Excellent results with Valmet’s ceramic press roll covers at Stora Enso Guangxi
Recently, Valmet successfully delivered the second press ceramic cover to Stora Enso’s Beihai mill’s BM 1. This repeat order benefited from the successful execution of a press roll optimization project in 2020. BM 1’s press section fully meets the mill’s production requirements.
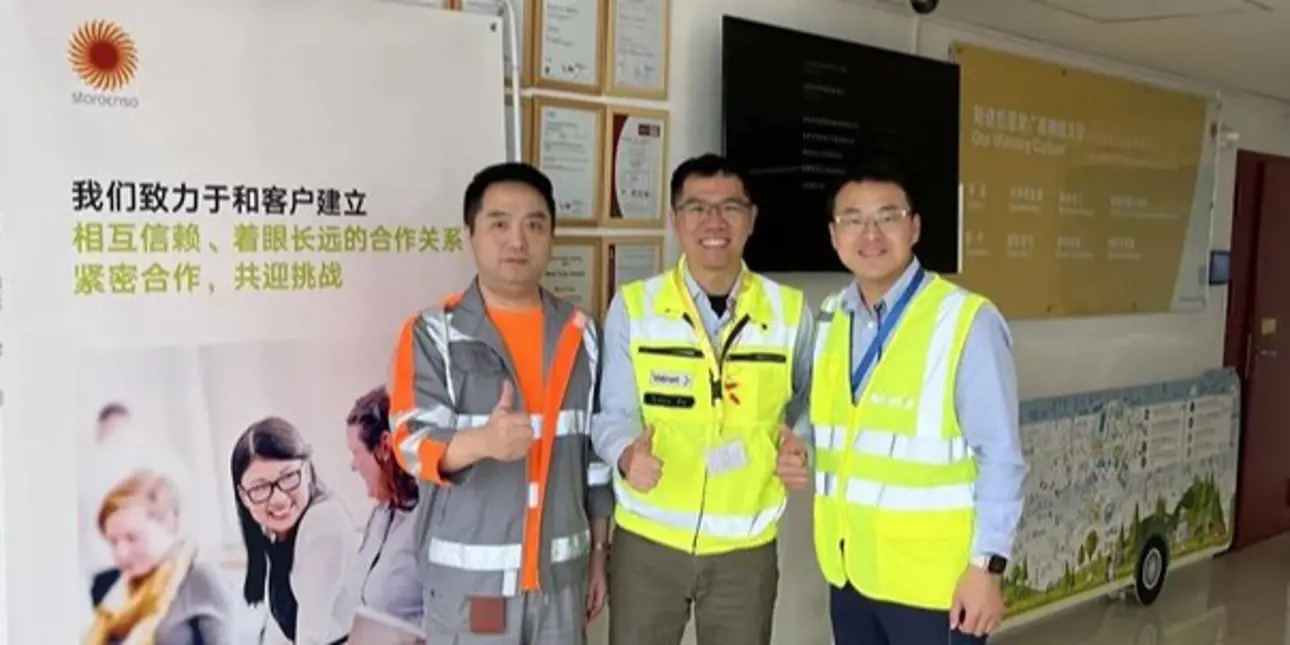
Stora Enso has always been committed to delivering high-quality products, emphasizing the stability of product quality and production process control reliability.
We have great trust in Valmet’s professional and service capabilities. Since the introduction of the ceramic cover and the application of light linear pressure in the smoothing press, the rear calender press’s operation has been more flexible, and the product bulk and paper smoothness have been effectively optimized and improved,” says Zhang Wei, BM 1 Production Manager, Stora Enso Beihai mill.
Stora Enso’s Guangxi mill uses the world’s most advanced technology and equipment to provide renewable solutions for packaging cardboard users, especially high-end liquid packaging cardboard (LPB), to ensure better performance in different end uses at all times. End users will benefit from the product’s stable quality, light weight, and food safety features. At the beginning of 2020, Stora Enso’s Beihai mill set the press section optimization project as the key improvement project of the year and set clear goals with the Valmet team to further improve the finished product’s surface quality and meet high-end customers’ increasingly strict quality requirements.
Targets were set to:
- Improve the peeling effect of the paper sheet in the smoothing press
- Improve the final product’s IGT index
- Optimize the interlayer bonding of the paper sheet
- Improve the surface smoothness of the paper sheet
Combining the mill’s historical data, the two parties reached a consensus on the improvement goal – to upgrade the original rubber cover to a ceramic cover, and eliminate the possible negative impact of the roll cover change. The two parties jointly formed a project team that included process and equipment professionals and conducted detailed discussions, from the early scheme selection, start-up plan, and execution stage to the later installation and testing stage.
Valmet Press Roll Cover PJ/PD family
The results of the ceramic cover are remarkable
The first ceramic roll cover delivered was installed on December 25, 2020. Before the start-up, both sides’ teams carried out corresponding inspections and adjustments of the doctor blades, online cleaning system, hydraulic system, interlockings, and other related press components. The final result met the expectations of both parties.
At the beginning of the project, customer selected two products as the target product types. According to the data after the start-up, the board product’s IGT index can meet expectations perfectly, and the board’s interlayer bonding strength and surface smoothness have been improved.
“What satisfies us is that we’ve since tested more product types, and all types of products have been able to meet our production index requirements with the aid of the press section optimization project to date. The successful application of the ceramic roll cover in PM 1 has not only improved the finished product’s quality, but we also noticed its effect on improving the dilution water profile. It also provides a wider operating window for the rear calender,” says Fu Zishan, Senior Manager, Roll Coating and Maintenance, Service Business Line, Valmet.