Do you know how to keep your wash press in perfect shape throughout its entire lifecycle?
Dec 11, 2024
We do! Valmet is the one-stop-shop for all wash press related services regardless of the brand – be it spare parts or consumables, services such as shutdown planning, roll reconditioning, or maintenance services, or various upgrade or improvement projects boosting performance, safety or sustainability.
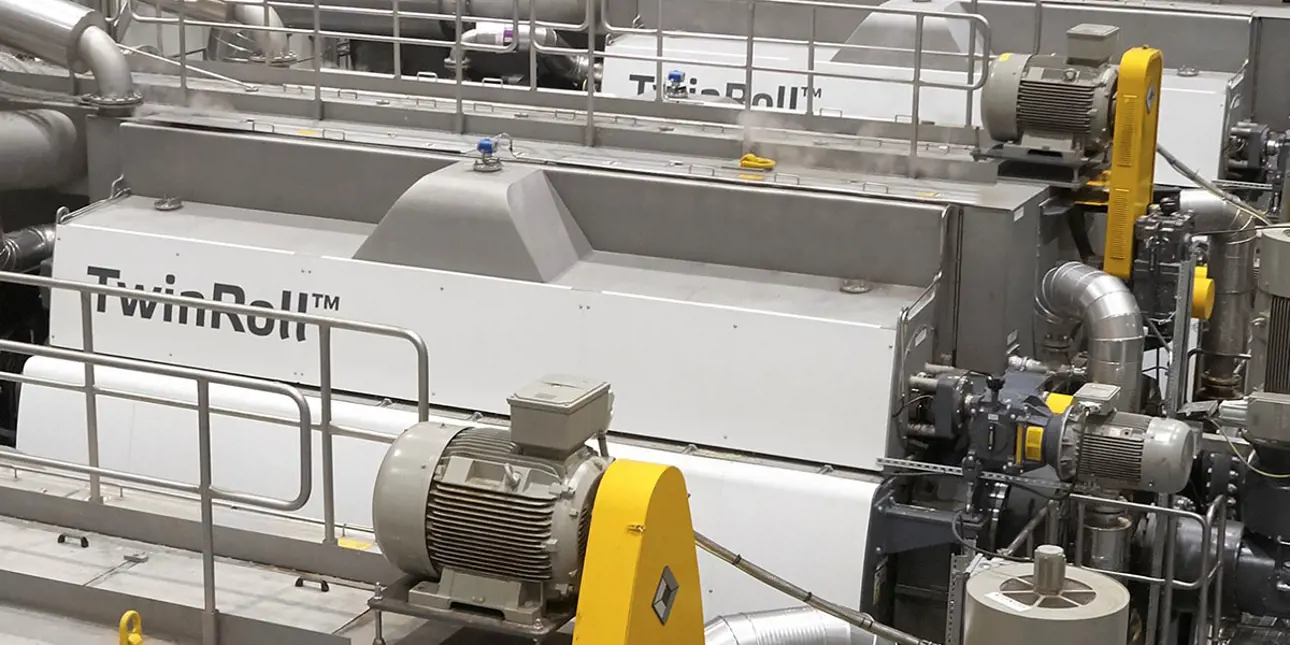
Valmet has a global installed base of over 1600 TwinRoll presses and the know-how to service also competitor wash presses at pulp mills around the world.
“With Valmet’s support, our customers can keep their equipment operating reliably, maximize the energy and cost efficiency of their fiber line, and optimize their production throughout the entire lifecycle of their wash press.
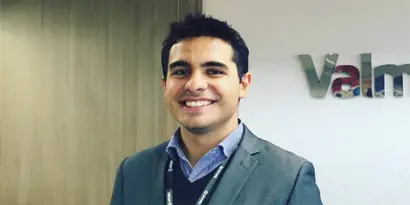
"Thanks to our long experience, we know all wash presses by heart and can offer services or technology updates that best fit the customer’s needs – regardless of the brand or the age of their wash press,” explains Murilo Vali, Global Product Manager at Valmet.
Valmet’s Wash Press Services offering covers the entire lifecycle of the customer’s equipment. Depending on the maturity of the equipment, the services are tailored to ensure a fast start-up curve and to establish efficient maintenance practices (-2 to 5 years), to maintain high productivity level (5 to 20 years) and to upgrade for competitiveness or to modernize to meet market needs.
The right combination of services in every stage of the wash press lifecycle
The key term in Valmet’s wash press services offering is lifecycle. Understanding the lifecycle of a wash press helps you in budgeting, planning daily maintenance activities and shutdowns, scheduling upgrades and improvements, and optimizing the efficiency of the wash press and the entire fiber line.
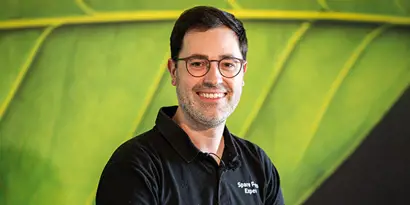
“The foundation for successful wash press operation is created before the startup, and that is why we often support our customers already at the investment phase. A properly done lifecycle cost analysis (LCC) is an excellent tool to understand the effects of certain choices made even before the wash press is installed. After all, money spent today is paid back later – for example in the form of increased availability or smaller operational costs,” says Tiago Voos Senior Manager for daily spare parts at Valmet.
“For those customers operating a more mature wash press, I’d like to say: keep calm and contact us. It’s never too late to establish efficient maintenance practices to maintain high productivity level or respond to changing market needs through tailored upgrades,” he adds.
Be proactive – and get the most out of your wash press
Whether it’s about spare parts, maintenance or equipment upgrades, proactiveness always pays off. Juha Ruotsi, Global Technology Manager for roll workshop services, has seen it many times.
“It’s not at all unusual to operate twenty years without properly servicing the rolls. As one fiberline can have as many as 16 rolls, it’s more than likely that at least one of them eventually breaks down if not inspected and reconditioned regularly. Rolls are not something you just pick out from your warehouse, so it’s clear that proactive roll maintenance pays off,” he says.
In addition to physically examining the rolls and other parts of the wash press, Valmet offers a variety of remote monitoring services through Valmet Industrial Internet applications that help you keep track of your wash press’s condition.
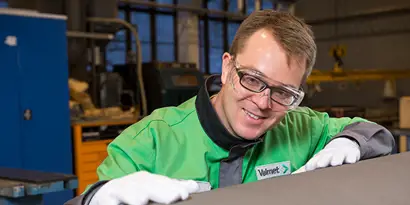
"The better you know your equipment, the better decisions you can make related to maintaining or even improving its condition and performance.”
If you don’t want to stress about it, you can rely on Valmet’s expertise and we will deliver services that guarantee the reliability and efficiency of your wash press throughout its lifecycle – not forgetting your safety or sustainability targets,” Juha Ruotsi says.
Proven track-record of successful real-life examples
Valmet has manufactured, serviced and refurbished wash presses for decades, which means that Valmet’s experts have built themselves a superior know-how in wash presses and related processes.
Many times, the cooperation between Valmet and the customer starts with a challenge – how to improve the performance of the wash press, how to make its operation less costly or how to diminish its climate impact, just to name a few.
Over the years, we’ve seen numerous real-life examples of successful cases resulting in zero unplanned shutdowns, lowering the chemical consumption by 30%, or increased outlet consistency up to 6% units. How can we help you?