and the Valmet press felts and roll covers, the mill has achieved higher dryness after the press and extended felt lifetimes, along with improved quality. The Valmet press felts and roll covers have also improved nip dewatering and reduced drive loads, resulting in energy savings.
On this Shared Journey Forward, every factor – press felts, vacuum optimization, roll covers, service, training, cooperation between the mill and Valmet – was vital for the successful outcome.
Related articles