Improved workflow and efficiency at Opal´s Botany mill with Valmet Mobile Maintenance application
Opal’s Botany mill was the first to implement Valmet Mobile Maintenance Application in daily use in 2022. A year later, the app is considered an important tool in preventive maintenance and tackling every board and paper-makers' challenge – unplanned downtime.
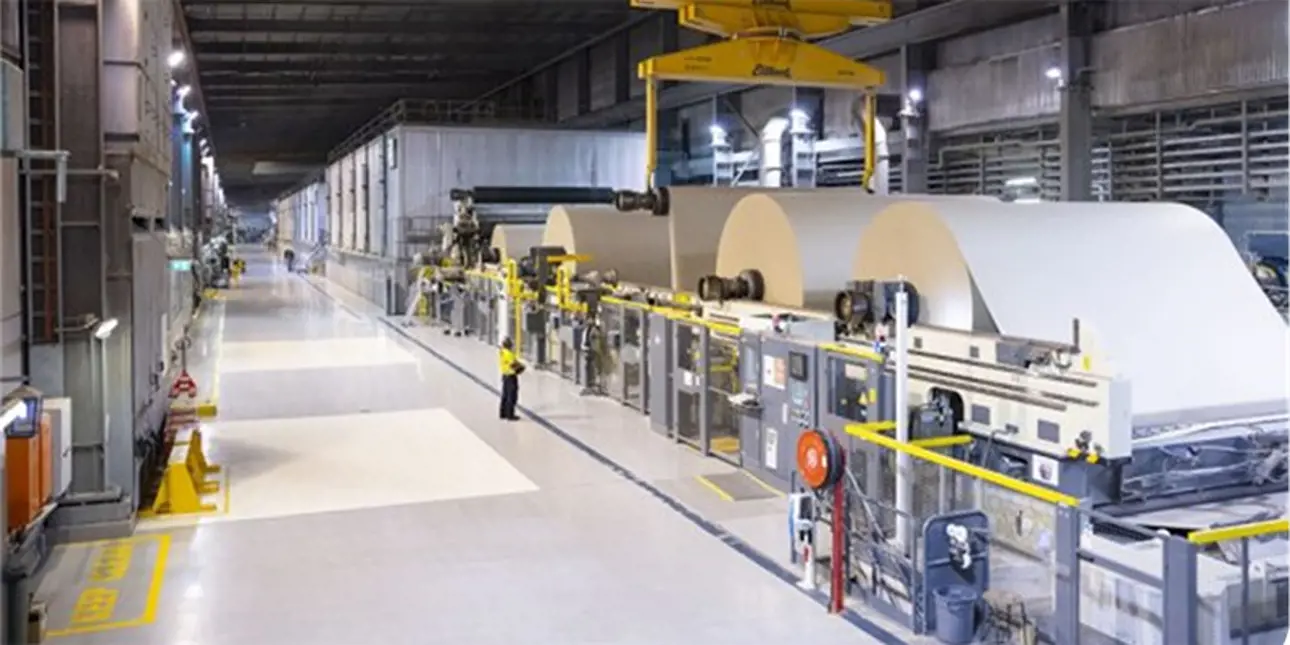
Opal’s recycling and manufacturing facility is located in Botany, New South Wales, Australia, where paper has been produced since 1902. The mill’s most recent production line B9 was commissioned in 2012 and is now recognized as an industry benchmark for containerboard manufacturing. For over ten years, the mill’s maintenance and reliability function has been entirely managed by Valmet.
Application development was a joint commitment
Opal’s Botany mill was involved in the development of the application and was the first one to implement it in daily use.
“Opal is dedicated to continuously improving the net overall equipment effectiveness at their mills, and the Mobile Maintenance App was selected as one of the initiatives to help them reach their targets. Thanks to the customer’s commitment and the good co-operation between Valmet and mill’s various teams from management to IT, the application meets our needs on site very well,” says John Naude, Site Manager, Mill Maintenance Operations at Valmet.
Currently, the application is being used by around one hundred people either on their mobile phones or other portable devices.
“We did have to upgrade some of the mobile phones to be NFC tag compatible, but other than that, the installation of the app was simple. The application itself is easy to follow, and largely self-intuitive. Naturally it took some time before we had everyone onboard, as acquiring new tools always means adjusting to new ways of operating,” Naude says.
Improved ways of working lead to better performance
In practice, the Mobile Maintenance Application has replaced pen and paper as the means of raising corrective notifications about the condition of the board machine.
Before, we used to write down notifications on our notepads and transfer them to the workorder management system when we had time – sometimes at the end of the day, many times even later. With the App, we are able to report notifications real-time with improved data quality through the ability to quickly attach photos and videos,” Naude explains.
“This in turn has improved the decision-making process as well as the execution and follow-up of tasks, eventually leading to improved reliability and less unplanned downtime. Given our team raises approximately fifty notifications a month utilizing VMM, the App makes our lives a lot easier and continues to add value to improve the maintenance efforts on site,” he continues.