Doctoring for top runnability
When Indah Kiat Pulp & Paper Perawang (IKPP) was looking to further boost machine runnability and performance, they challenged Valmet’s specialists to find potential areas for improvement. A plan was made to review the entire doctoring process.
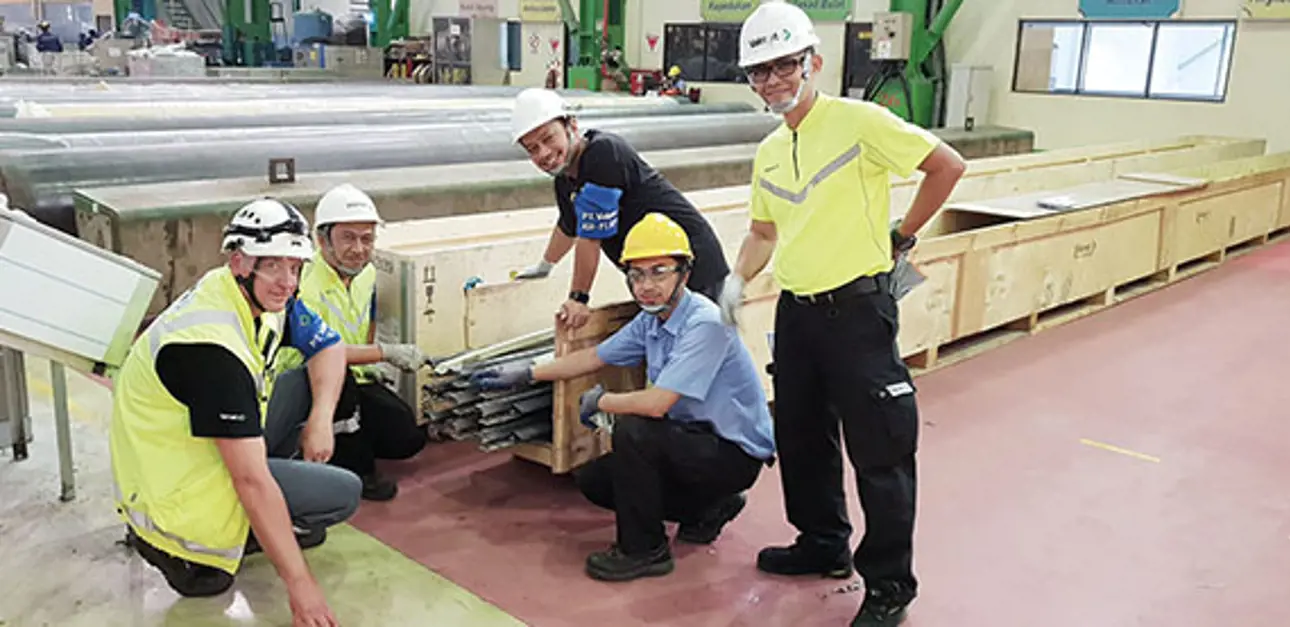
Picture above: From left: Hannu Eerikäinen, Valmet; Ginanjar, Valmet; Tandi Muharam, Valmet; Aska Ramadhan, APP and Rusman Rianto, Valmet.
Indah Kiat Pulp & Paper Perawang mill is one of Asia Pulp & Paper’s biggest mills. It is located on the island of Sumatra in Indonesia. The fully integrated mill produces some 800,000 tonnes of pulp and around 1.2 million tonnes of paper and board annually.
The cooperation between Valmet and IKPP Perawang Mill started in 2012. At the time, a PM 6 rebuild project was coming to an end. The mill was actively looking for opportunities to further boost machine runnability and performance, and Valmet’s specialists were challenged to find potential areas for improvement.
“We used the recent machine rebuild project as a base for collecting machine data and evaluating performance indicators. At first, the machine faced pre-dryer breaks and occasional fiber passing problems, and some holes were also detected in the paper. After thorough analysis and several discussions between the customer and our team, doctoring was identified as the tool for improvement,” says Global Technology Manager Pasi Viitasalo from Valmet.
Review of doctoring process
PM 6 is 10,500 mm wide and has a design speed of 1,500 m/min and a capacity of 400,000 tonnes per year. It produces woodfree coated and uncoated papers. During several on-site studies, all doctoring positions were checked, and their current status was documented. An improvement plan was made to cover the whole doctoring process.
“The positions needing immediate focus were clearly identified by our doctoring specialists. We scheduled a doctor blade holder replacement project and prioritized the positions in need of immediate action. Our initial delivery included Valmet Doctor Holder Compact blade holders, doctor blades, pneumatic control boxes and fixing screws, all carefully selected for each position. We replaced the outdated doctor blade holders with the latest technology. In addition to superior doctoring performance and the easy maintenance of our doctor blade holders, we were able to meet the customer’s expectations of a short delivery time in the first installation,” says Viitasalo.
“New blade holders enable easier maintenance, with a time saving of up to 50 percent.”
Continuous benefits
Good results in the initial doctoring improvement project led to continuous cooperation between IKPP Perawang mill and Valmet.
“We work together regularly, and we’ve been able to further improve the doctoring process. In addition to a better doctoring result, we’ve achieved less doctoring-related downtime and easy holder maintenance operations. We’ve also been able to reduce the customer’s net working capital tied to the doctor blade inventory with the optimized doctor blade types the machine requires,” continues Viitasalo.
Easier maintenance
The latest delivery of another 17 doctor blade holders was finalized last year.
“We’ve been very satisfied with Valmet’s doctor blade holders, so we’ve renewed our order. Compared with conventional ones, Valmet Doctor Holder Compact blade holders enable easier maintenance. The time saving is up to 50 percent, and we require less manpower. Changing or cleaning doctor blades as the machine is running has increased overall efficiency by 3 percent. And Valmet offers good support during the startup,” says Aska Ramadhan from IKPP Perawang Mill.
Reduced costs
Valmet offers a wide range of doctoring products, including doctor blades, blade holders and doctoring accessories. The offering is the most cost-effective on the market, targeting optimal blade lifetimes, energy savings and improved safety.
“We tackle the challenges paper and board makers face from the continuous need to reduce paper making costs. Doctoring plays a key role in modern paper machines when the aim is good runnability combined with the lowest possible costs. One good way to achieve all this is to strive for an effective doctoring process,” concludes Viitasalo.
TEXT Pasi Viitasalo and Marianne Valta
Article published in Forward magazine 2/2019.