How Valmet’s Tube Thickness Prediction Application improves boiler performance and maintenance
Feb 12, 2024
The development of a tube thickness measurement program began as a thought to create more structure and finished as an interactive application in Valmet Customer Portal, with many benefits for both the customer and Valmet. Prolonged lifespan of boiler tubes, control over maintenance costs and prevention of unplanned shutdowns are only some of the gains.
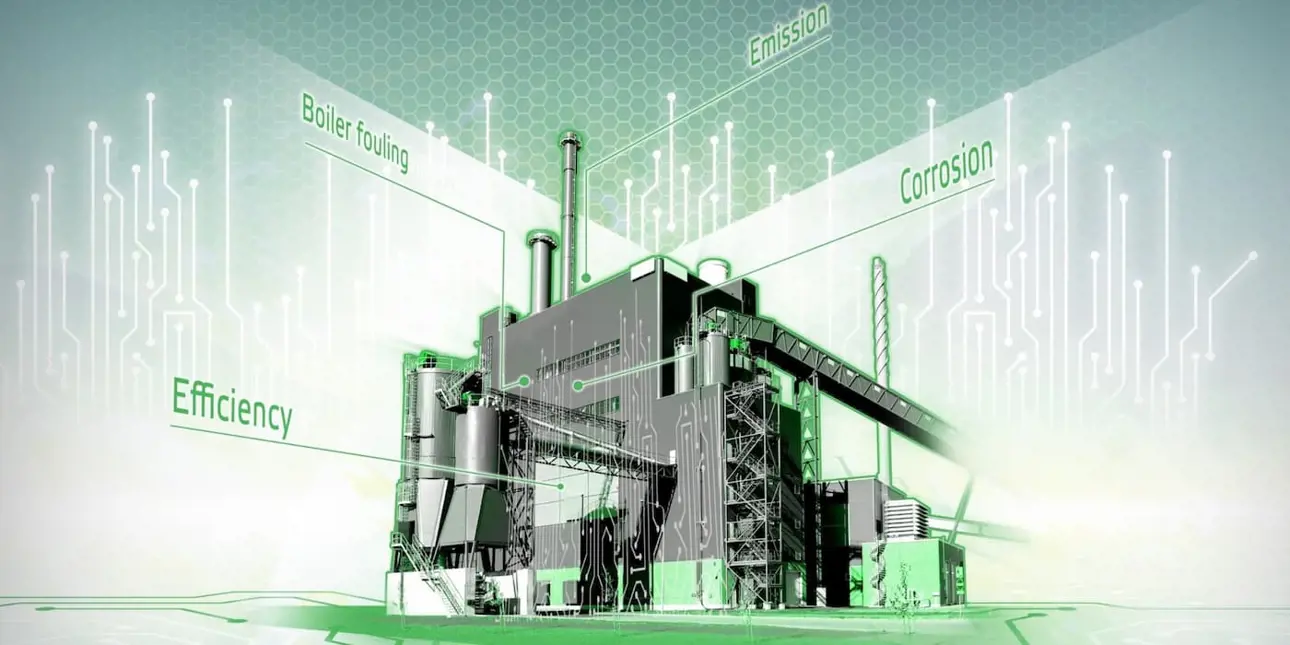
A systematic approach for future benefits
The thought of a systematic approach to the measurement of thickness in boiler tubes was developed in 2014 as a result of too many excel sheets with differentiating measurement points, making it hard for both the customer and Valmet personnel to make qualitative analyses of the scattered data. “With a systematic measurement program, the goal was to create a clear structure to help customers foresee the future development of their boiler tubes and help prevent the risk of unplanned leakages and shutdowns”, Anders Edsand, Senior Product Engineer Agreements, Maintenance Specialist, Valmet explains.
Forward with the development of a customer application
Through internal discussions and cooperation between different functions at Valmet, the project got started and demanded both analysis of customer needs, development of data handling and creation of interactive visuals. Anders explains the motivation behind the development; “How can we create a system that prevent leakages, erosion, corrosion and potentially unnecessary changes of tubes through changes in mechanics, processes and performance”. The successful teamwork resulted in a user-friendly application with an illustrative summary of boiler wearing spots in Valmet Customer Portal, easily accessible for both the customer, Valmet Inspectors, product and maintenance engineers.
From scattered data to preventative customer actions
The initial step when joining the measurement program is importing historical data from the customers previous tube thickness measurements into the application, to summarize the critical points where future action is needed, up to 5 years ahead.
A Valmet inspector will conclude an initial analysis of the imported data and propose a written action plan in the application. Every year ultrasonic inspections will be performed by Valmet or a third-hand party, providing new data input to the application via a pre-defined template. Signs of corrosion or flue gas channeling/erosion, fuel usage, temperatures and unstable combustion are also considered during the inspections and taken into the analysis for the best proactive decisions ahead.
“If there are signs of erosion a proactive solution might be to strengthen that part of the tube with tube shields to prevent both an unplanned leakage and change of tubes. Furthermore, a change of fuel or temperature might show effects of corrosion down the road, but the application allows us to see the effects early on and propose preventive actions to prolong the lifespan of the tubes”, says Anders.
A solid foundation for future customer development plans
The Tube Thickness Prediction Application has been up and running since 2014 and agreements have been made with customers all around the globe. The new version of the application has created great interest by our customers, and it is a great improvement providing all parties with a clear visual overview and a system that provides reliable information for analysis and preventive measures. If the customer already has a Service Agreement together with Valmet, the data from the application will be an important discussion point and input for the future development of the whole plant. Anders concludes; “The application will move forward with continuous improvements for optimal usage, together with our customers”.